SIASUN SR25A-12/2.01 robot - Comprehensive robotised workstations from design to service
We not only offer the SIASUN SR25A-12/2.01 robot, but also complete robotic production workstations. We carry out the entire process - from design to implementation to service - all in one company.
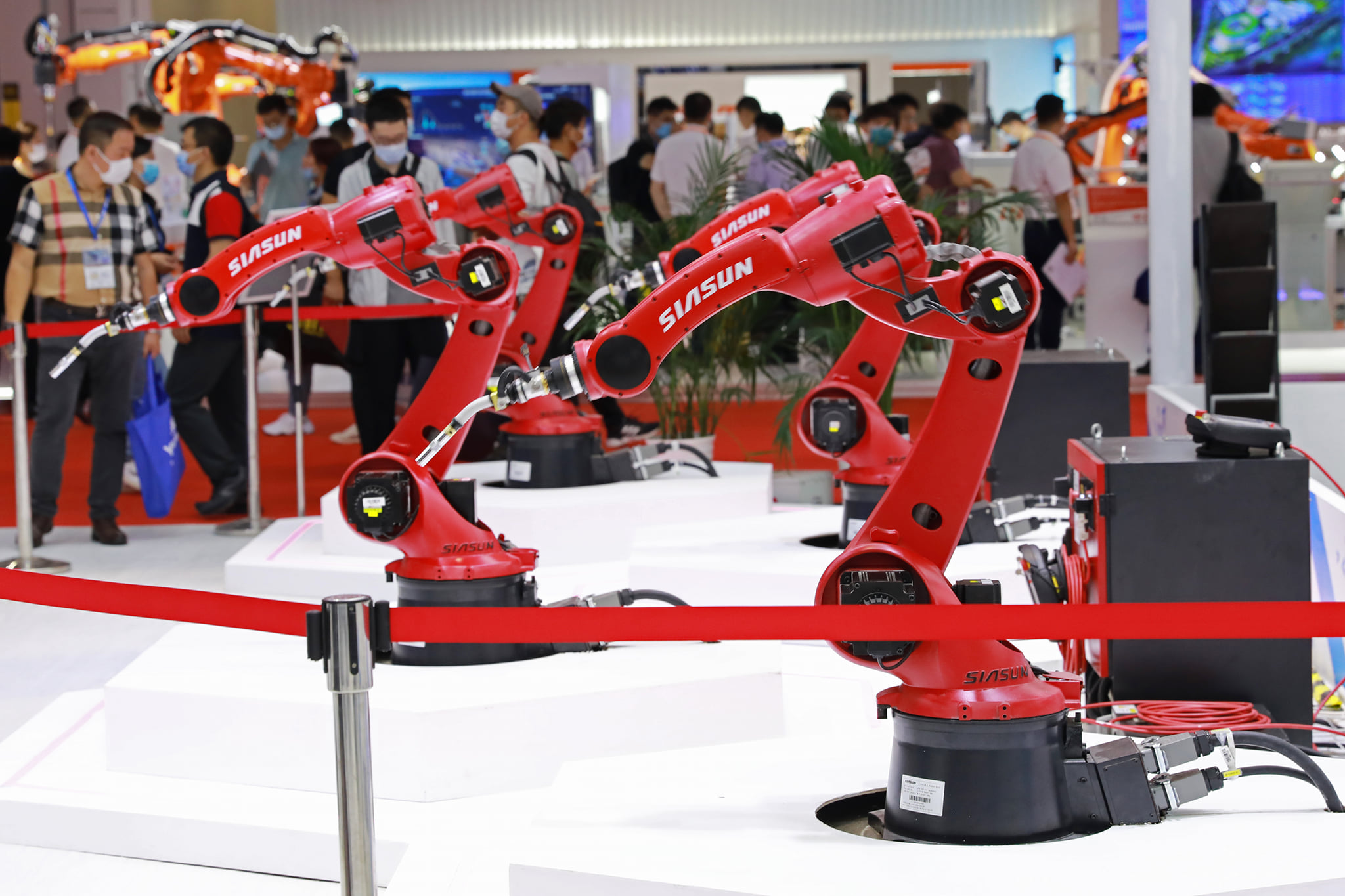
SIASUN SR25A-12/2.01
The SIASUN SR25A-12/2.01 robot is a high-tech solution that stands out for its modern design and versatile application possibilities. Its streamlined, hollow arc arm is designed for maximum functionality. This design significantly reduces interference with workpieces, resulting in greater operational flexibility and the ability to create more compact working arrangements. This makes the robot ideal for environments where space is limited.
The built-in welding cable system is another asset of this model. It protects the cables from external wear and tear, which not only increases the durability of the machine, but also ensures stable