Robotisation relief - Gain an edge with modern technology and professional support
Increase efficiency, reduce investment costs and grow your business with the opportunities presented by the robotisation allowance. Find out how you can gain up to 50% in reimbursement for your industrial robot deployment between 2022 and 2026.
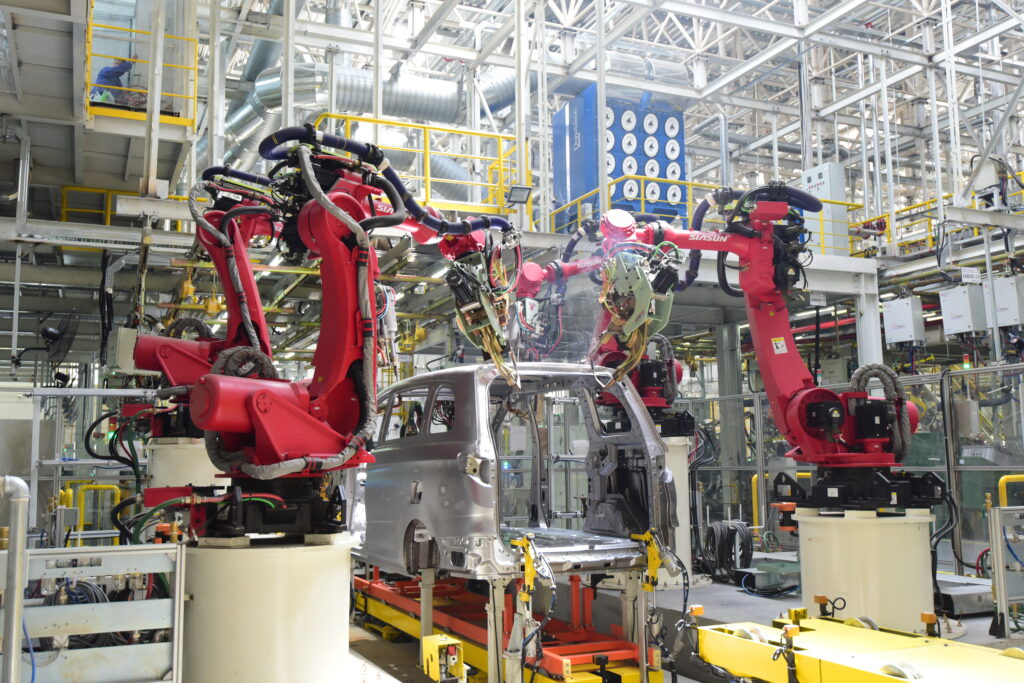
Why take advantage of robotisation relief?
The robotisation allowance is a unique opportunity for entrepreneurs who want to invest in modern technologies and increase the competitiveness of their company. The introduction of industrial robots makes it possible not only to automate repetitive activities, but also to increase product quality, reduce lead times and minimise the risk of human error. Thanks to the relief, you can deduct from your tax base as much as 50% of the costs incurred for robotisation between 2022 and 2026, which realistically reduces investment costs and increases the profitability of your business. This is a solution dedicated to companies that want to develop in line with the idea of Industry 4.0 and not fall behind the competition.
Who can benefit from robotisation relief?
For which companies is the relief intended?
The robotisation allowance was created with all entrepreneurs in mind - whether they run small, medium or large companies. It does not matter what industry you operate in - the key is that the investment is related to the automation of production processes.
Both manufacturing entities and service companies that implement industrial robots into their processes can benefit from the relief. This is an excellent opportunity for companies that want to increase productivity, optimise costs and modernise their operations.
Formal requirements
In order to be eligible for the robotisation allowance, several basic conditions must be met. First of all, the investment must be related to the implementation of new, factory-unused industrial robots or peripheral equipment. The costs must be incurred between 2022 and 2026 and properly documented in the accounts. In addition, the entrepreneur cannot account for the same costs under other tax credits or grants. It is also crucial that the robots and related expenses are used in the company's business activities.
What expenses are covered by the robotisation allowance?
Eligible costs
The robotisation allowance includes a broad catalogue of expenses that you can deduct from your tax base. Eligible costs include:
Purchase or lease of new industrial robots - automatically controlled, programmable machines with at least three degrees of freedom, used in production processes.
Software and control systems - purchase of licences, robot management systems, integration into existing production lines.
Accessories and peripherals - running tracks, positioners, turntables, motion sensors, cleaning stations or other robot support components.
Health and safety equipment - health and safety equipment directly related to the implementation of robotisation.
Training for employees - courses and workshops to prepare staff to operate new machines and systems.
What are industrial robots according to the regulations?
According to the statutory definition, an industrial robot is a stationary or mobile, multi-tasking, programmable device with at least three degrees of freedom, capable of exchanging data in digital form with other devices and systems. Robots must be integrated into ICT systems and monitored by sensors or cameras. Only if these conditions are met does the expenditure qualify for relief.
How does the robotisation relief work?
Deduction mechanism
The robotisation allowance allows you to deduct as much as 50% of eligible costs incurred for the implementation of industrial robots and related expenses from your tax base. This means that you can account for a total of 150% of costs: 100% as a standard deductible cost and an additional 50% in relief. This solution significantly reduces the effective investment costs and accelerates the return on the implementation of modern technology.
Limits and exclusions
It is worth remembering that the amount of the deduction cannot exceed the income obtained by the taxpayer in a given tax year from business activities (excluding income from capital gains). The deduction cannot be used in relation to expenses financed by grants or other public funds. It is also crucial that the costs are correctly itemised in the accounting records to avoid problems during a possible audit.
Step by step - how to benefit from robotisation relief?
Steps to implement the relief
Investment analysis and audit
We carry out a detailed analysis of your project to see which expenses qualify for relief and how best to account for them.Separation of eligible costs
We assist in the correct accounting and documentation of the costs incurred to meet all formal requirements.Preparation of tax documentation
We prepare a set of necessary documents, including a list of costs and the relevant attachments to the tax return.Filing a return and accounting for relief
We support you in correctly accounting for the relief in your annual tax return and monitor the entire process until the procedure is completed.
The most common mistakes and how to avoid them
The most common mistakes include: incorrect separation of costs, deduction of expenses for used equipment, lack of required technical documentation or accounting for costs already financed by subsidies. With our help, you minimise the risk of errors and are assured that the entire process will run in accordance with the regulations.
Professional assistance in obtaining relief for robotisation - our offer
How can we help you?
Implementing robotisation and correctly accounting for tax credits requires not only knowledge of the regulations, but also experience in cost analysis and preparation of documentation. Our partner with many years of experience with this type of project will provide comprehensive support at every stage of the process:
It audits the investment and we identify all eligible costs.
Verifies the accuracy of accounting and tax documentation.
Prepares a set of documents to settle the relief.
It supports you during tax audits and in your dealings with the authorities.
With our help, you can focus on growing your business and we'll make sure you get the most out of your robotisation relief.
Why trust us?
Our experience, our individual approach to each client and working with a company that has been assisting with these types of projects for over 15 years guarantee tax security and maximise the benefits of your investment. By working with us, you minimise the risk of formal errors and gain confidence that your company will take full advantage of the support available.
Do I incur any costs?
The audit itself and verification of whether your project is eligible for submission is free of charge. Subsequent costs depend on the programme and are determined on an individual basis.
Ready to implement robotisation?
Don't wait any longer! Contact us today and find out how we can help your business reach new levels of productivity.
Make an appointment for a consultation
Return on Investment in Robotics Calculator
Investment costs
-Production parameters
+Staff parameters
+Economic parameters
+Calculating the results ...
Results of the combined analysis
Financial summary
Production analysis
Cost analysis
Long-term analysis
Results of employee savings analysis
Financial summary
Employee cost analysis
Long-term analysis
Results of the analysis of increased production
Financial summary
Production analysis
Long-term analysis
Attention: The results presented by the ROI calculator are indicative and for informational purposes only. The calculator has been designed to illustrate the potential opportunities and approximate return on investment for robotisation, but should not be the sole basis for making business decisions.
Actual results may differ significantly from the calculations presented due to numerous variables beyond our control, such as market fluctuations, changes in energy costs, unforeseen downtime, changes in legislation and taxation, or individual production process conditions.
We recommend treating the results of the calculator as a starting point for further, more detailed analyses, taking into account the specifics of your company.
Wide range of technologies - we will find the optimal solution for your production
Our robotic workstations offer the flexibility to choose from a variety of technologies, allowing you to precisely tailor a solution to your specific production needs.
With our experience and knowledge, we will help you choose the technology that best optimises your production processes, increases productivity and quality.