wire feeding. The result is higher precision and reliability for a variety of welding tasks. The robot supports multiple installation modes, making it ideal for industries such as heavy industry, shipbuilding, automotive and rail vehicle manufacturing. Its versatility allows it to be used effectively in a wide range of industrial applications.
A lightweight, highly rigid design combined with a robust drive train gives the SR25A-12/2.01 robot exceptional performance. The unit achieves a double leap in speed and precision, resulting in faster and more accurate tasks. The balanced configuration and excellent price/performance ratio make the robot a worthwhile investment for companies looking for reliable technology solutions.
With its operational stability and advanced features, the SIASUN SR25A-12/2.01 robot meets the expectations of the most demanding users, while increasing the efficiency of production processes and reducing operating costs. This is a machine built for the future of industry!
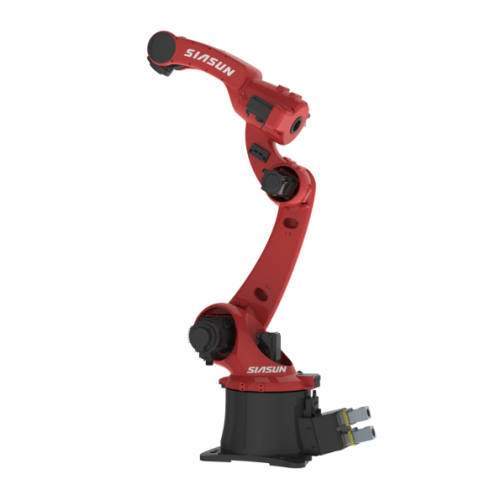
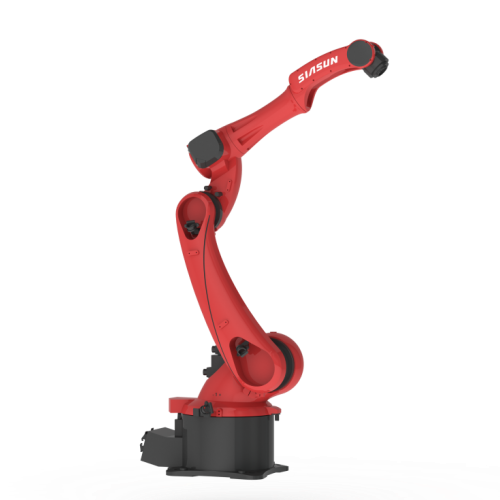
Specification
Cargo |
12kg |
Coverage |
2010mm |
Repeatability |
±0.07mm |
DOF |
6 |
Protection |
IP65 |
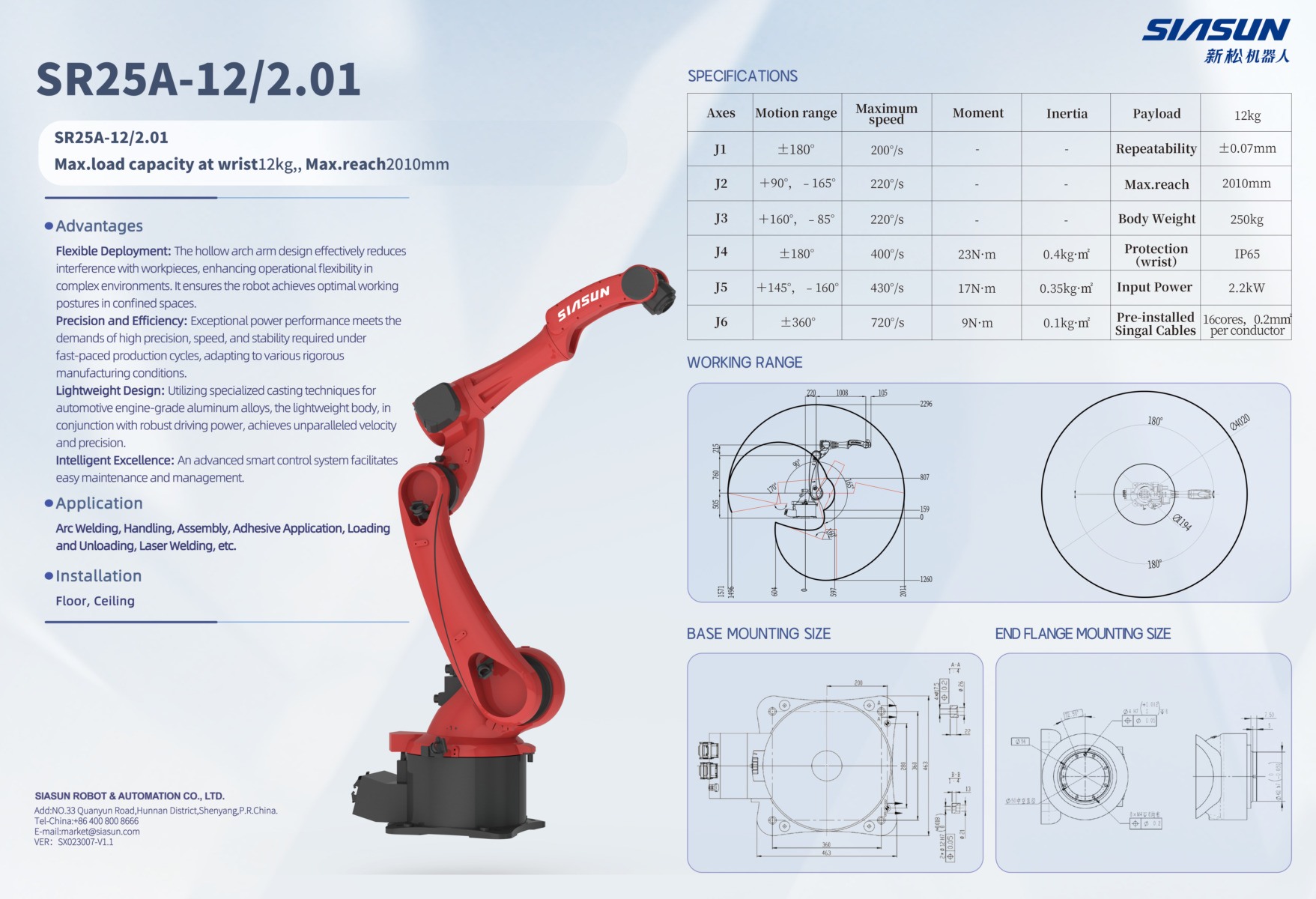
The price of the robot |
95,000 PLN net |
The price of a megmeet source robot |
from PLN 125,000 net |
Price of stand from photos below |
from 280,000 PLN net |
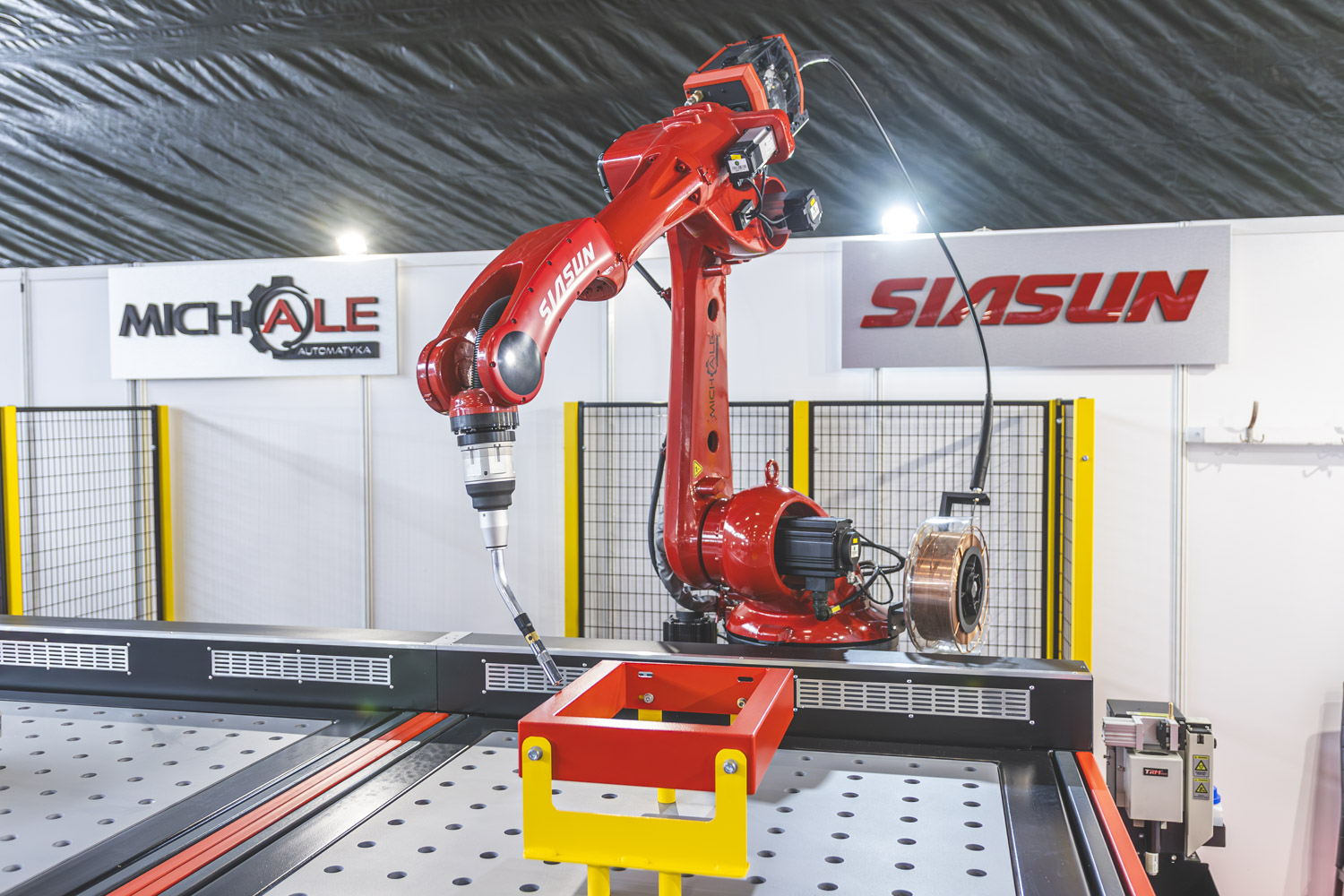

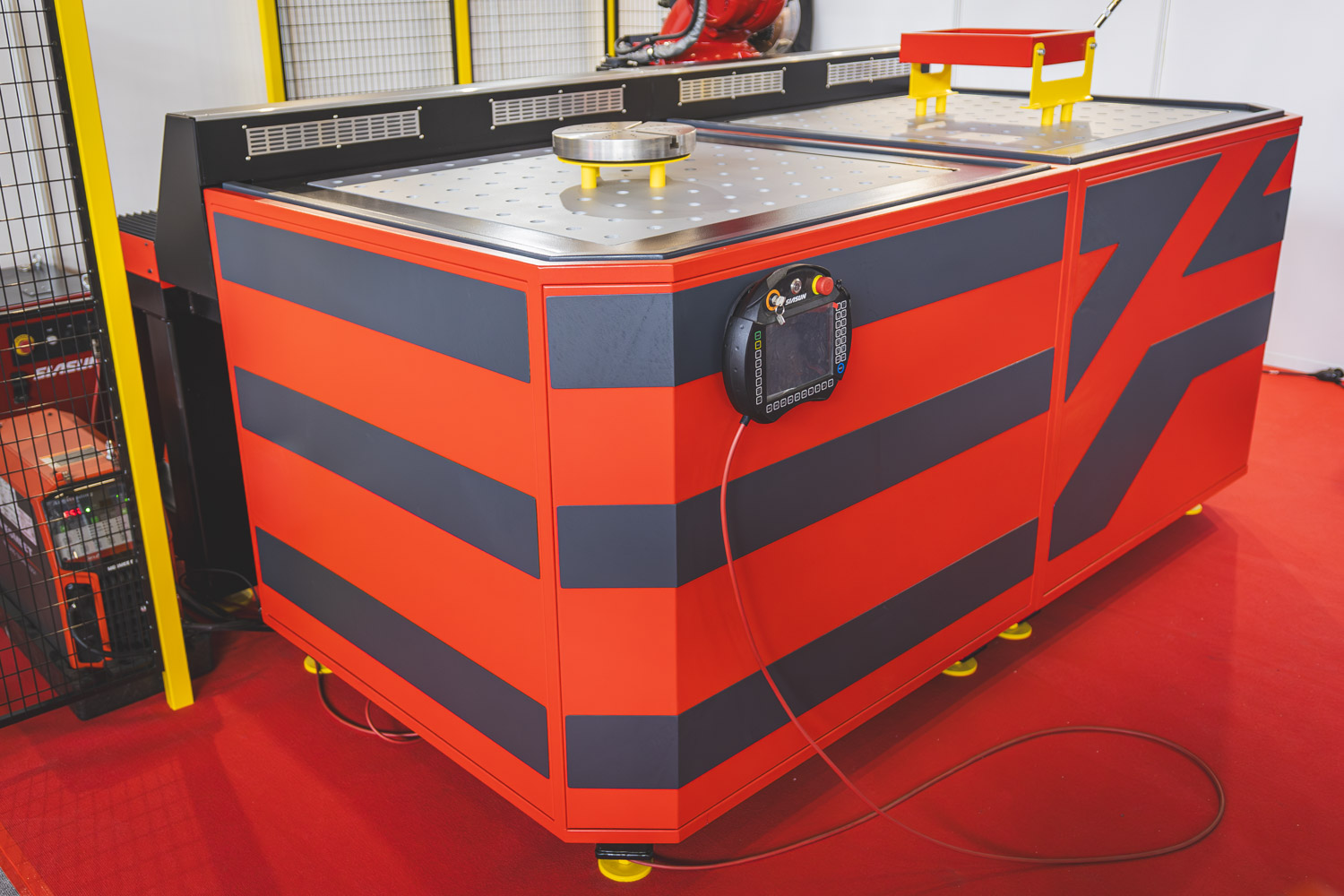
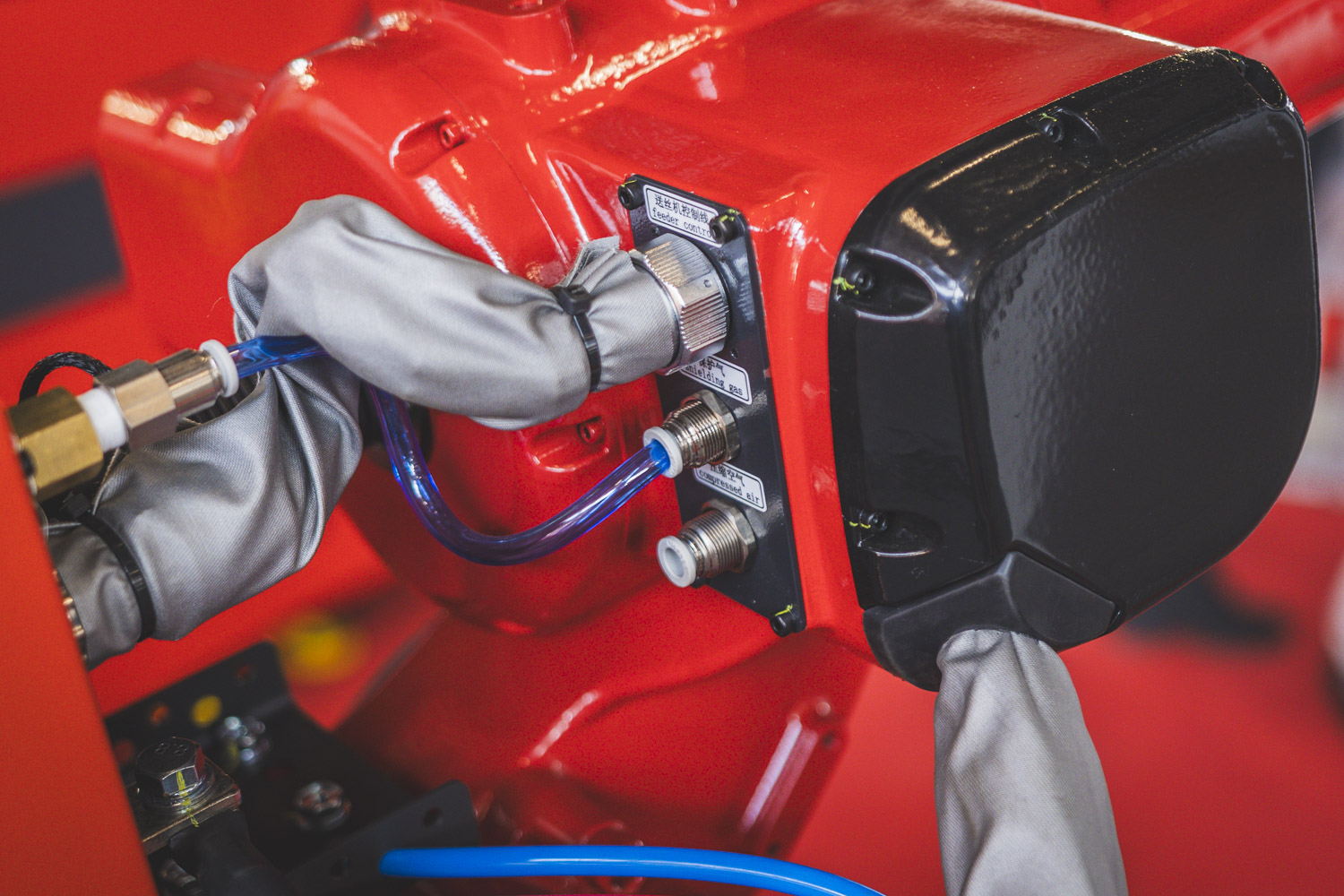
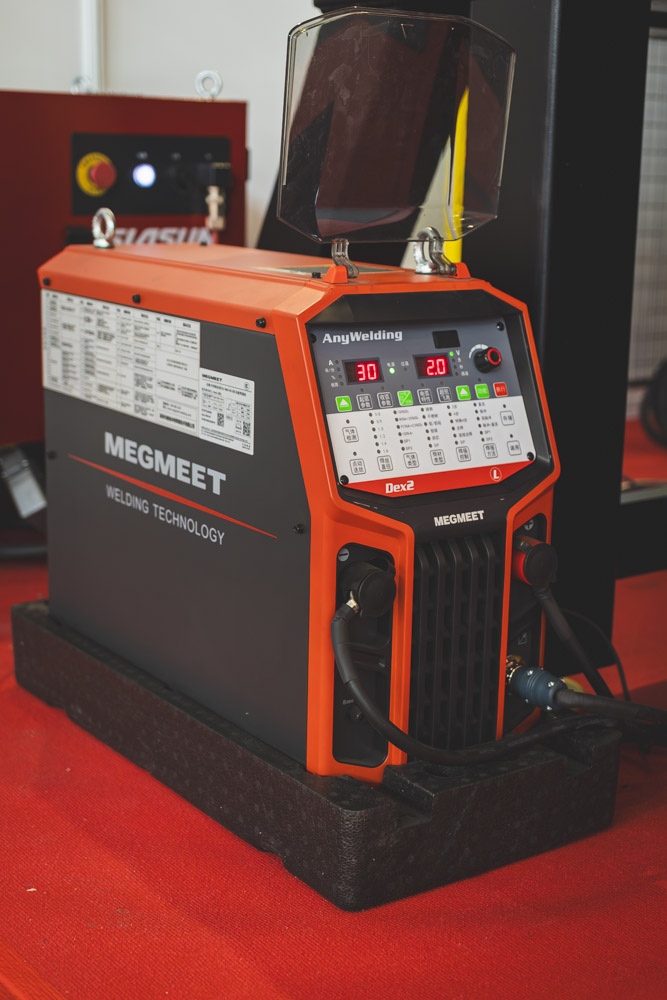
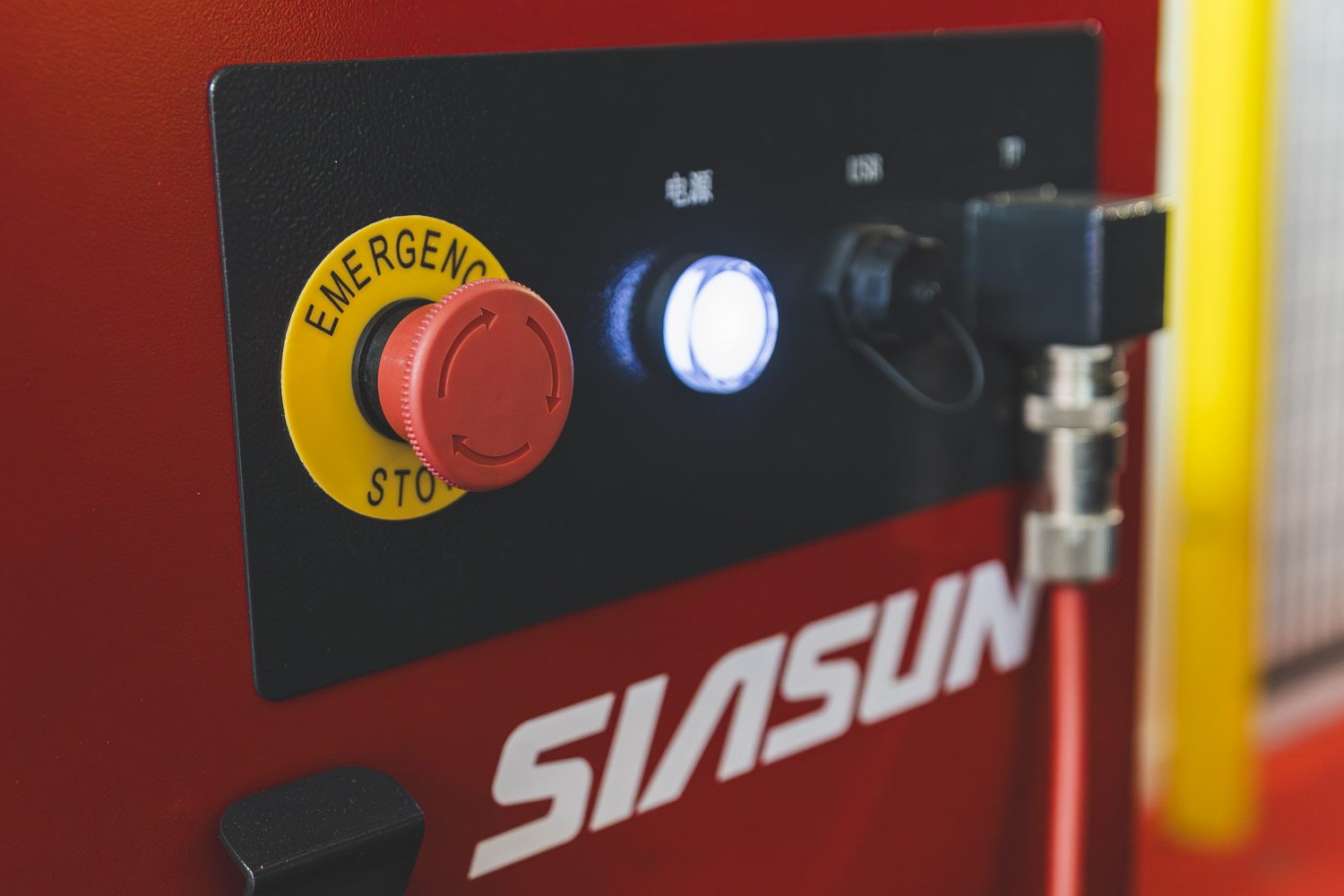
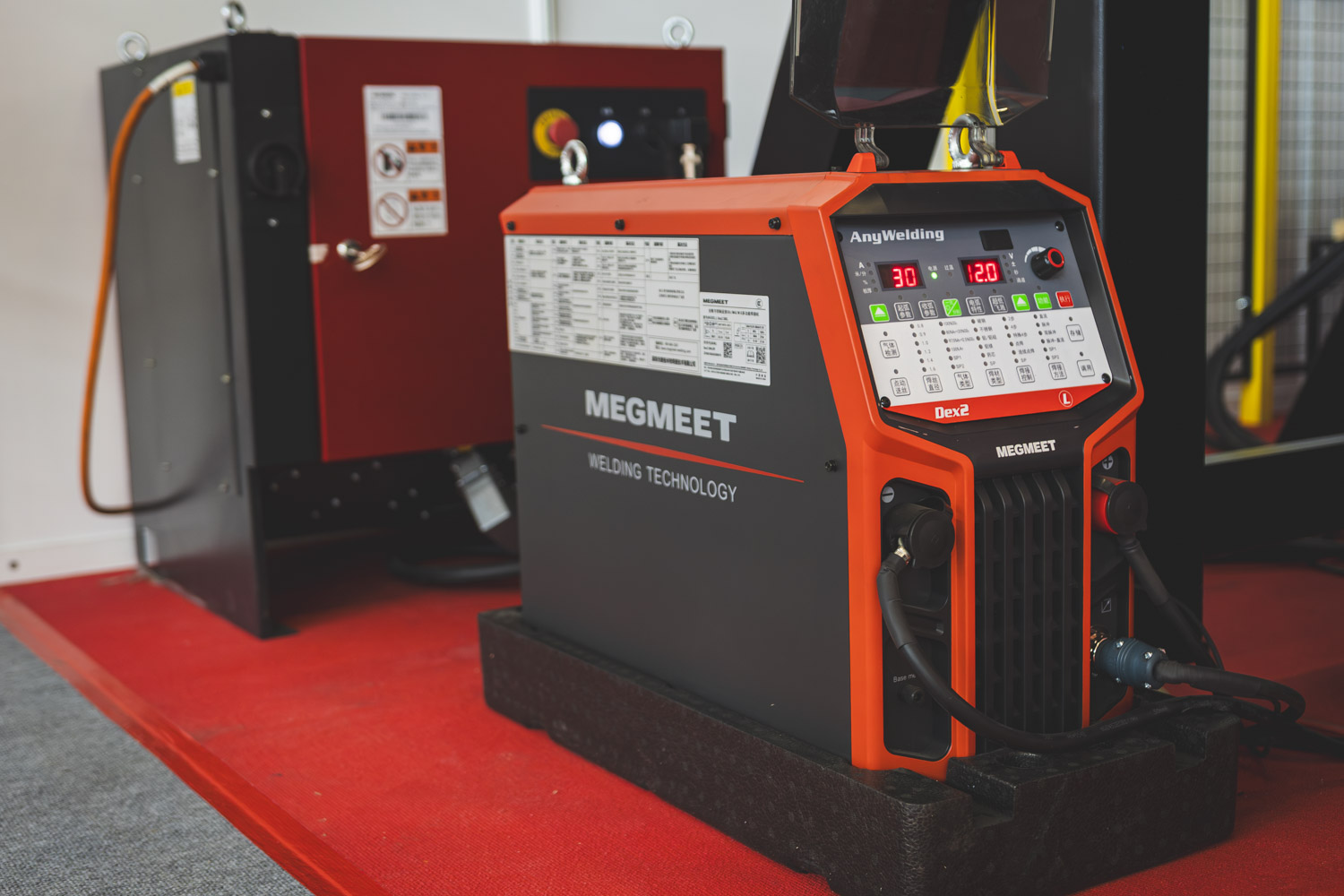
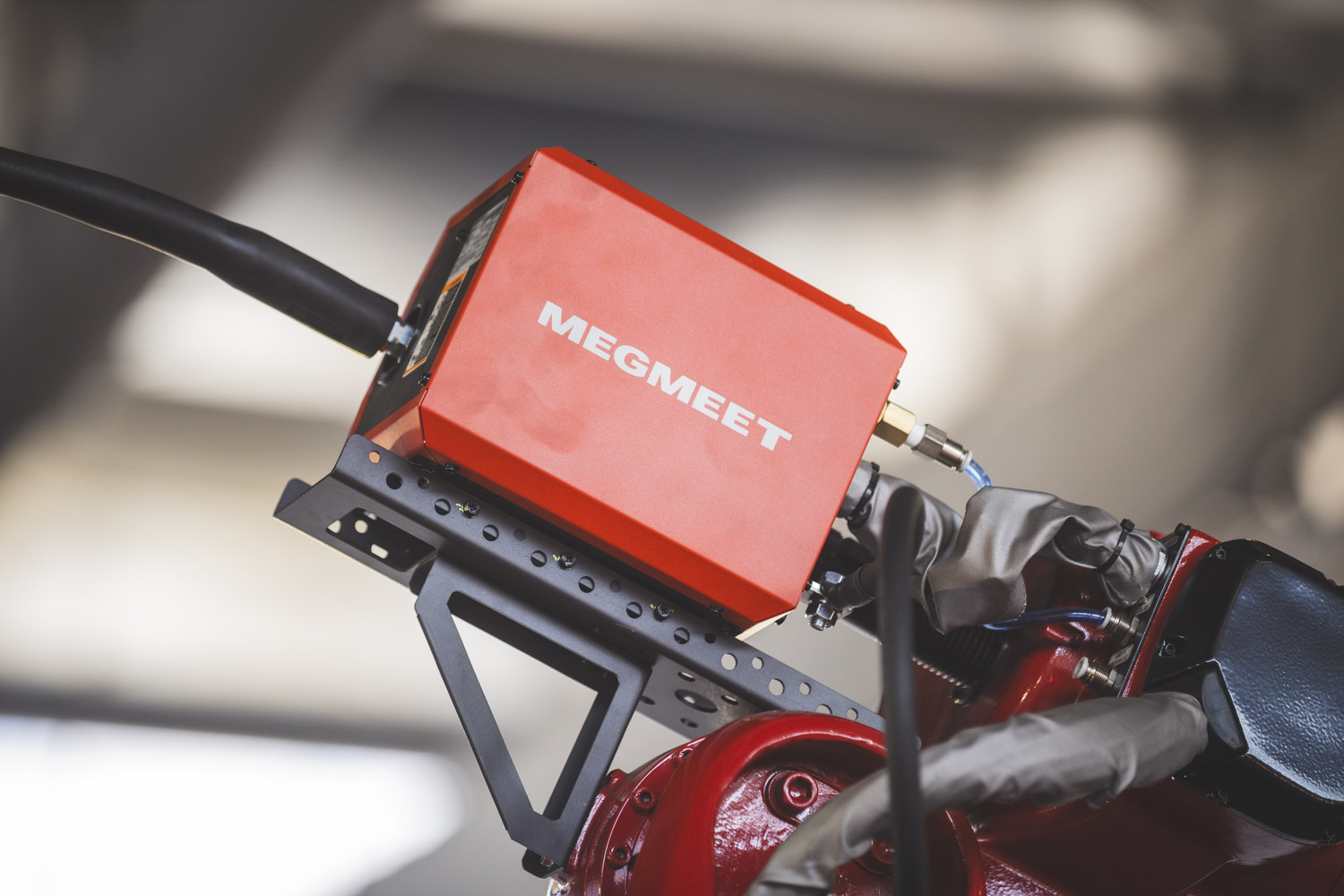
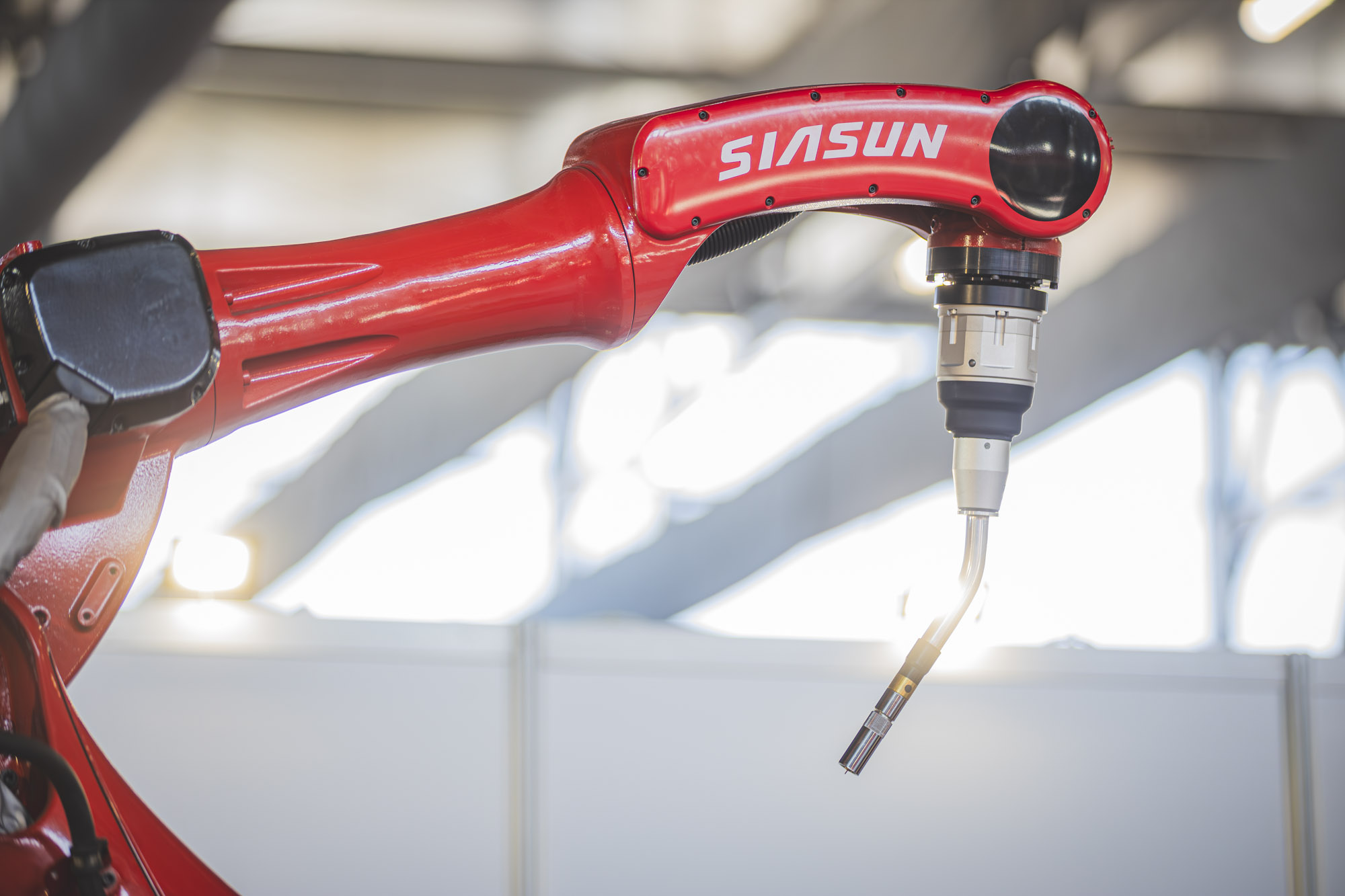
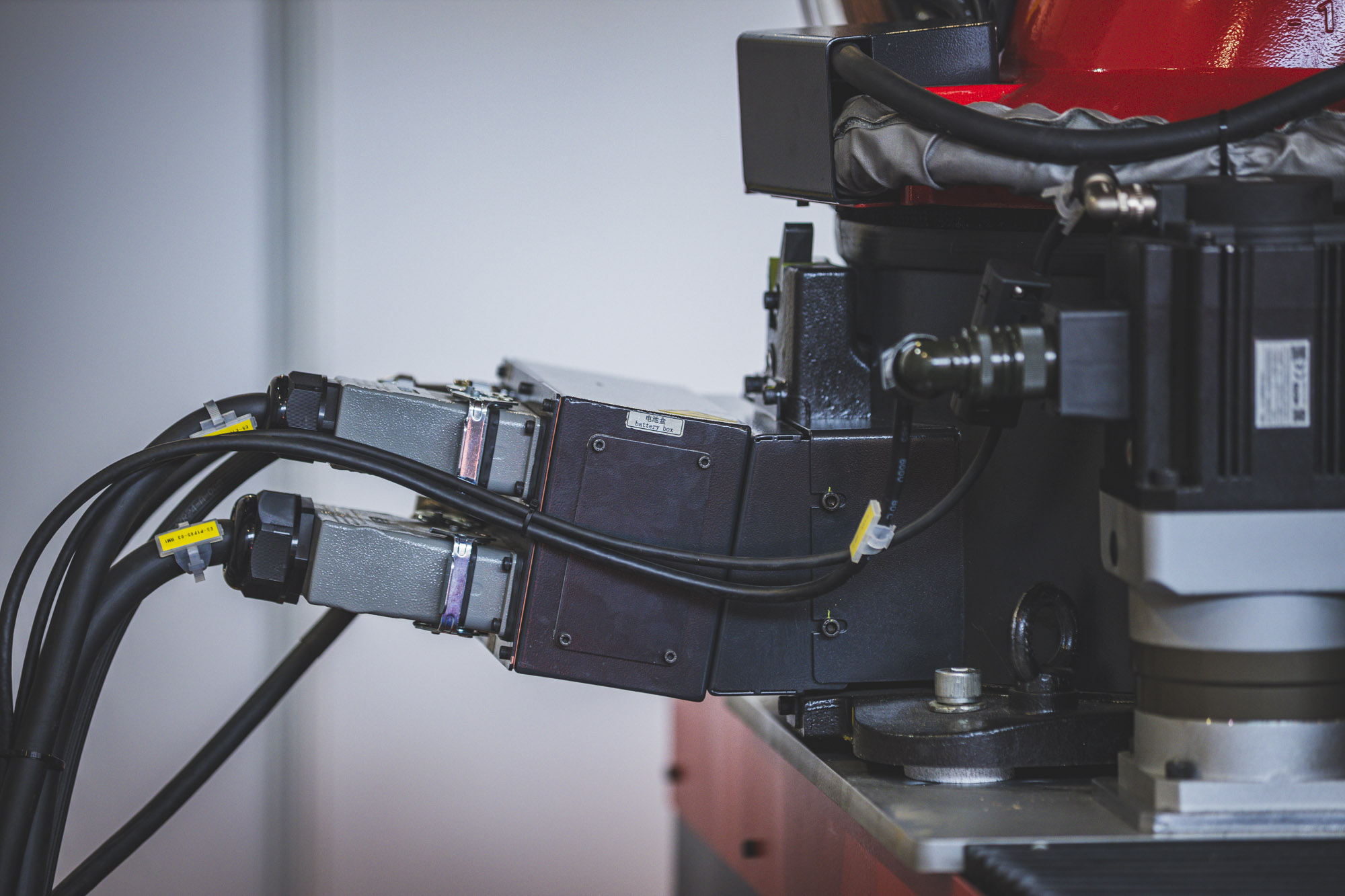

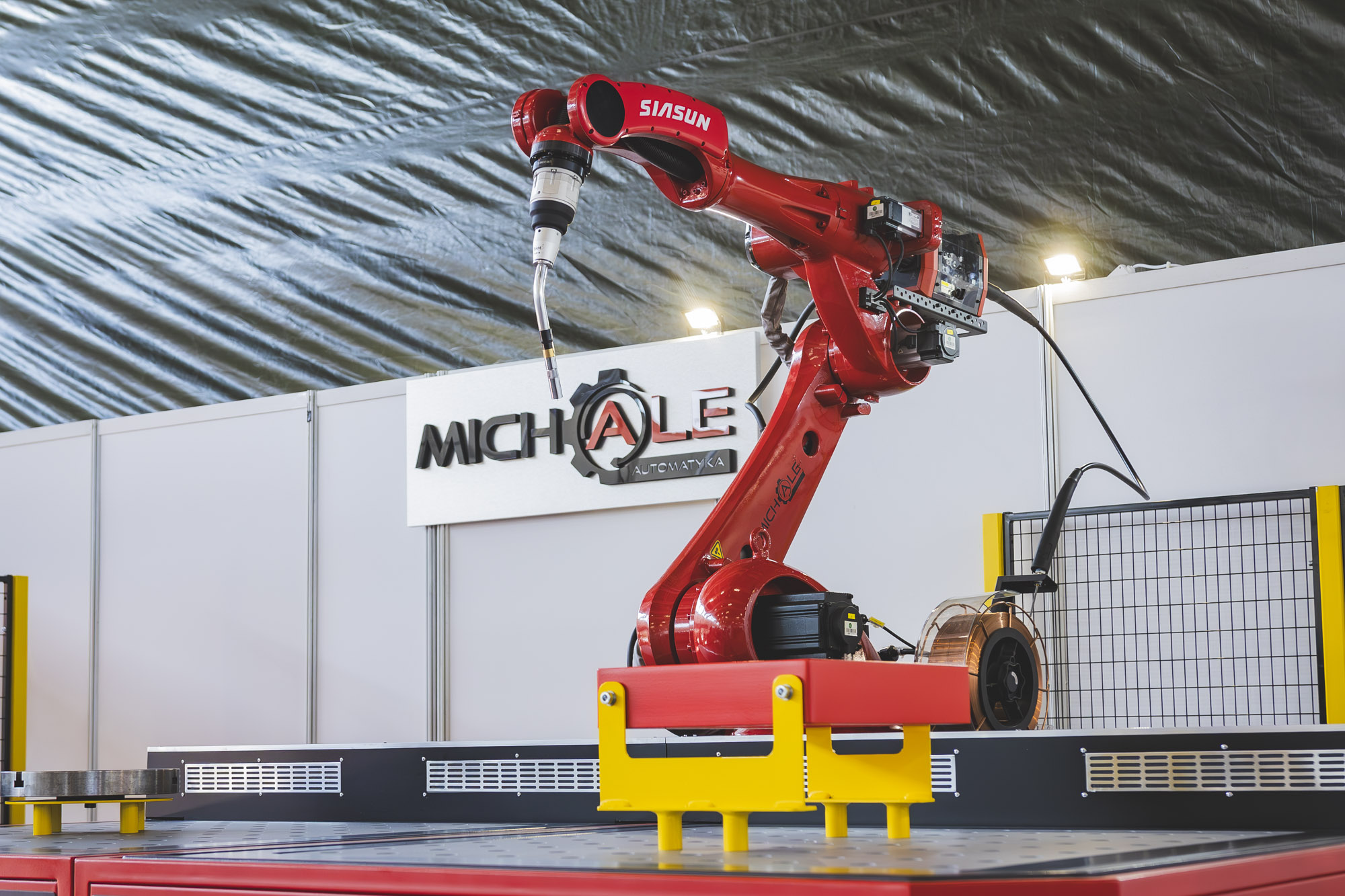
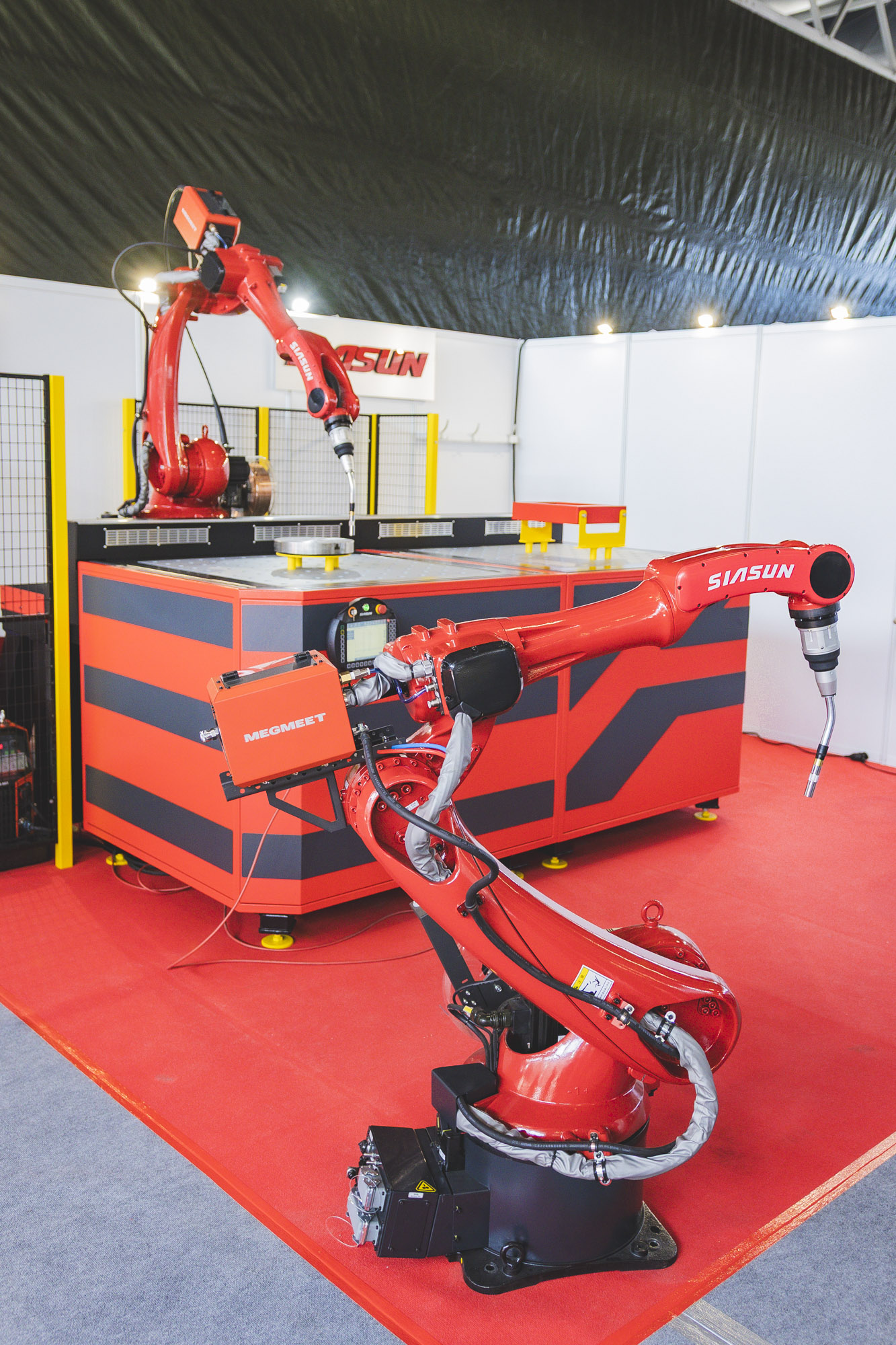
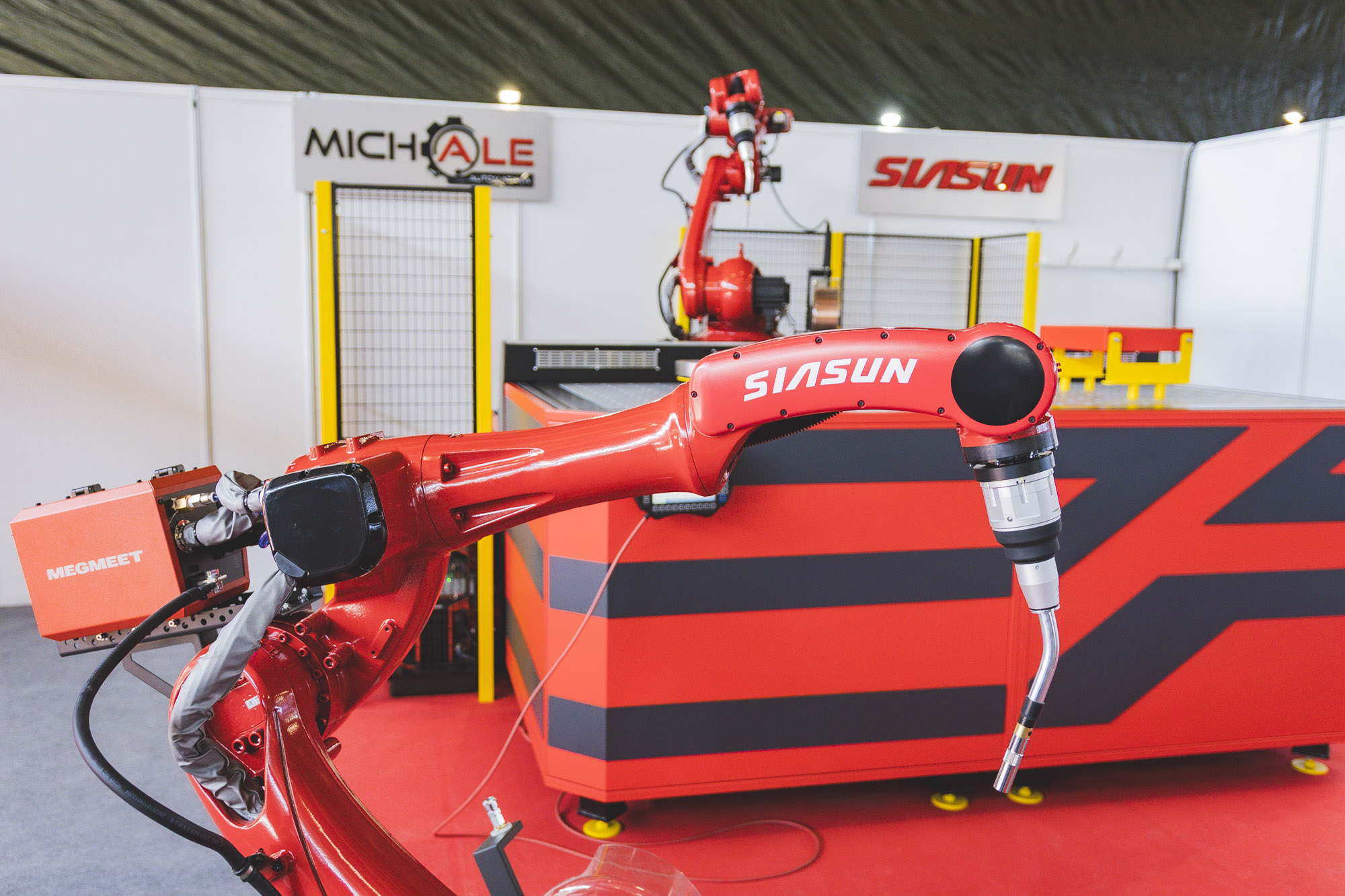
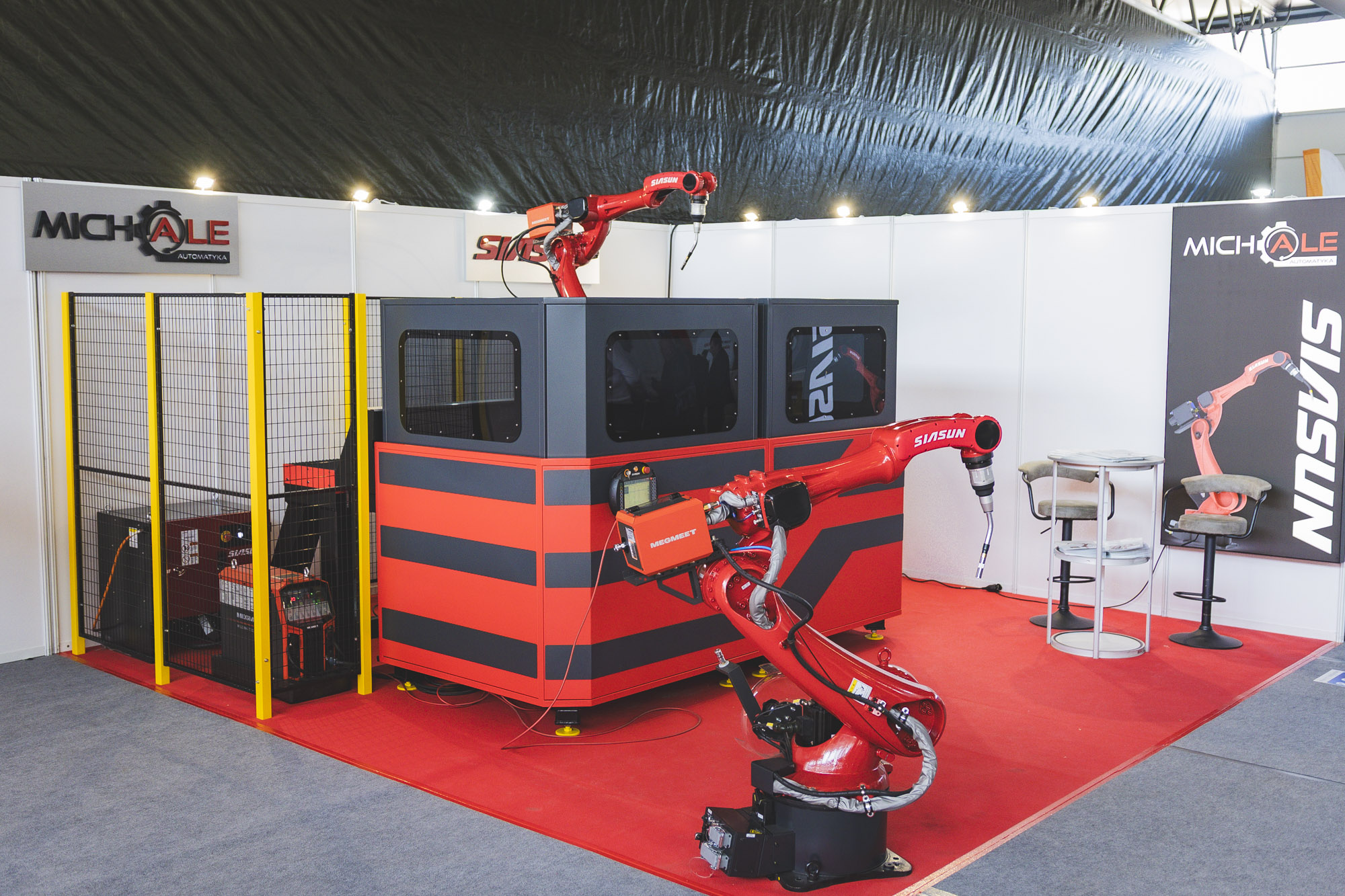
Ready for collaboration?
Make an appointment valuation