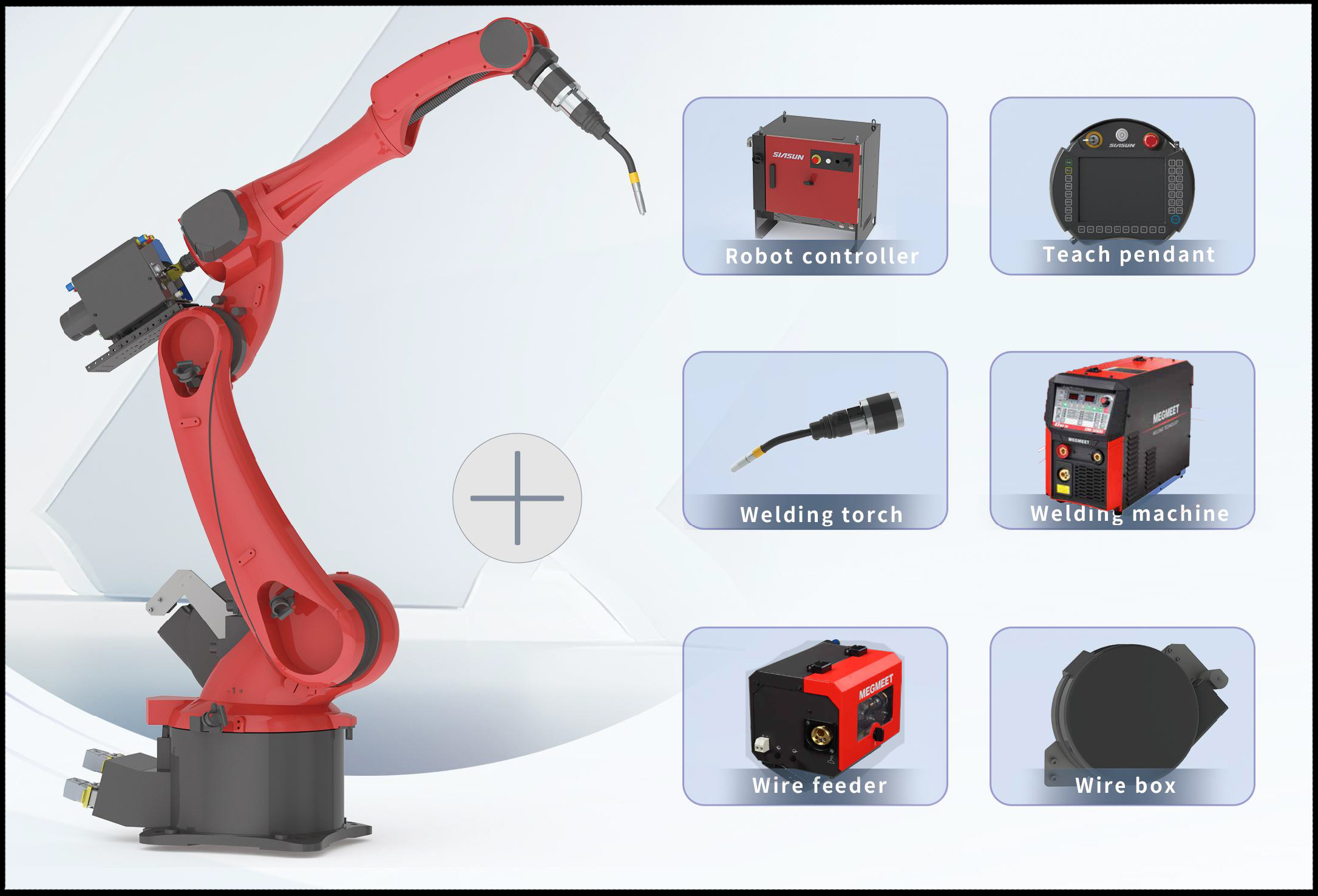
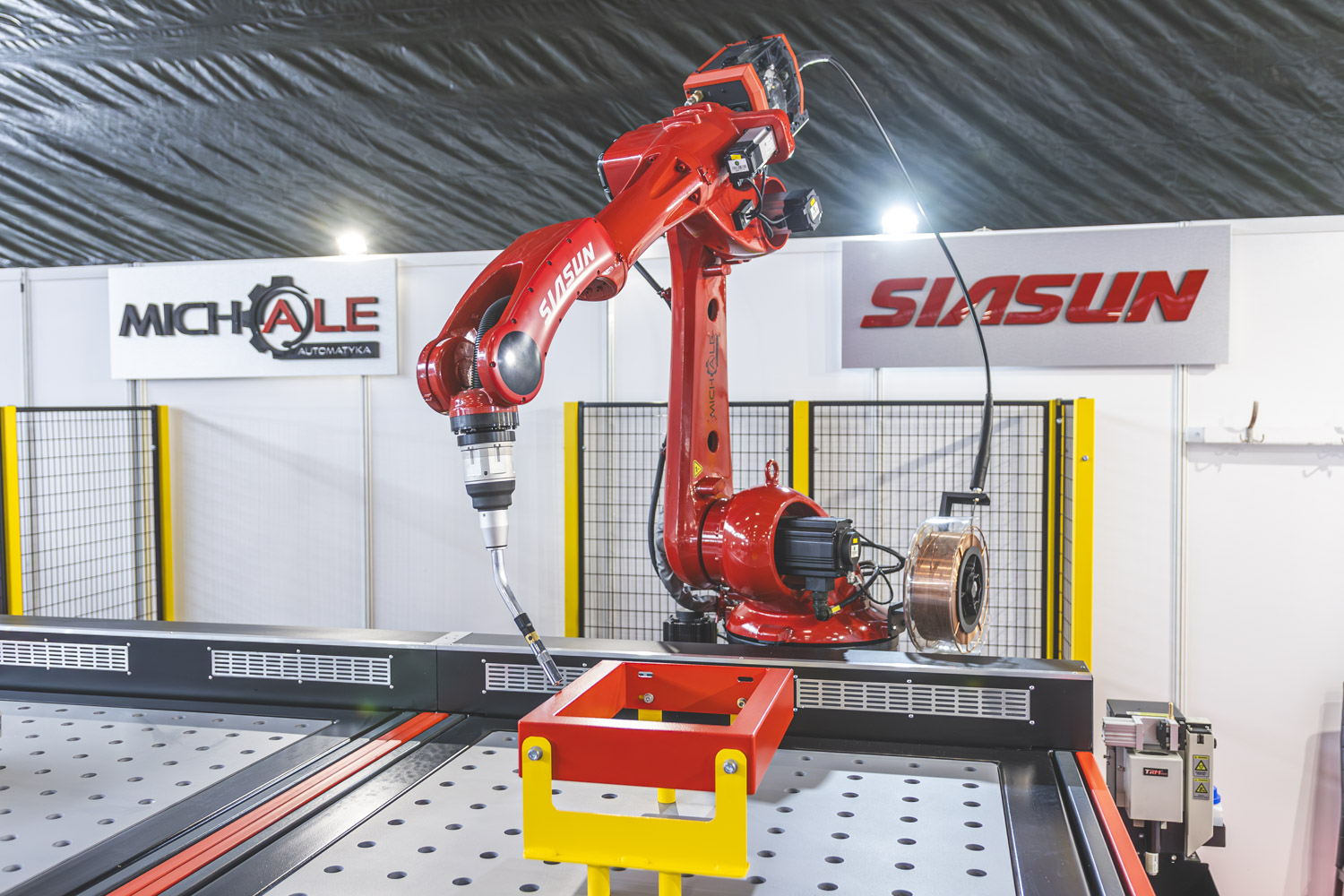

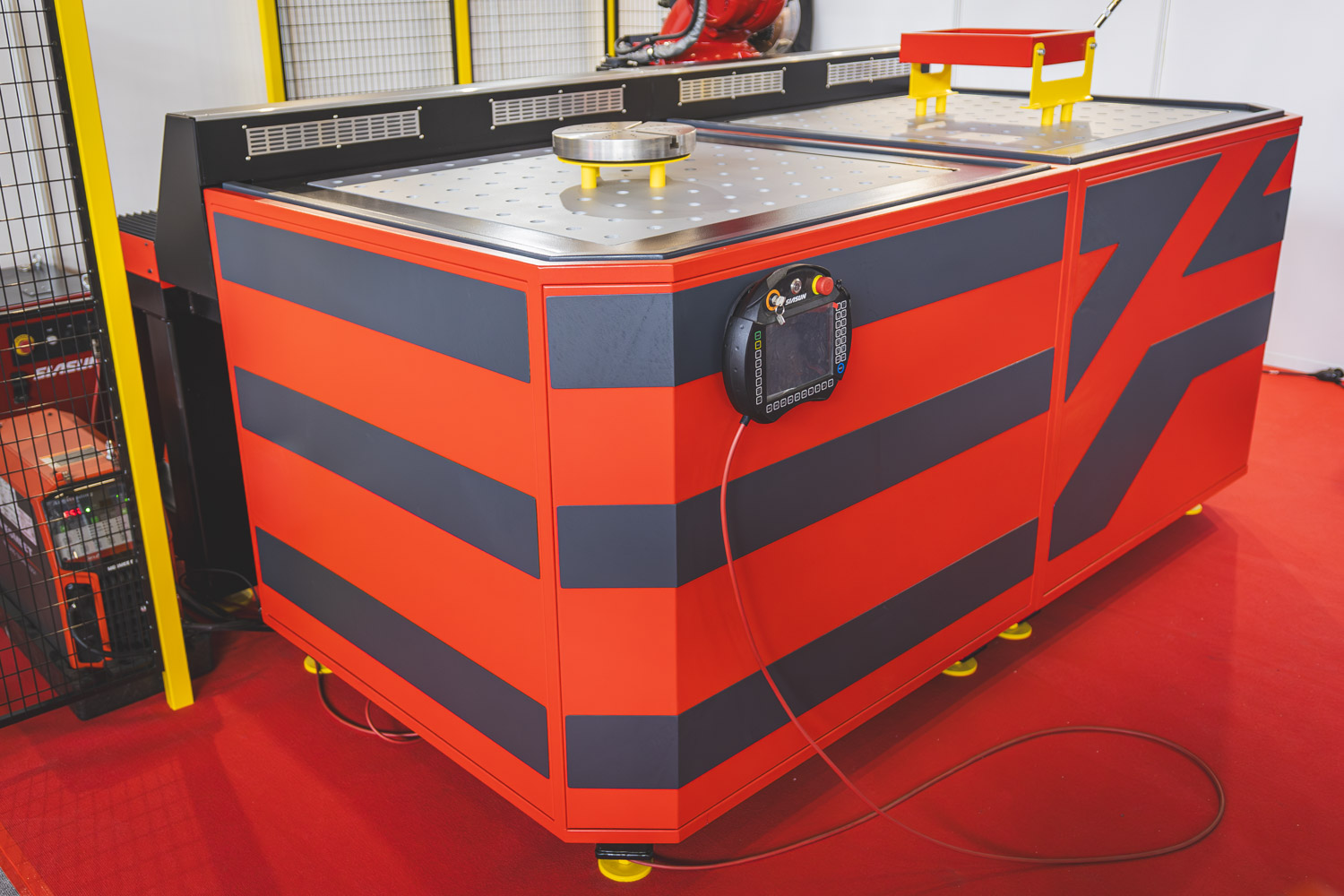
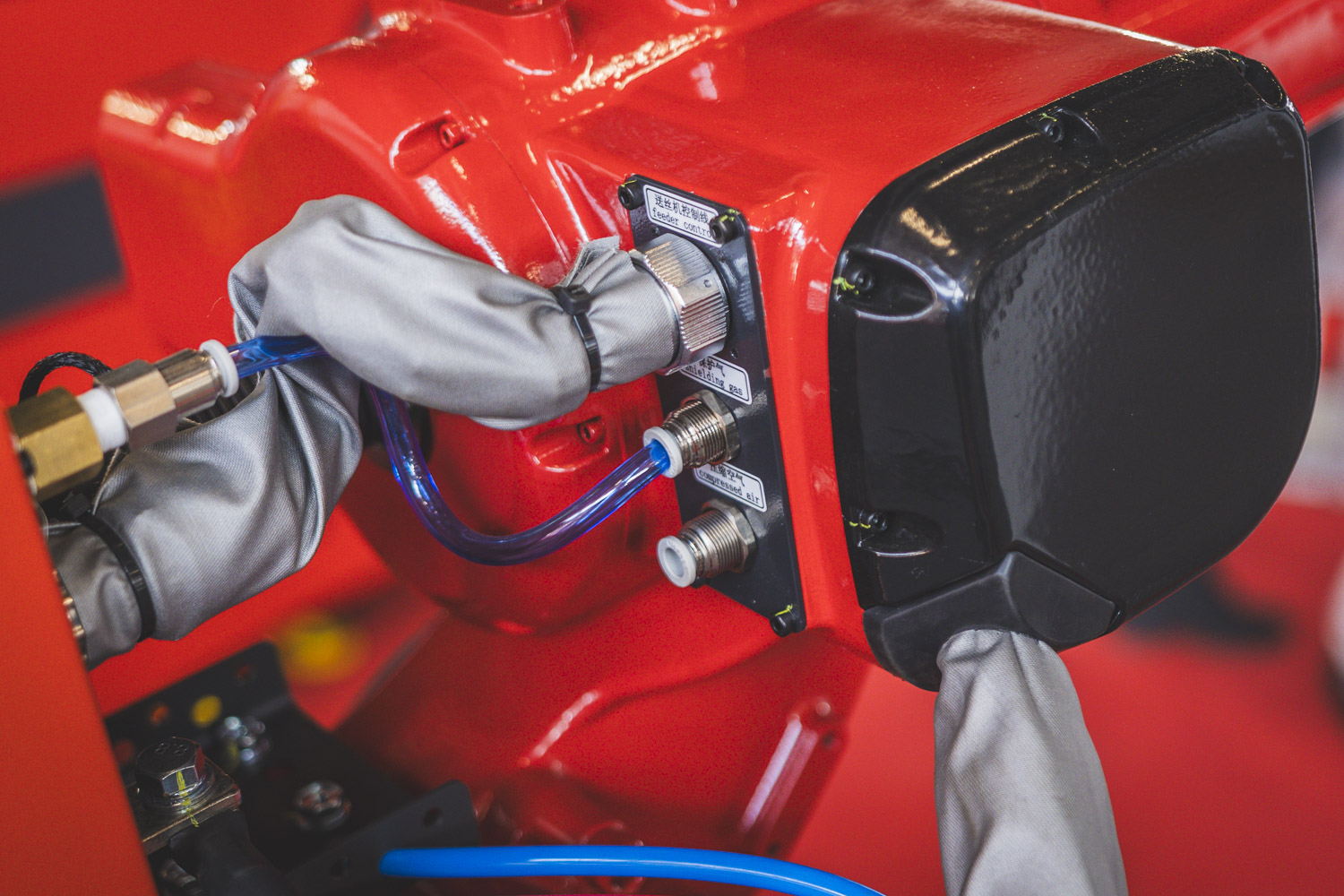
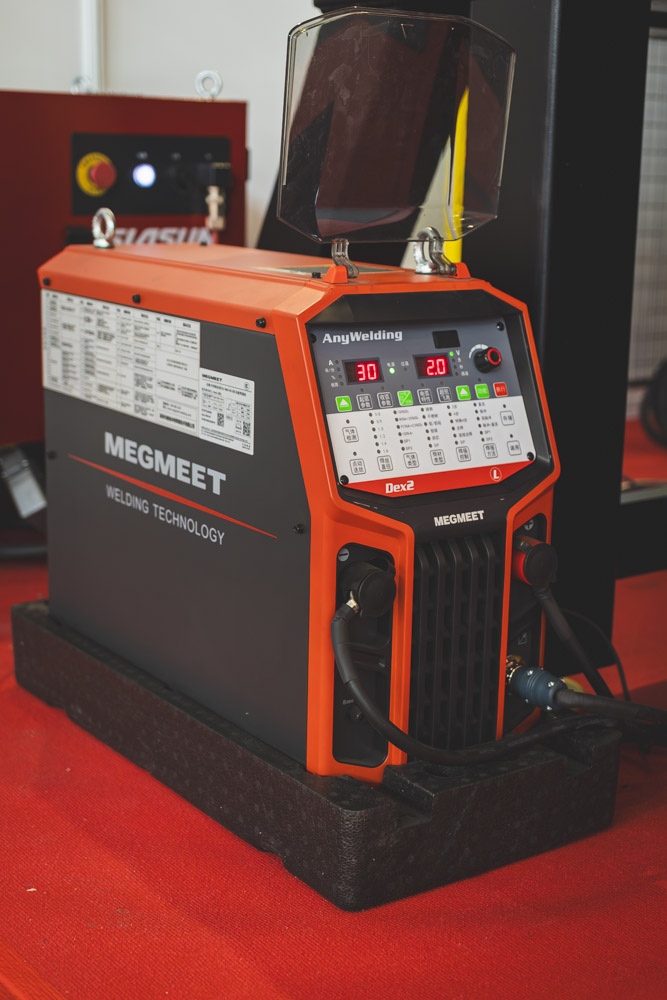
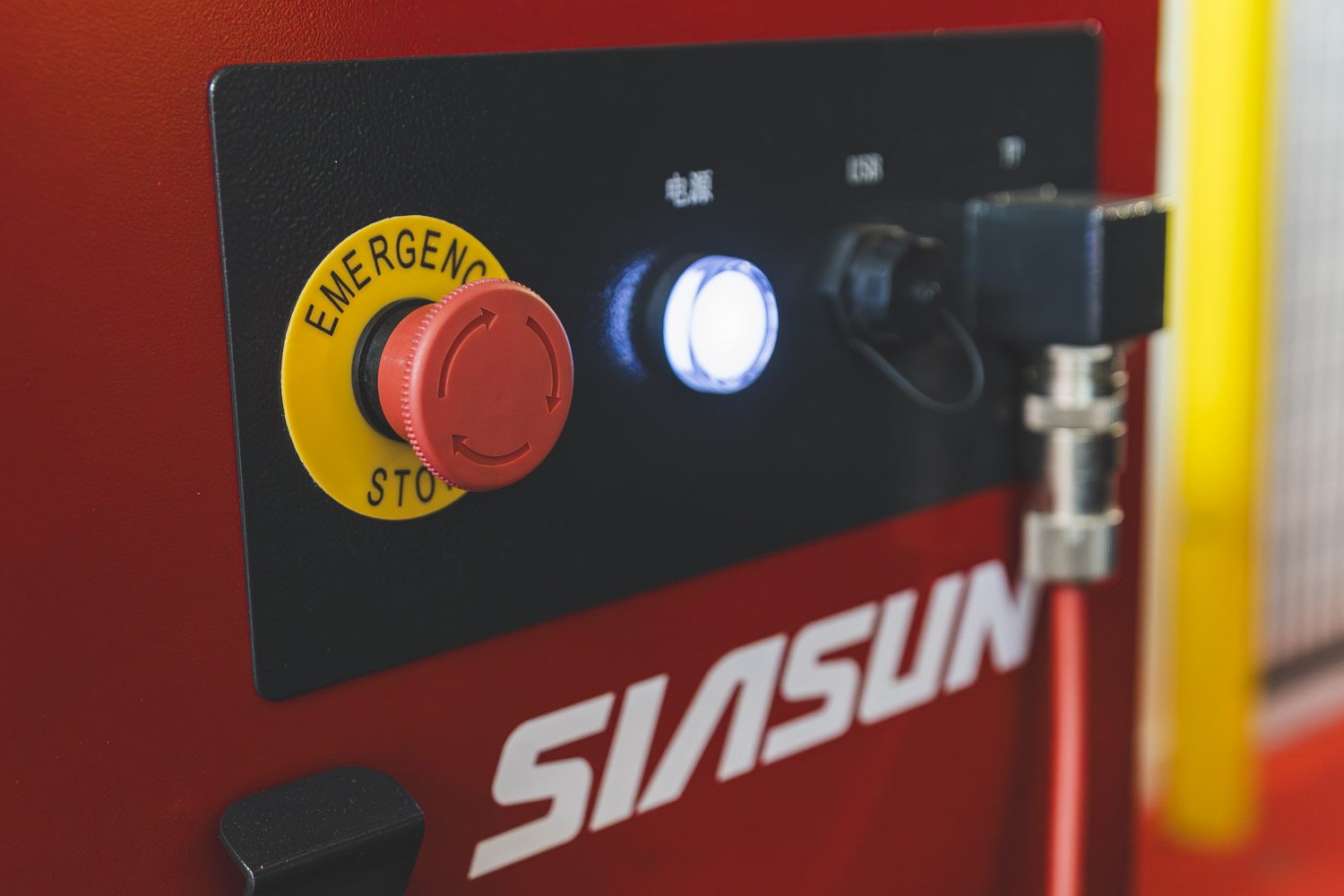
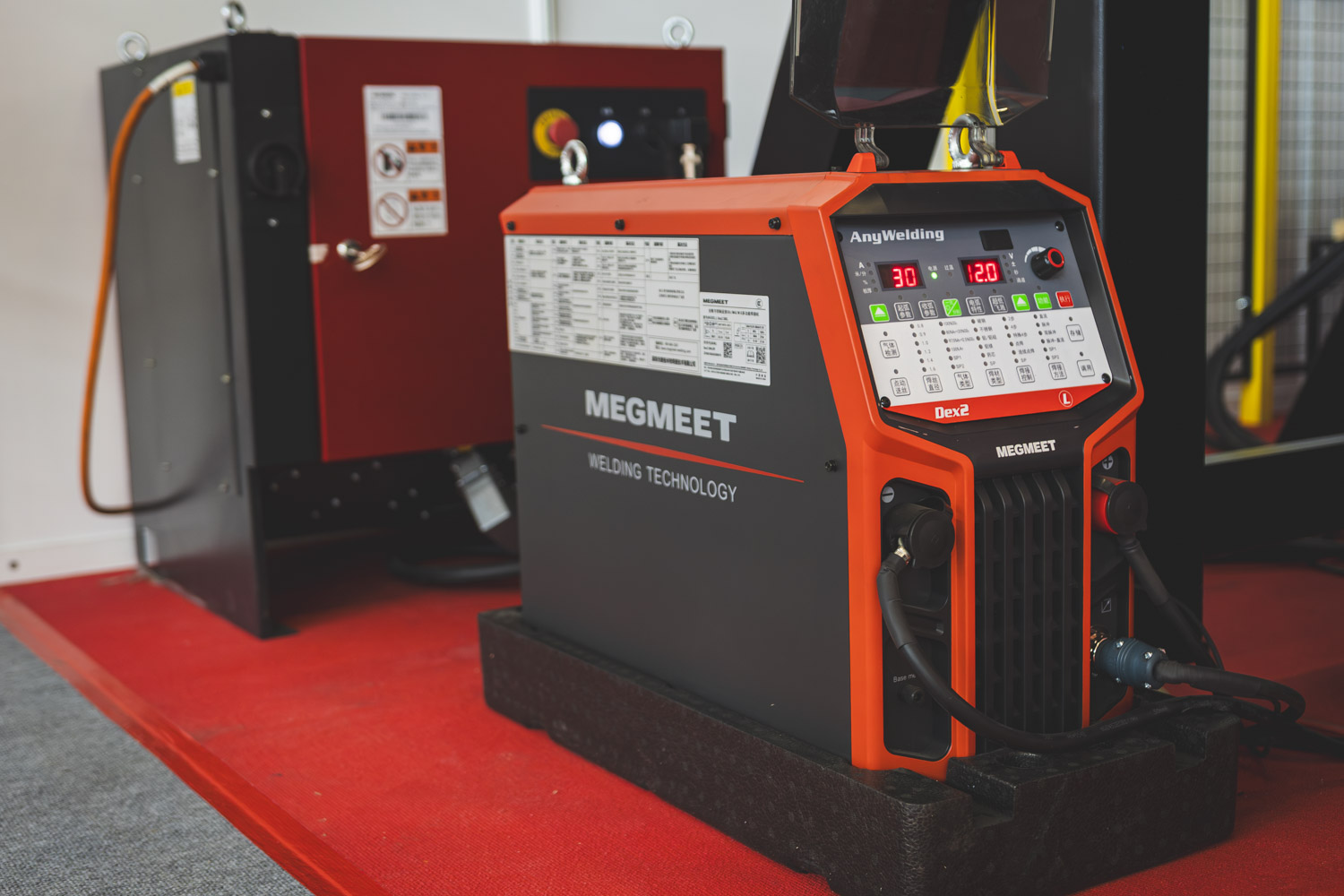
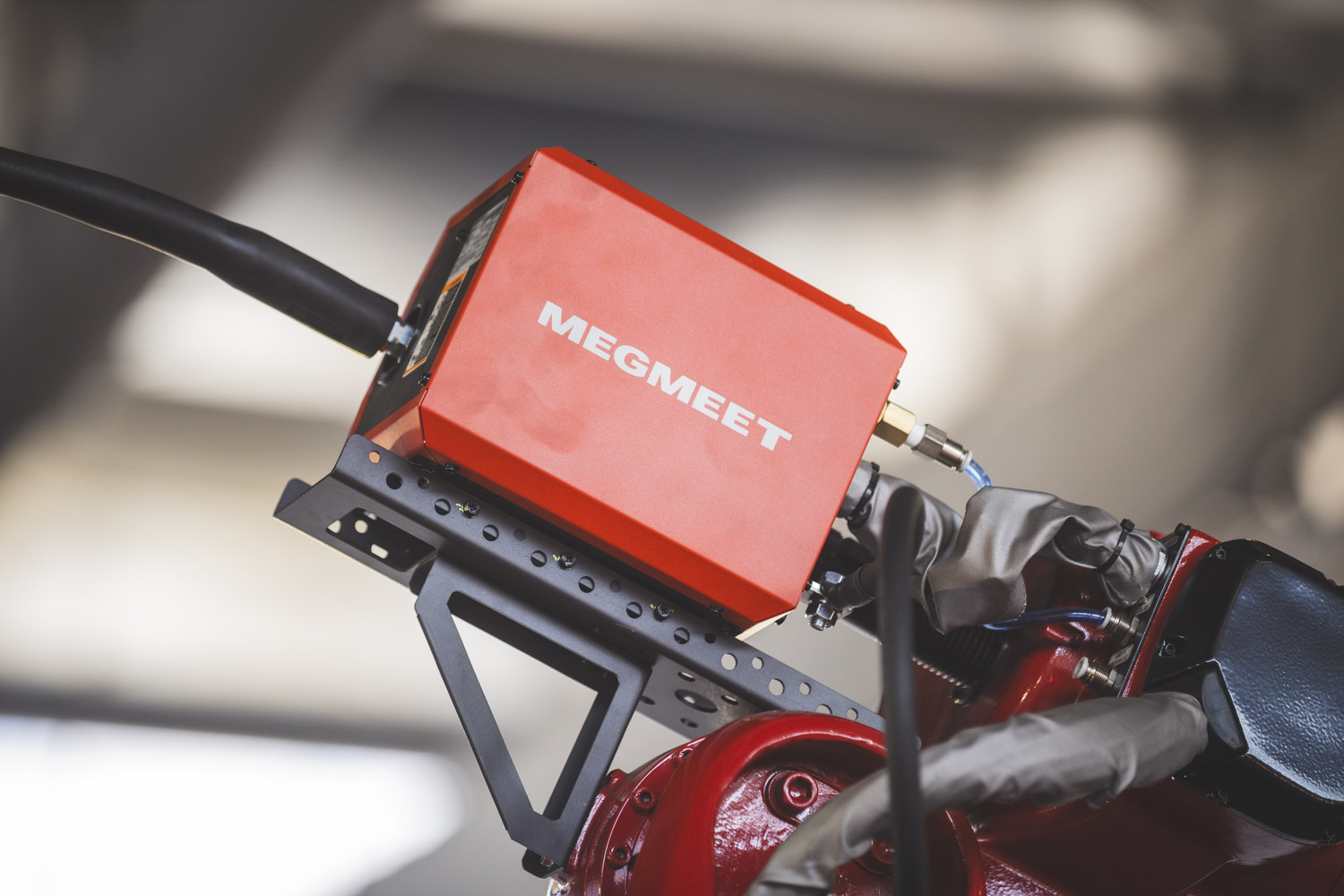
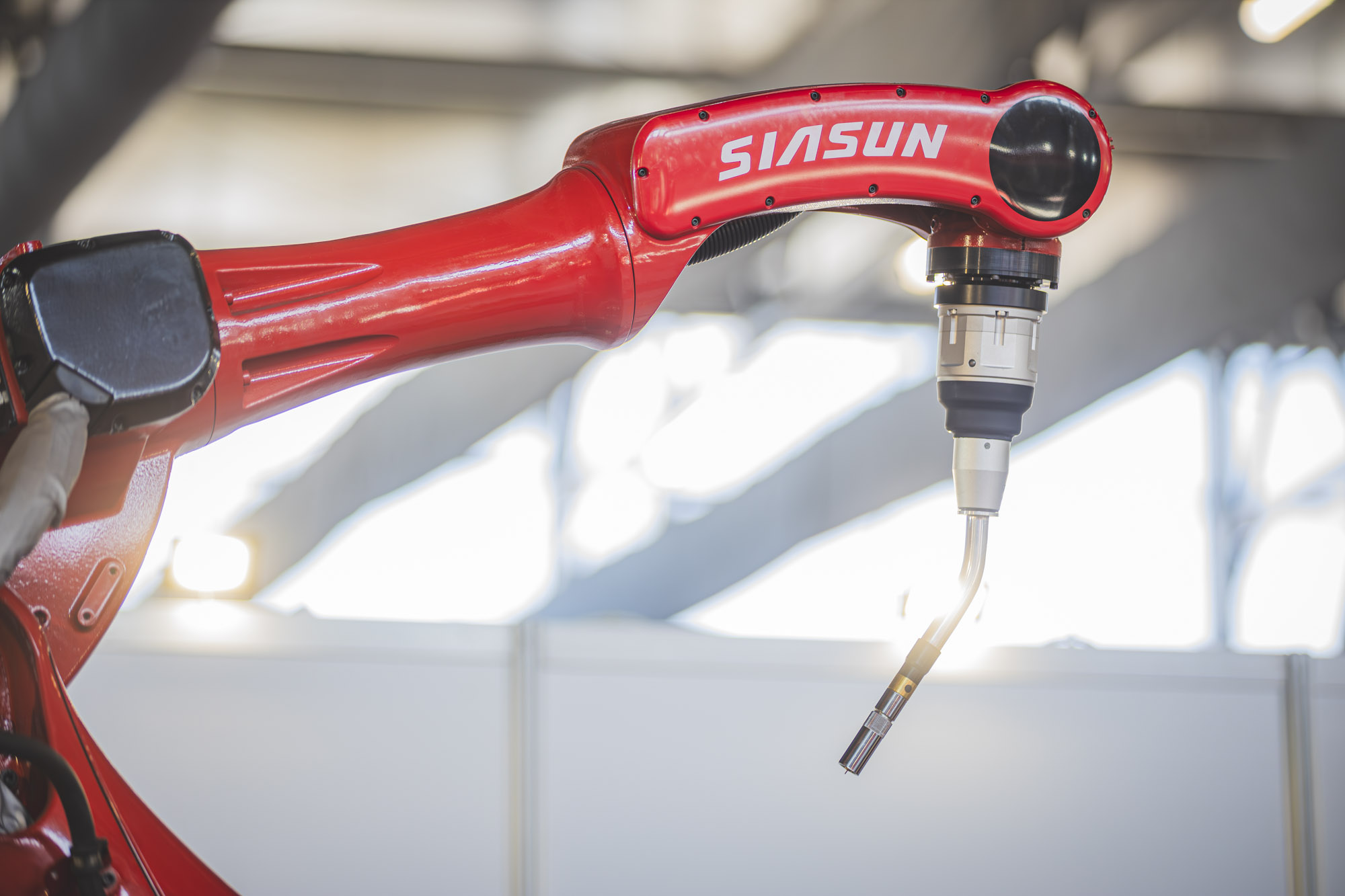
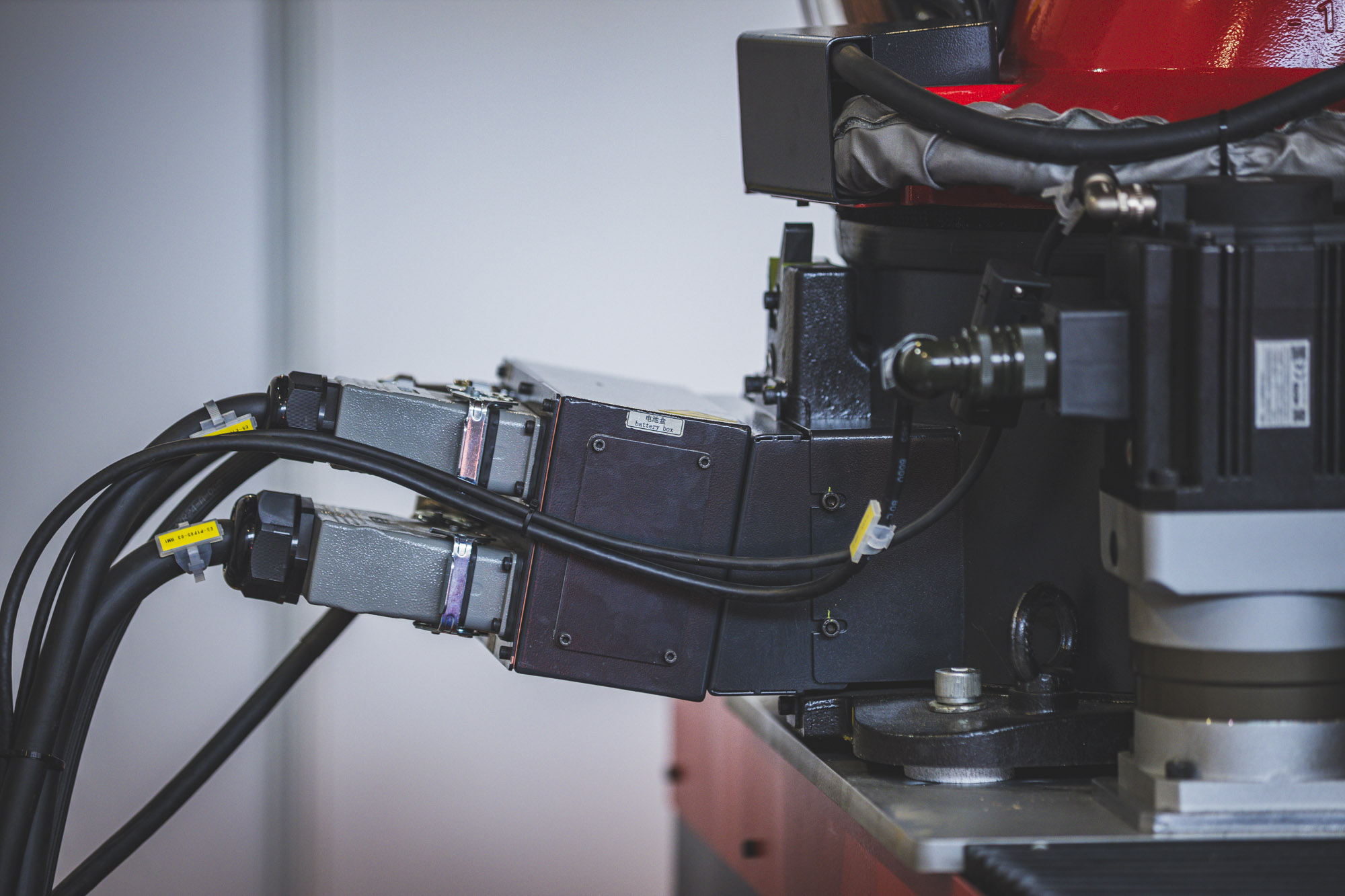

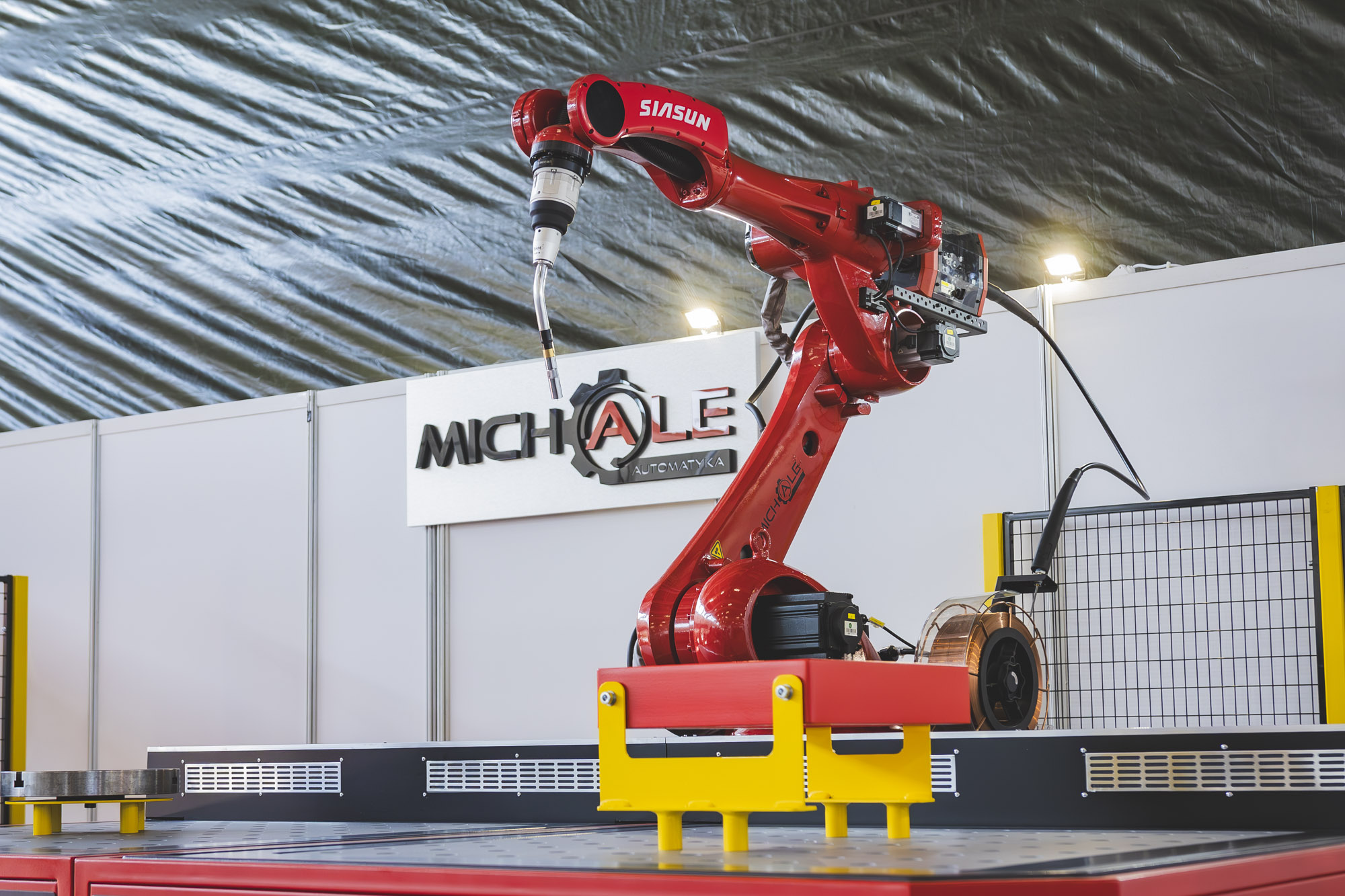
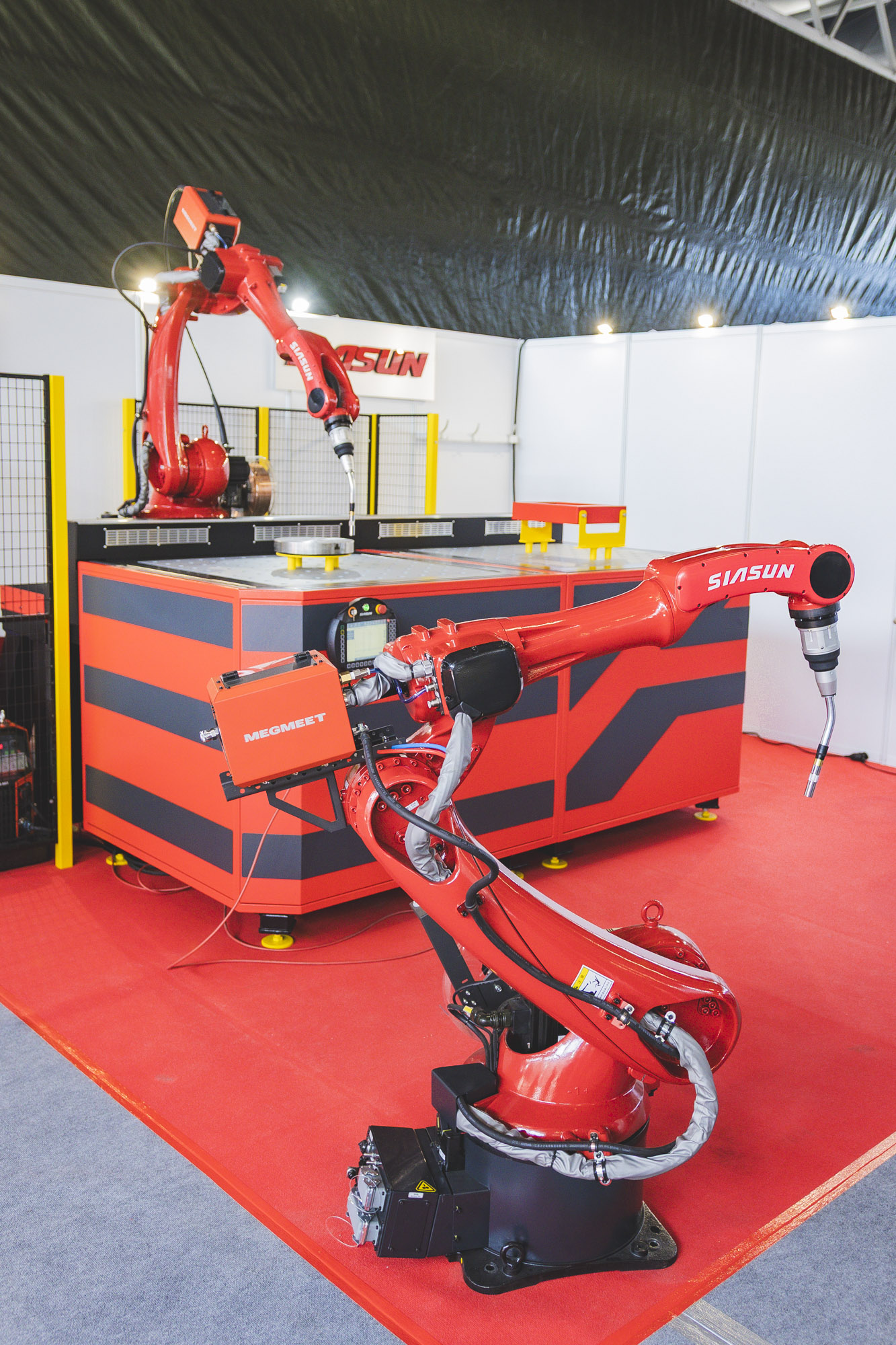
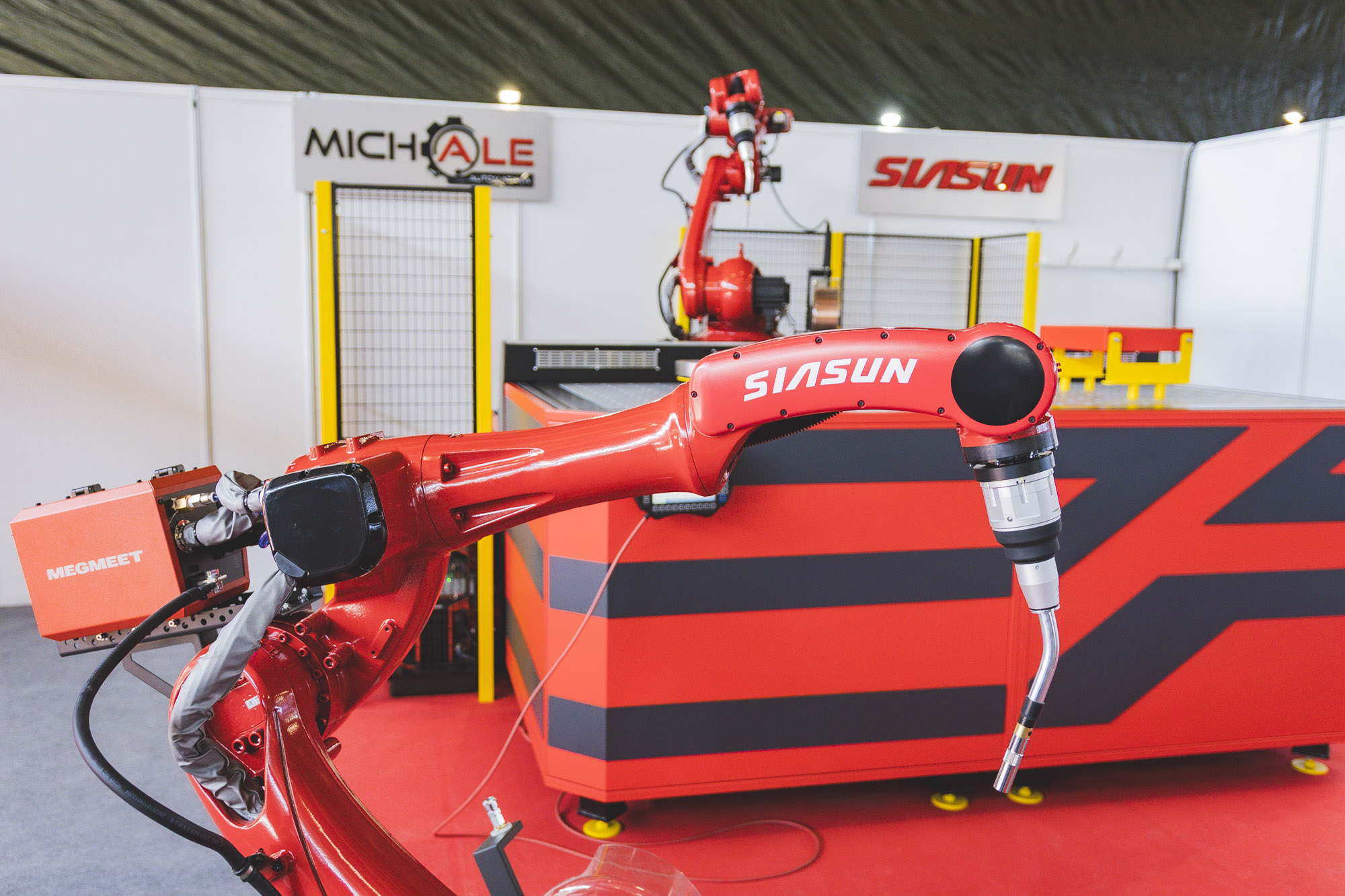
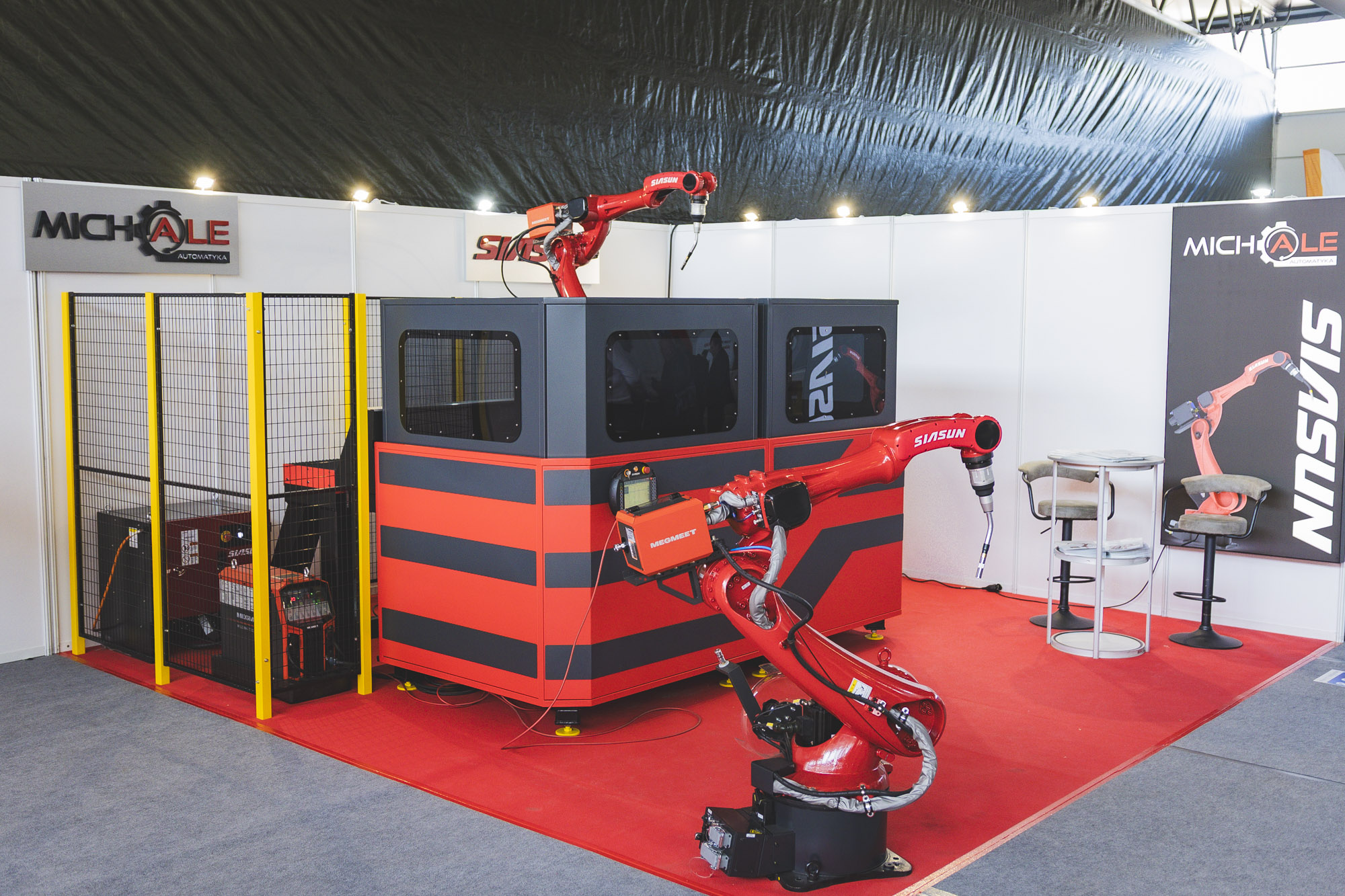