Don't wait any longer! Contact us today and find out how we can help your business reach new levels of productivity.
Contact details
Michale 88C
86-134 Dragacz
Professional training, service and maintenance of robotic workstations
We offer comprehensive training, service and maintenance of robotic workstations. Ensure the efficiency, safety and reliability of your systems with our specialist solutions. Contact us today!
Our training courses are the ideal solution for companies that want to exploit the full potential of their robotic workstations. We offer comprehensive courses tailored to the participants' level of knowledge - from basic robot operation to advanced programming and diagnostics. Thanks to our training courses, your employees will acquire the necessary skills, which will translate into greater efficiency and safety in the workplace.
- Professional training for operators and technicians operating robotic workstations.
- Increase team competence and optimise production processes.
We provide a professional service for robotic workstations, which includes diagnosis, repair and replacement of faulty components. Our team of skilled technicians works quickly and efficiently, minimising production downtime. We use only original spare parts, which guarantees the durability and reliability of the repaired equipment.
- Diagnostics and repair of robotic systems by qualified specialists.
- Rapid troubleshooting and minimising production downtime.
Regular maintenance is key to maintaining the high performance and long life of robotic systems. We offer comprehensive technical inspections to detect potential problems early and prevent costly breakdowns. Our services include cleaning, lubrication, calibration and replacement of worn components - all to keep your workstations running smoothly for many years to come.
- Regular maintenance and replacement of worn components.
- Ensuring reliability and extending the life of equipment.