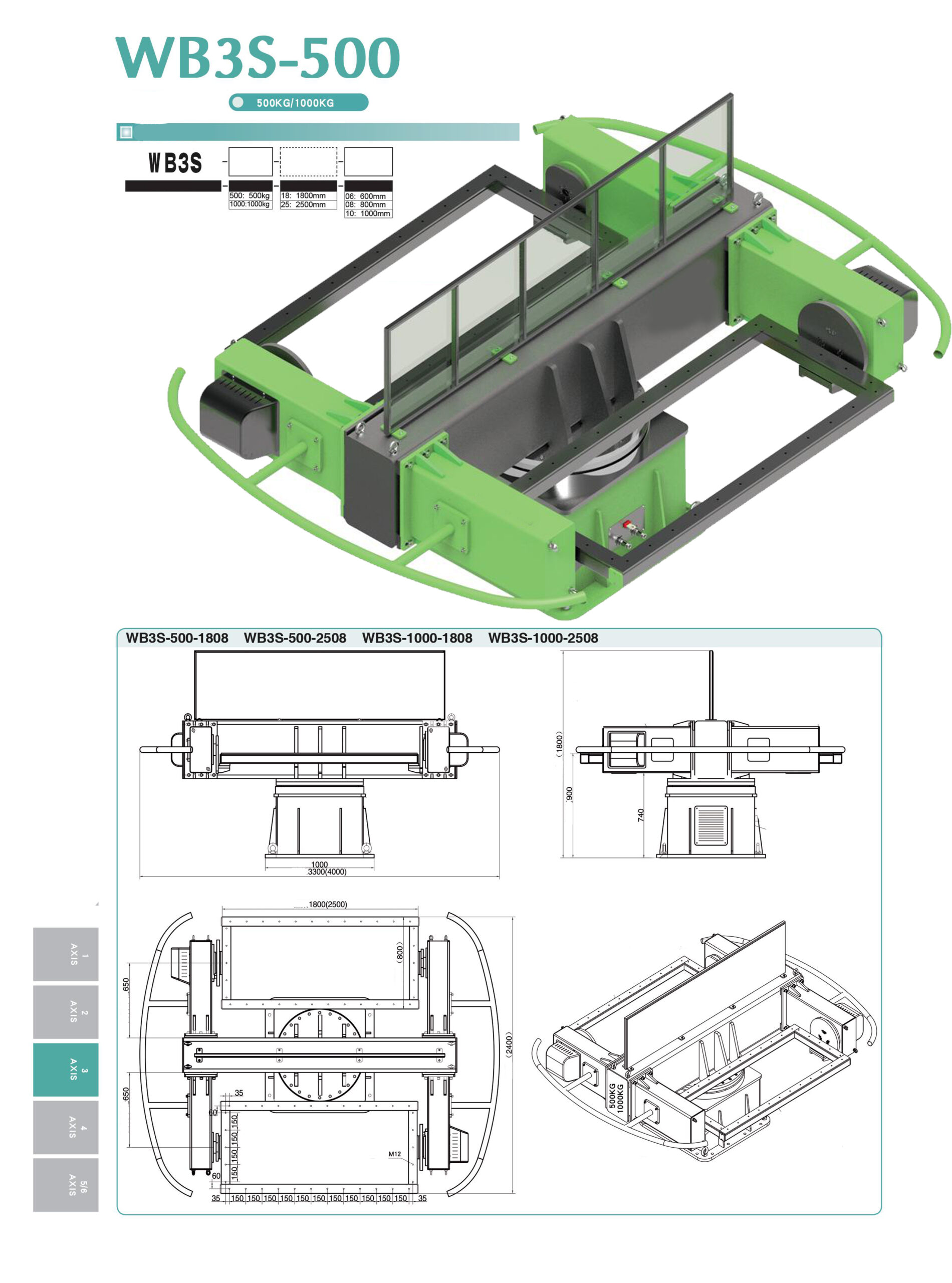
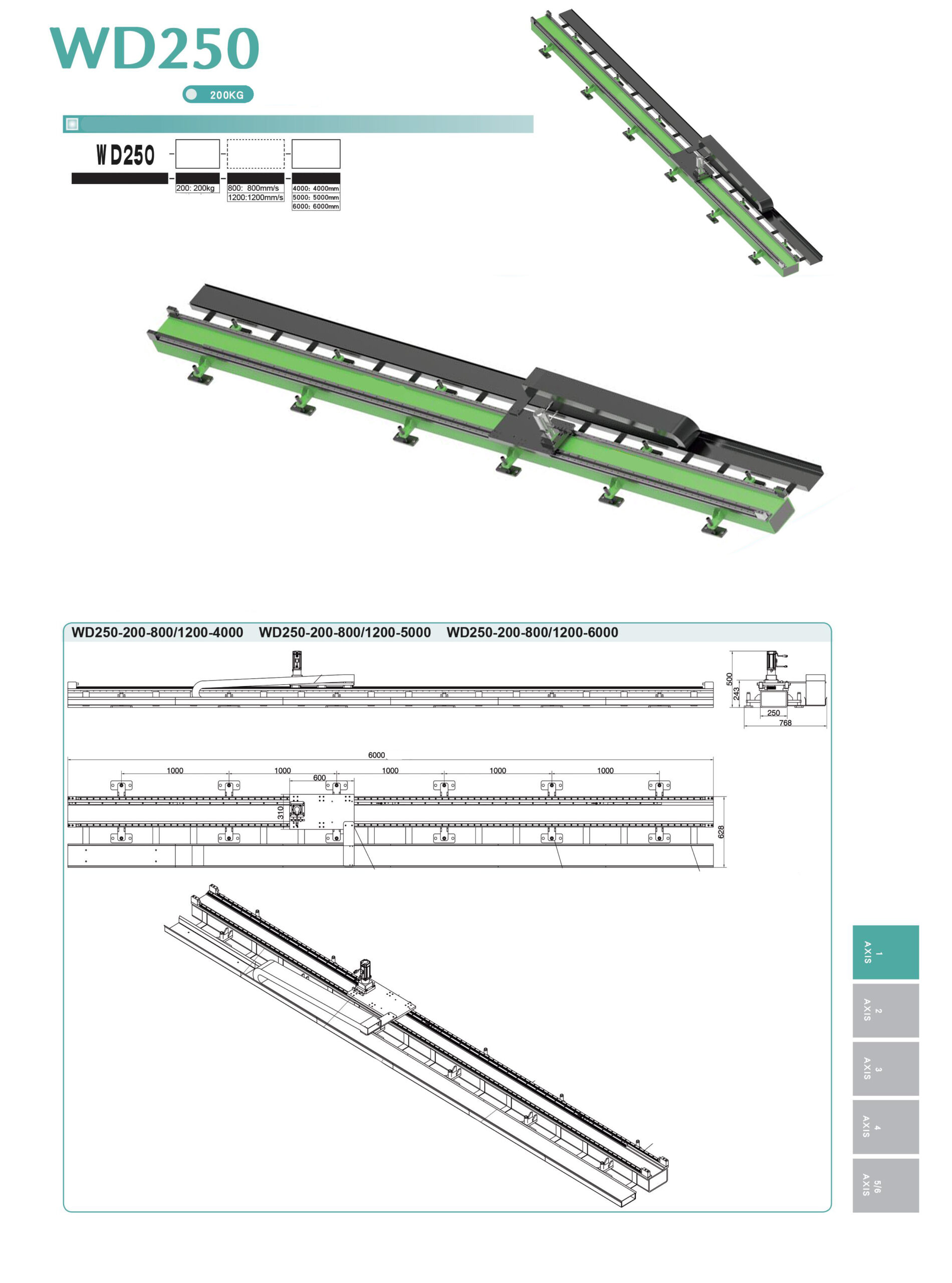

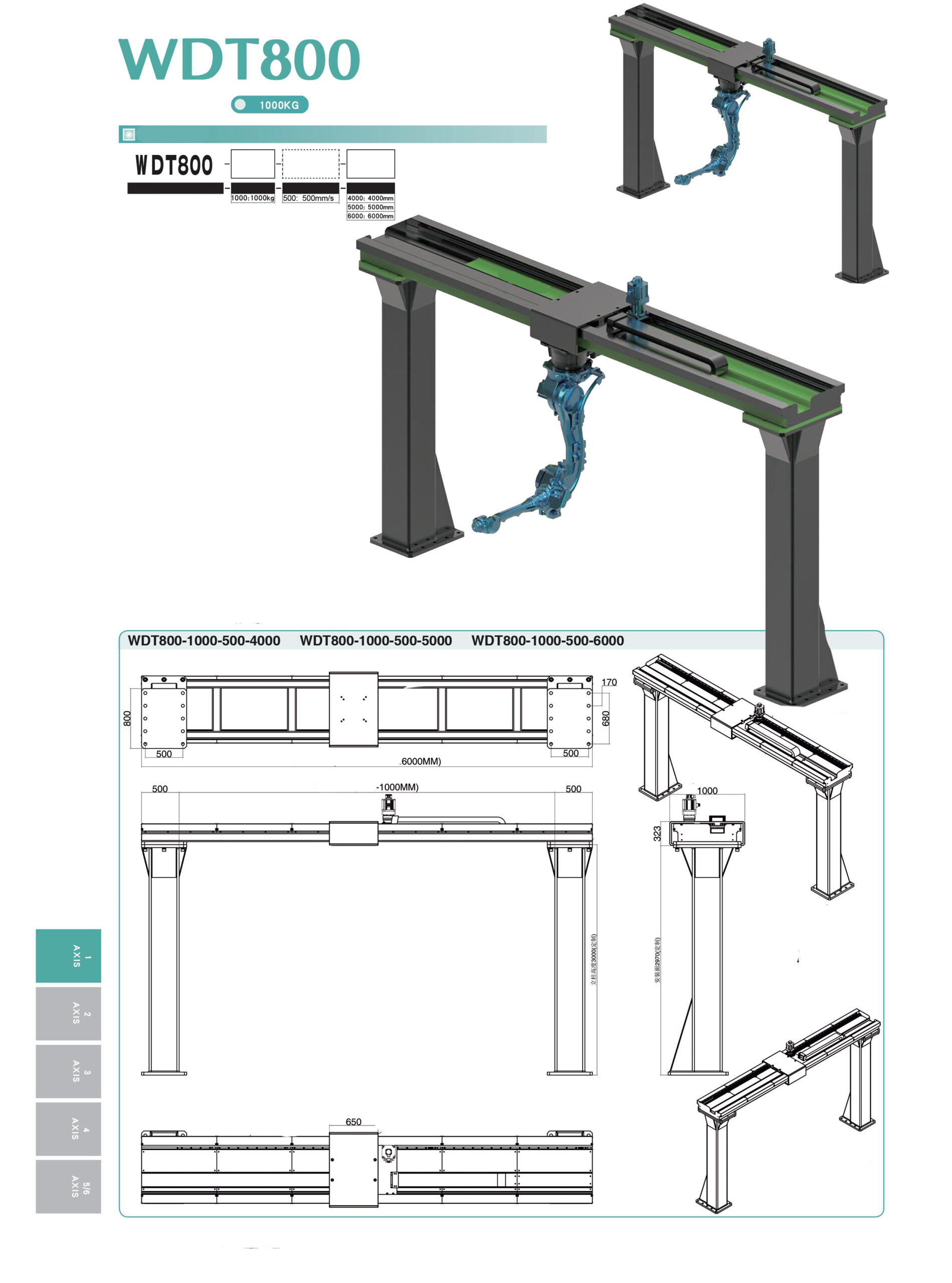
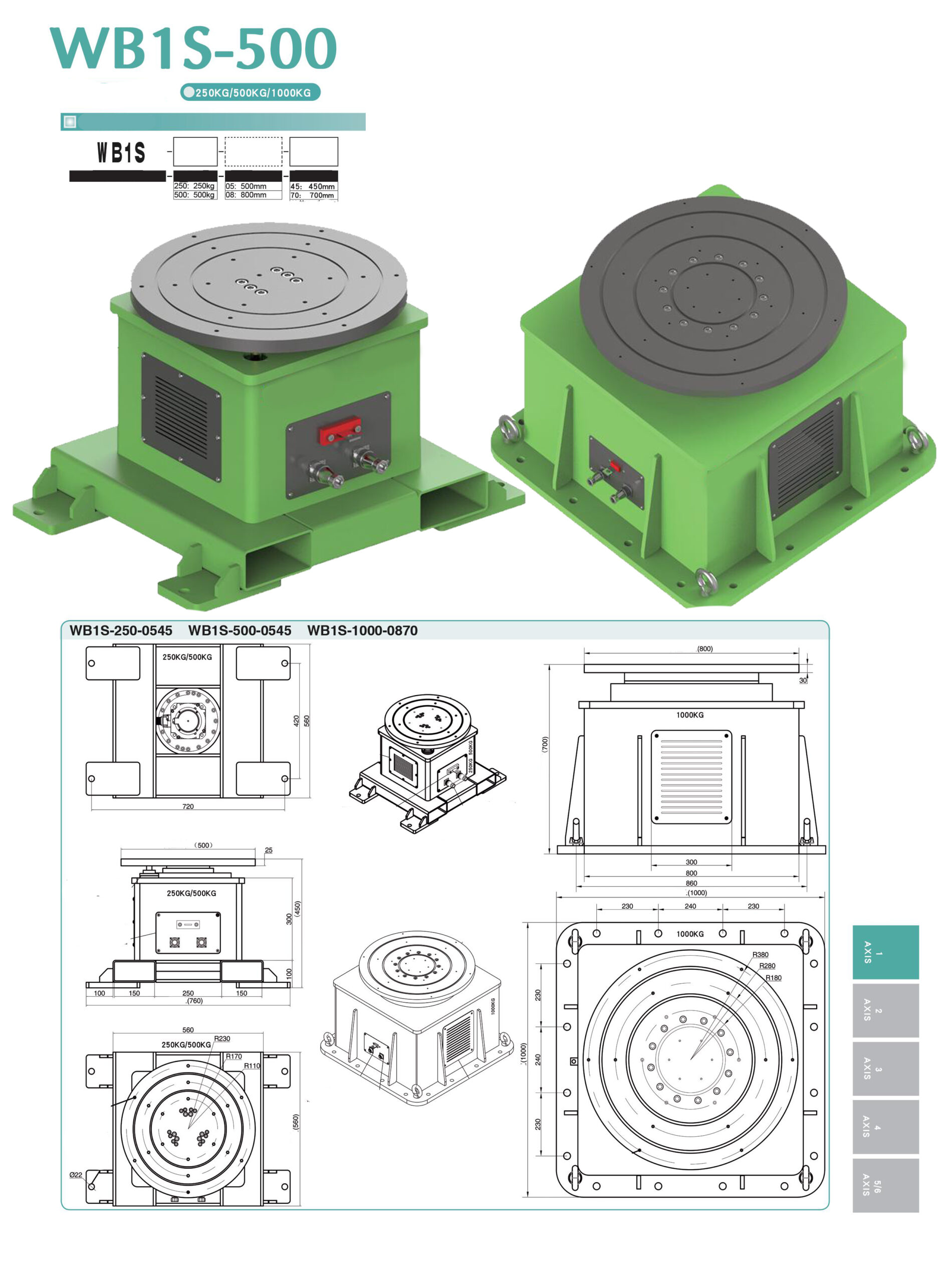
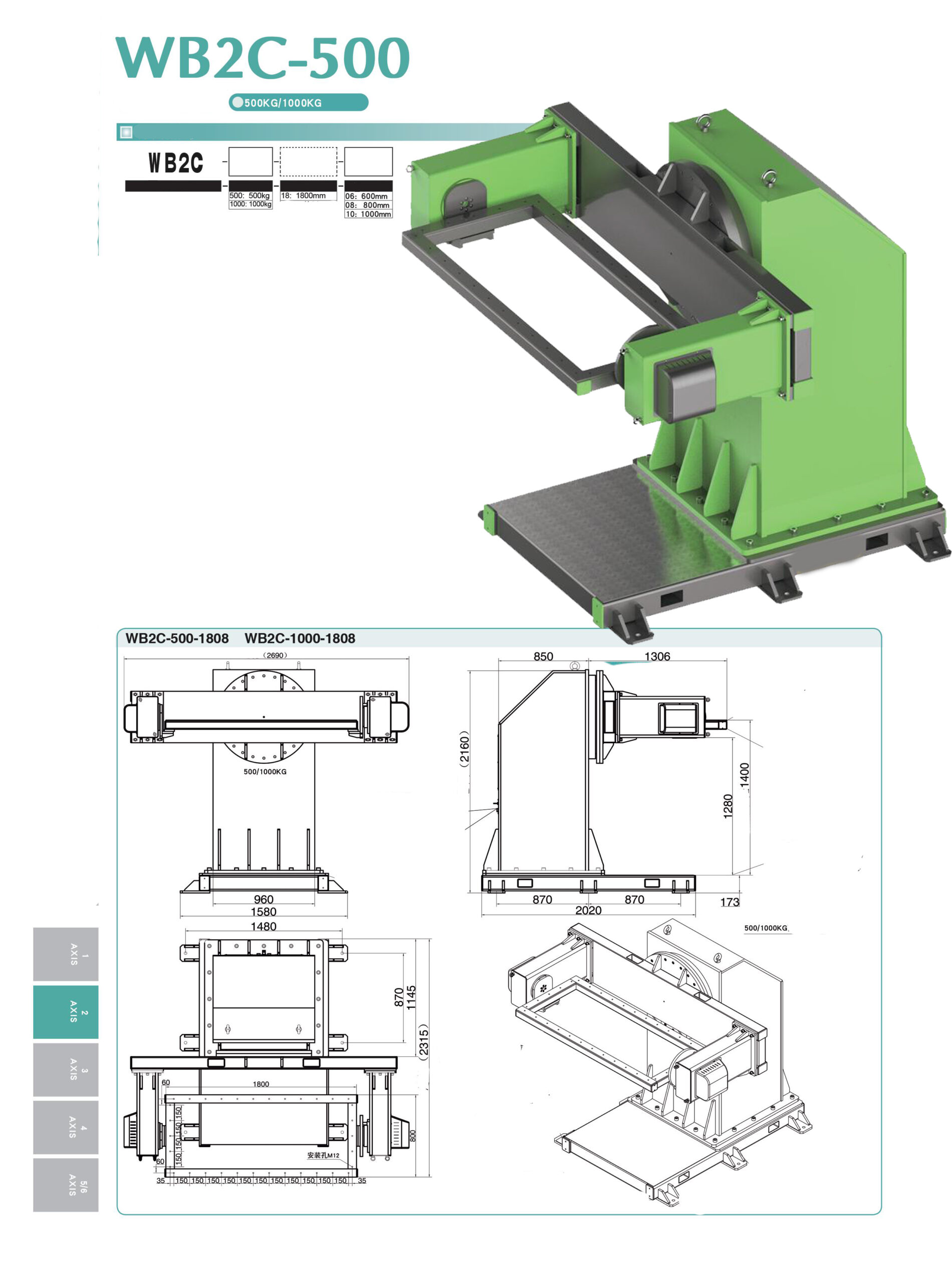
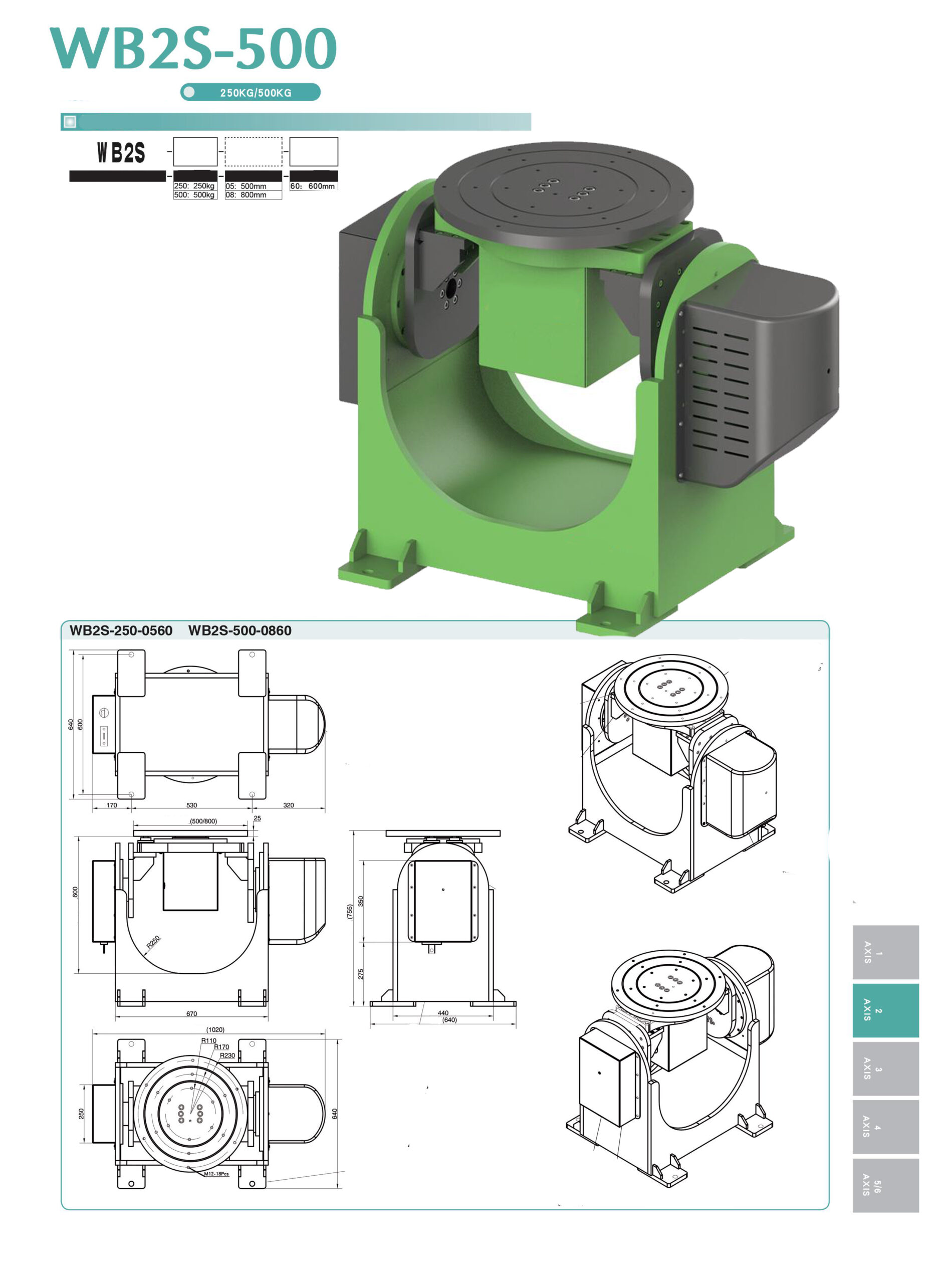
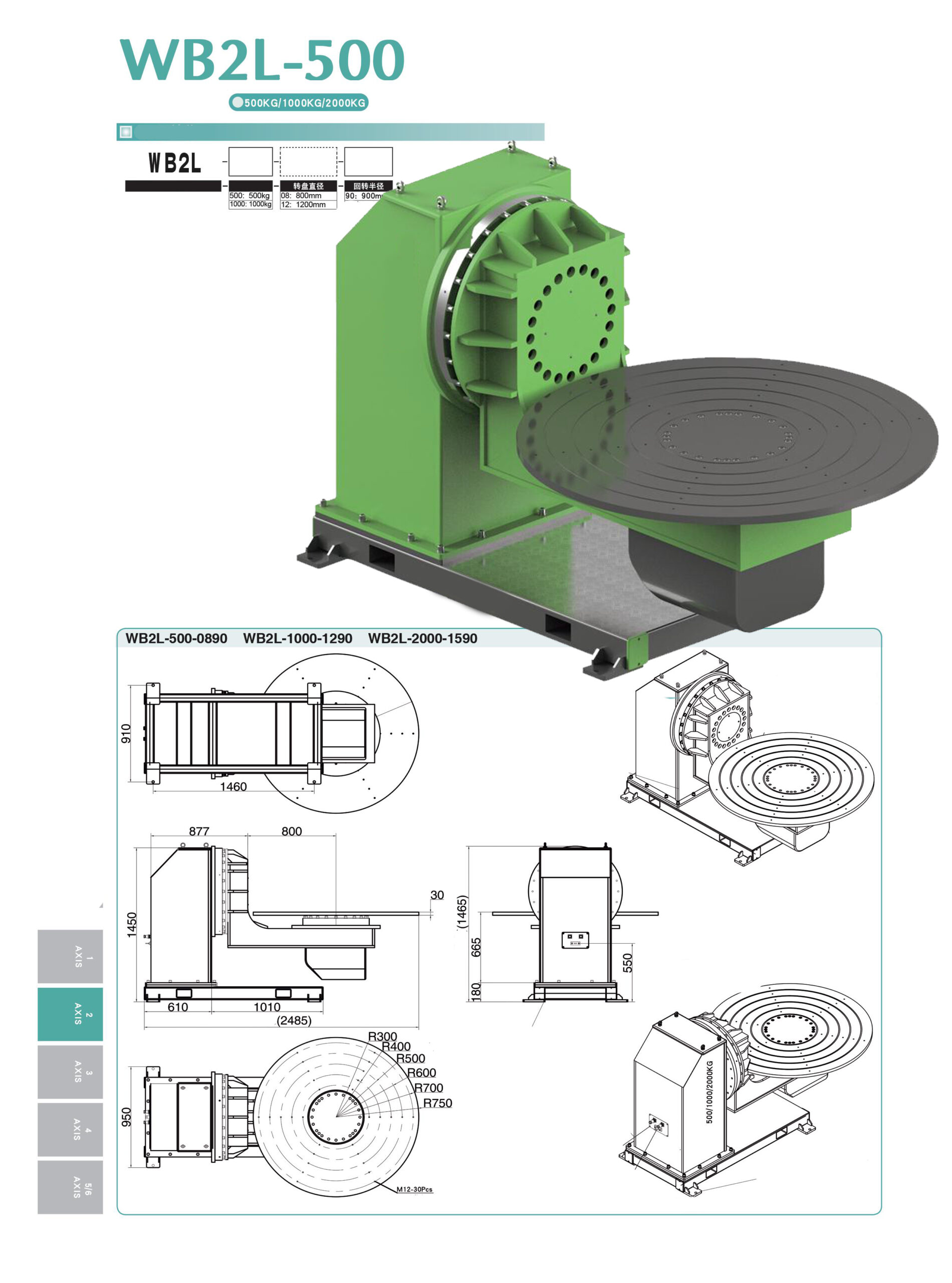
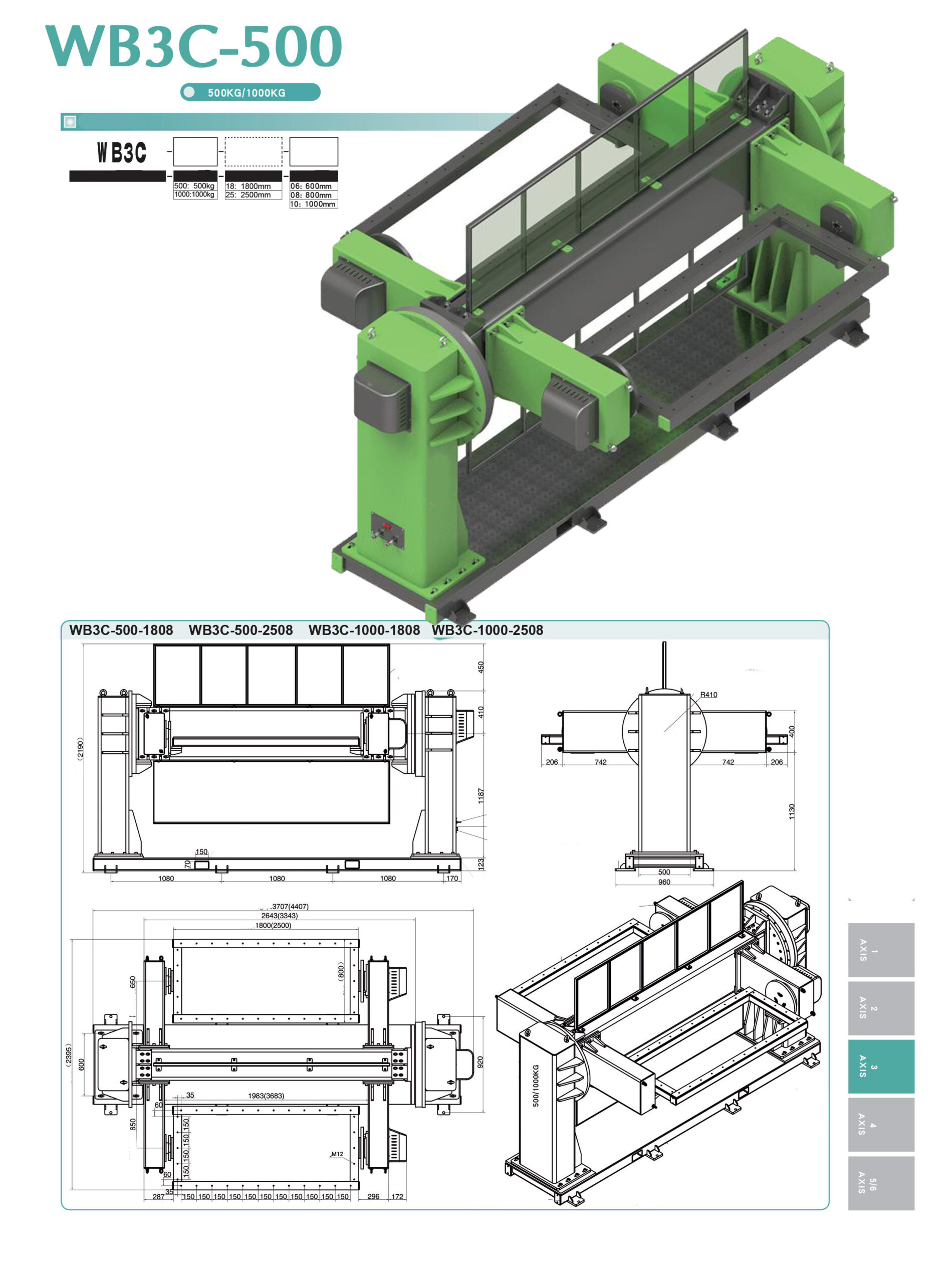
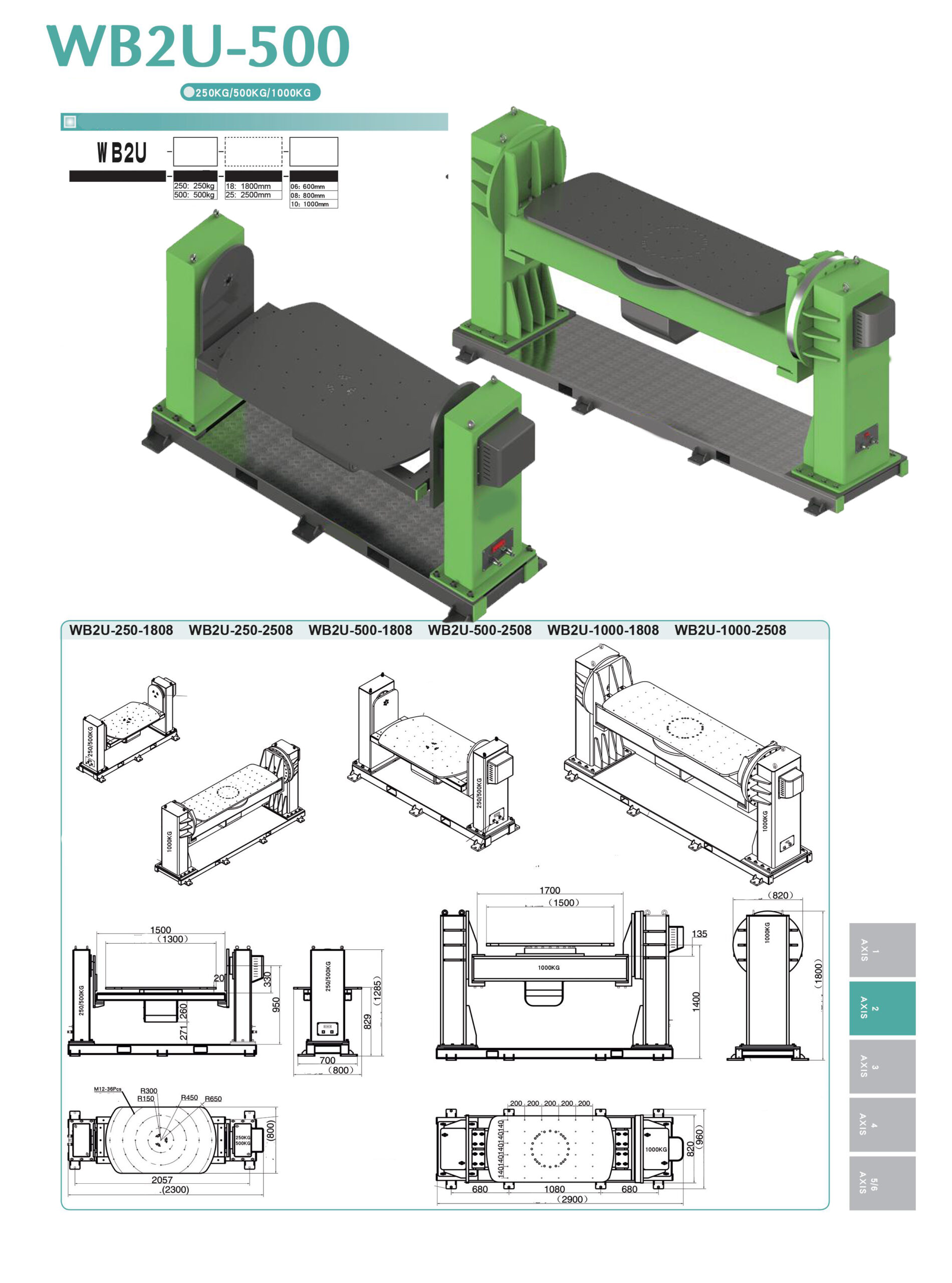
Additional equipment for robot workstations
We can equip robotic workstations with additional accessories. With the right choice of accessories, it is possible to increase the efficiency, safety and versatility of production processes.
Robotised workstations
Why us?
We are a company that offers end-to-end construction of robotic workstations from A to Z, eliminating the need for external contractors and speeding up projects. Our experience in building production lines allows us to transfer proven solutions to modern robotic workstations, ensuring high quality and efficiency.
In addition, as the exclusive distributor of Siasun robots in Poland, we offer our customers access to market-leading robotic technology at more competitive prices, without having to compromise on quality and performance.
-
Experience in building production lines Years of experience in the design and construction of production lines allow us to implement proven and innovative solutions, tailored to the specific needs of the company.
-
Individual approach to the customer We understand that every business is different, which is why our solutions are always tailored to our clients' individual needs and business goals, ensuring maximum satisfaction.
-
Competitive prices Our solutions offer excellent value for money, so you can modernise your processes without going over budget.
-
Exclusivity for Siasun robots in Poland We are the only company in Poland to offer Siasun robots that combine unparalleled quality with attractive pricing, giving our customers exceptional value and a competitive advantage.
-
Guarantee and fast service We guarantee a fast service with a fair guarantee, safeguarding your investment and ensuring the uninterrupted operation of your production facility.
-
Comprehensive service We offer full support - from consultation to design to service - ensuring seamless implementations and business continuity.
Customer feedback



Ready for collaboration?
Make an appointment consultation
Don't wait for your competitors to overtake you! Contact us today to find out how we can help your business maximise the benefits of robotisation relief. Fill out the contact form or give us a call - our team of experts is here to help!
Contact details
Michale 88C
86-134 Dragacz
Answers to frequently asked questions
FAQ
Does the robotisation allowance combine with other forms of support?
The relief cannot be applied to costs already funded by grants or other public funds, but it can be combined with other tax reliefs as long as it does not apply to the same expenditure.
What documents do I need to prepare?
Invoices, contracts, payment receipts, technical documentation of the robots, a list of eligible costs and the relevant attachments to the tax return are all necessary.
What if I don't use the full allowance in a given year?
You can settle the unused part of the relief in the following six tax years, allowing you to plan your investments and settlements flexibly.