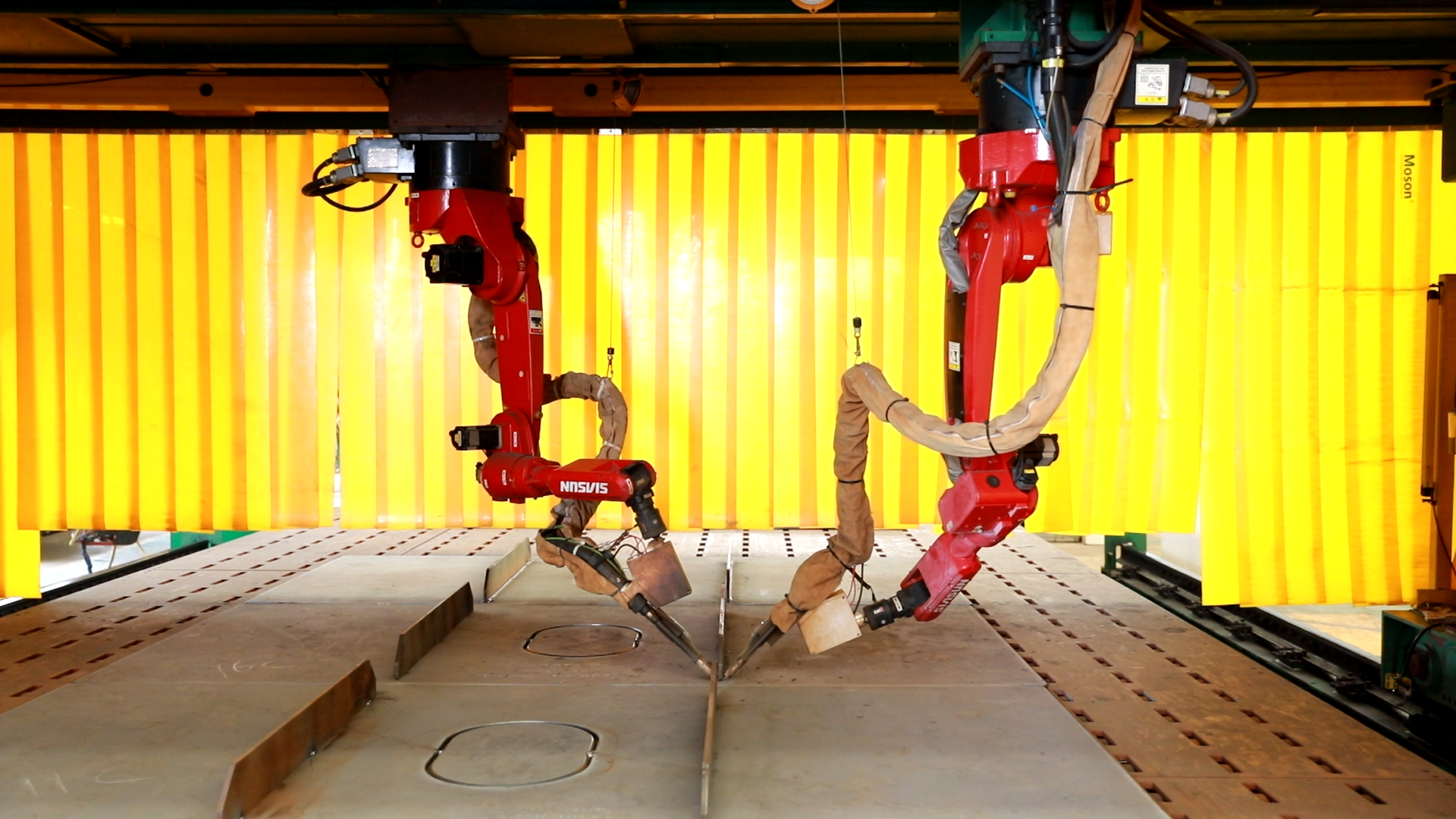
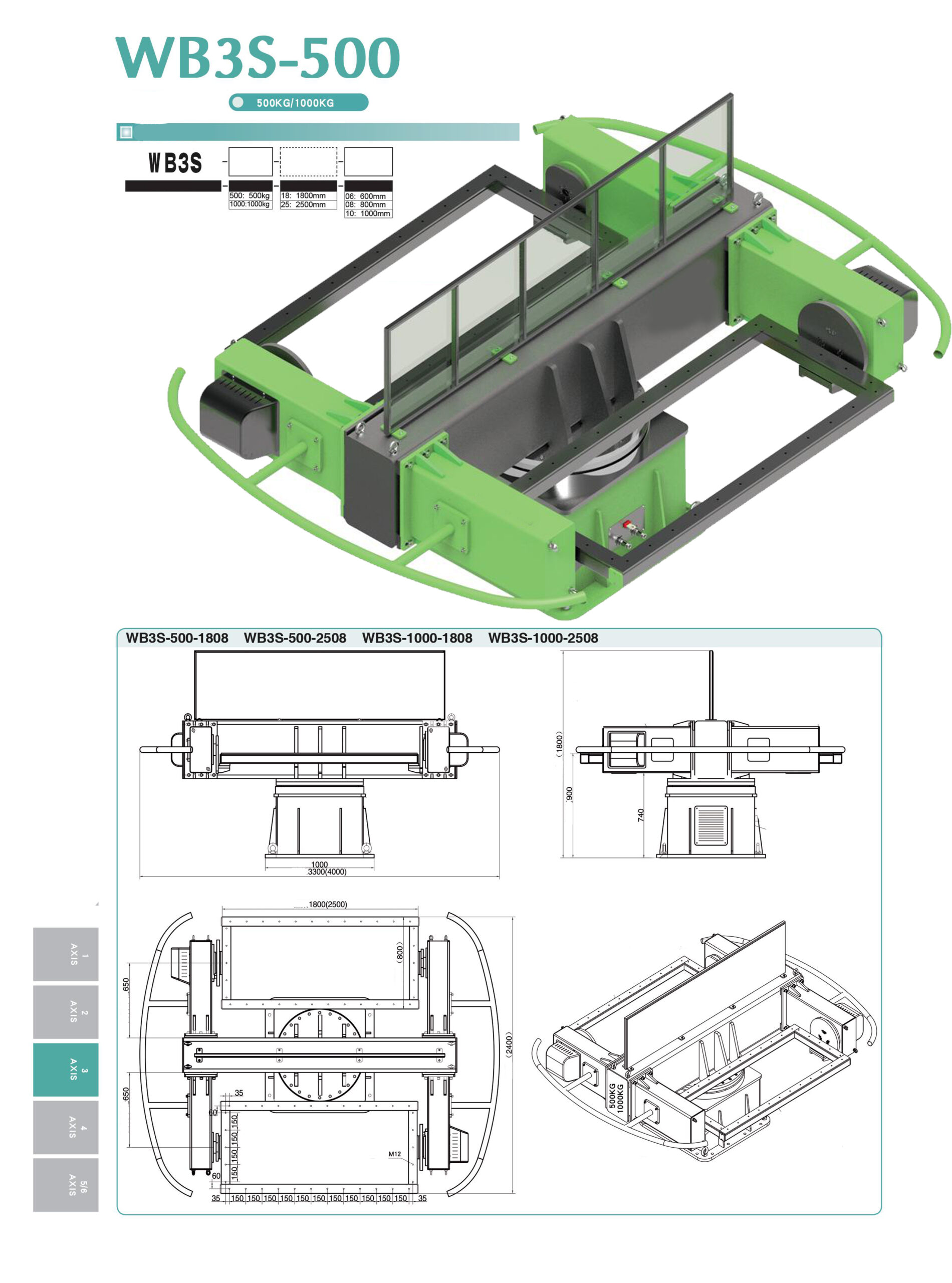
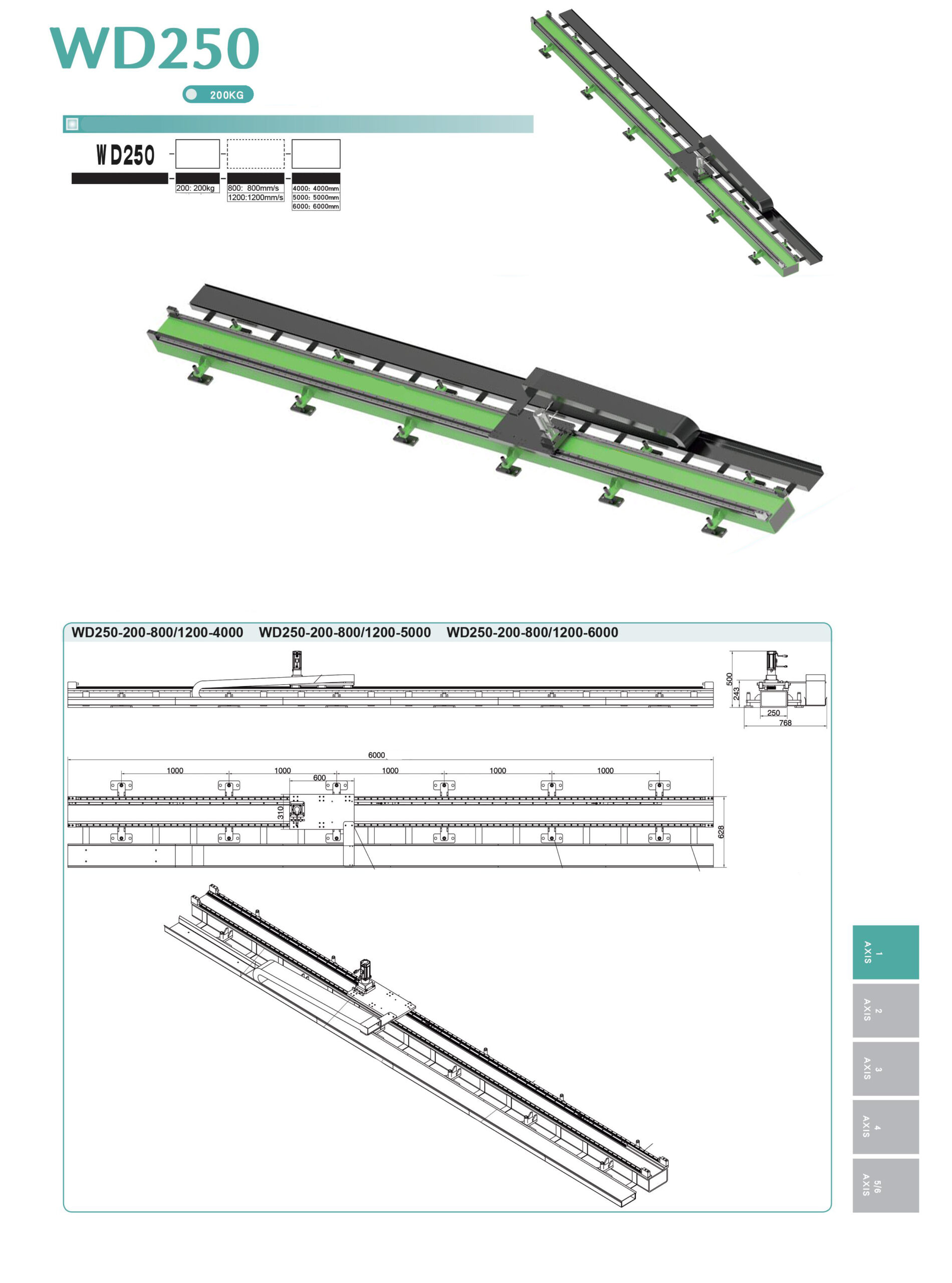

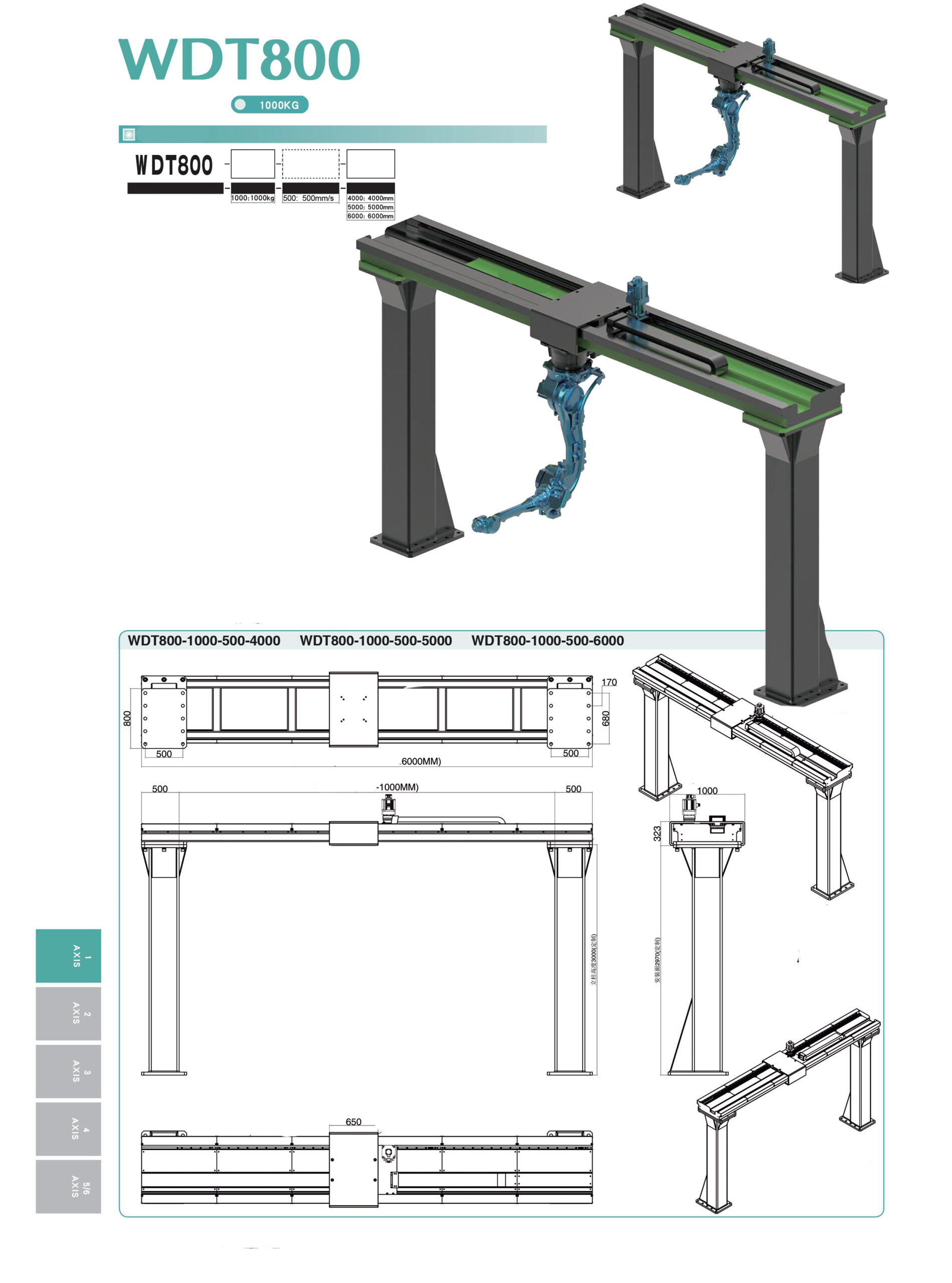
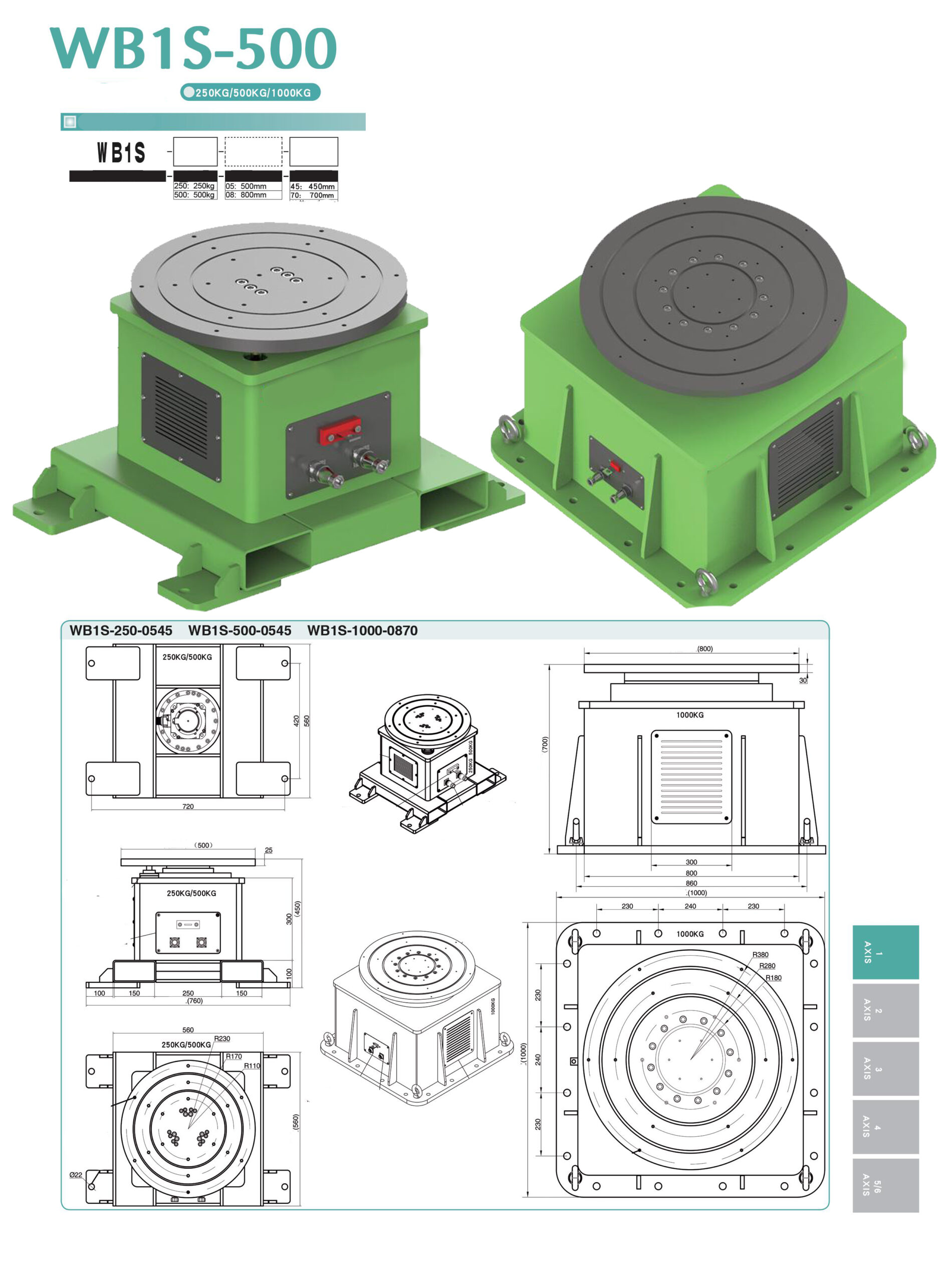
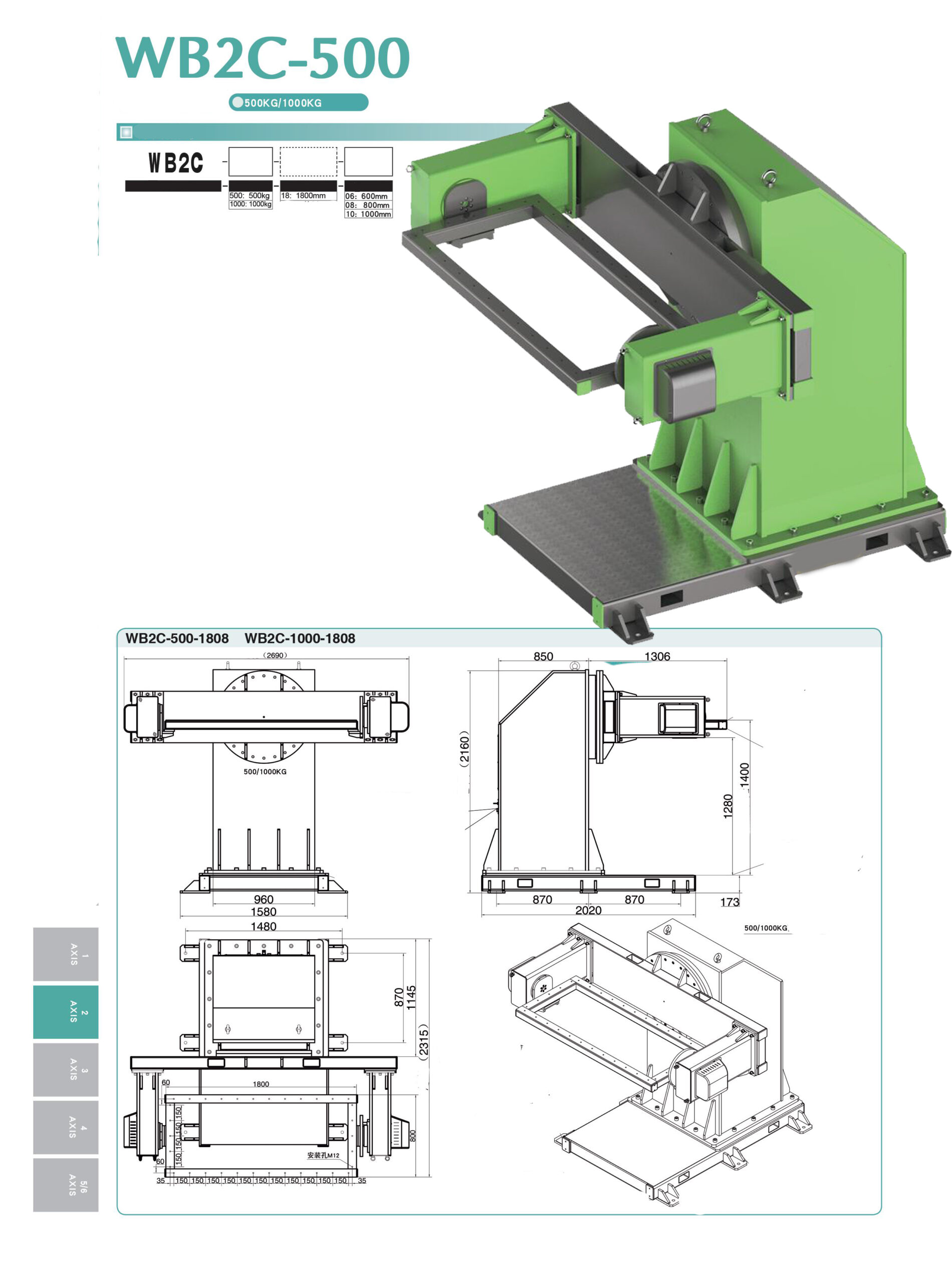
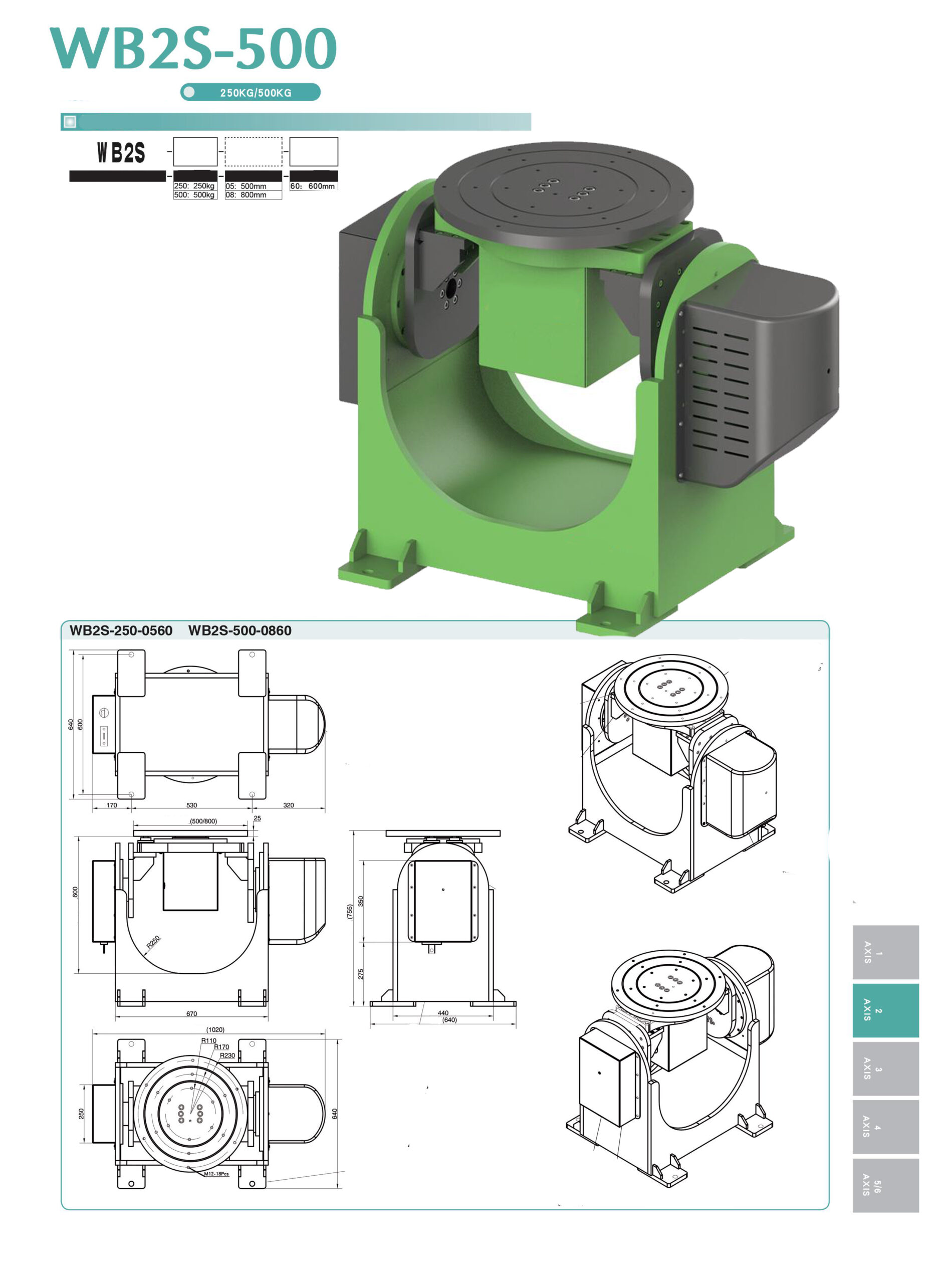
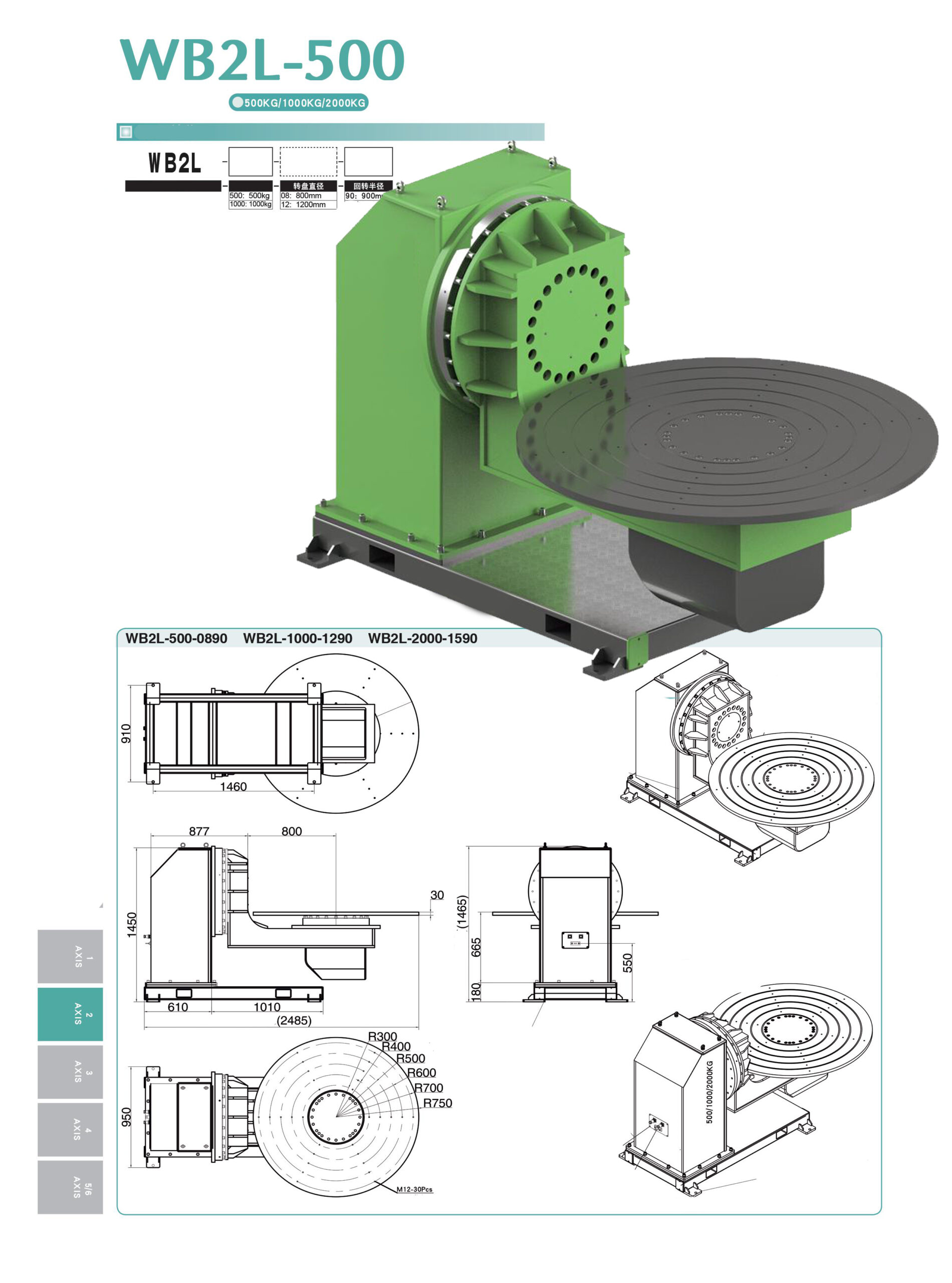
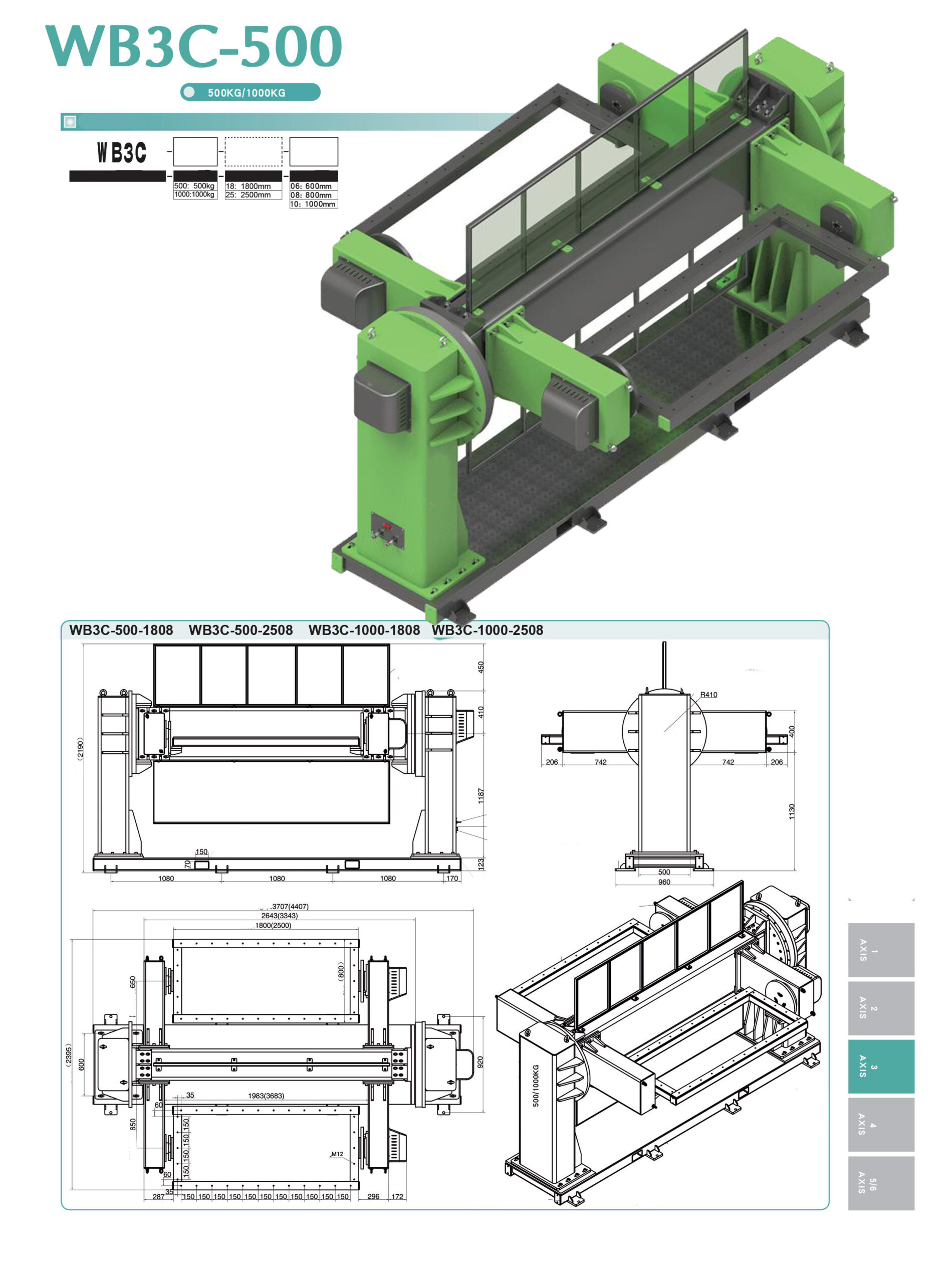
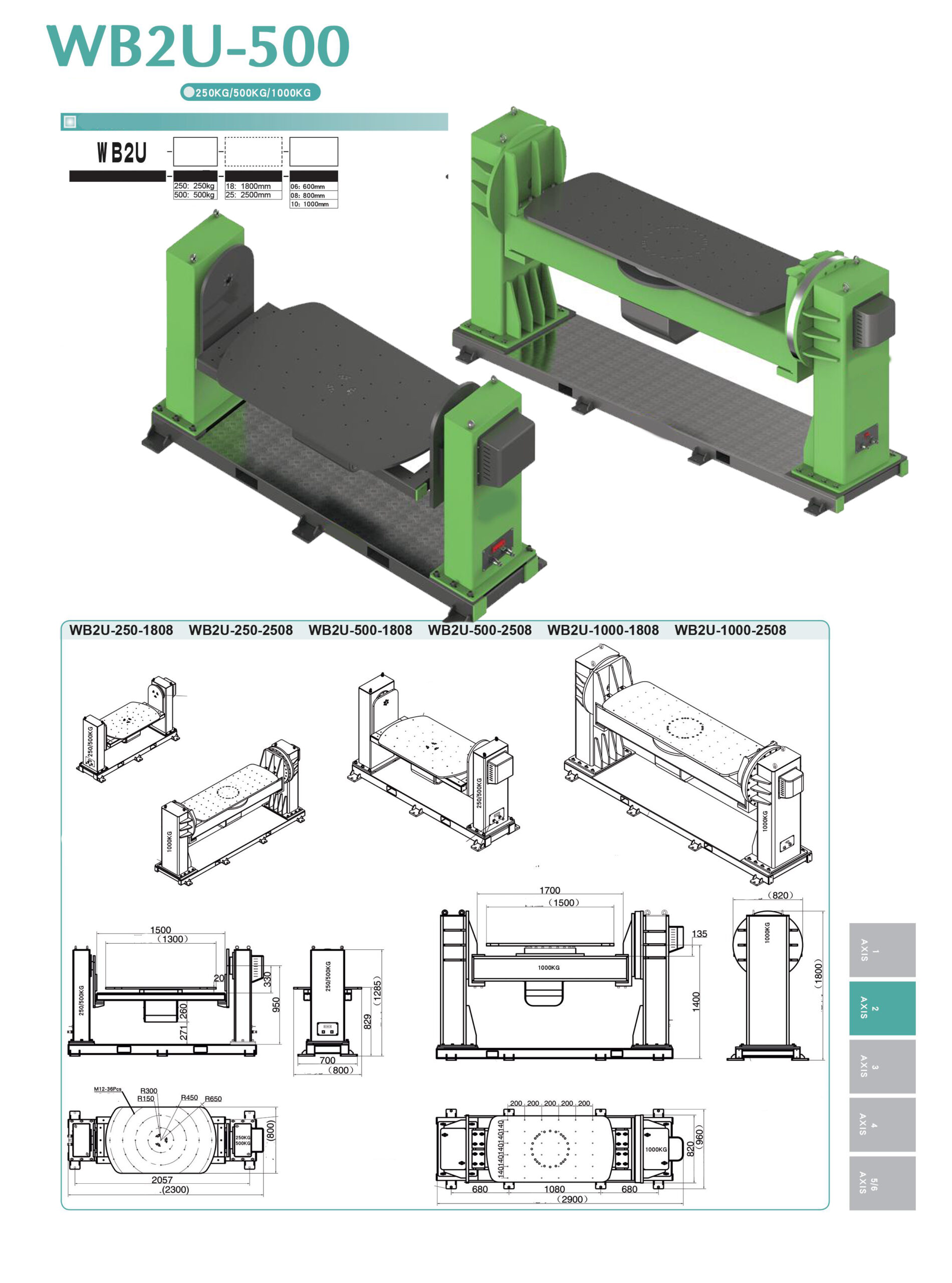
Additional equipment for robot workstations
We can equip robotic workstations with additional accessories. With the right selection of accessories, it is possible to increase the efficiency, safety and versatility of production processes.
Application of welding workstations
Robotising repetitive production is the key to increasing the efficiency, precision and reliability of your company's processes. Automated workstations eliminate errors, speed up tasks and ensure repeatable product quality. Our end-to-end solutions - from design to implementation and service - are fully tailored to the specifics of your production. By robotising repetitive processes, your company gains a competitive edge, saves time and optimises costs.
- Automotive industry
- Steel industry
- Shipbuilding industry
- And wherever there are welded components
- Pass-through 6 axles
- Stationary 6 axes
- Suspended 6 axes
- Designed for welding carbon steel
- Designed for welding aluminium
- Designed for welding stainless steel
- Welding cell
- Automatic feeder
- Answering machine
- Cleaning station (burner preparation)
- Swivels and positioners
- Operating panel
- Robot base
- Protection fences
- Training
- Service
- Maintenance
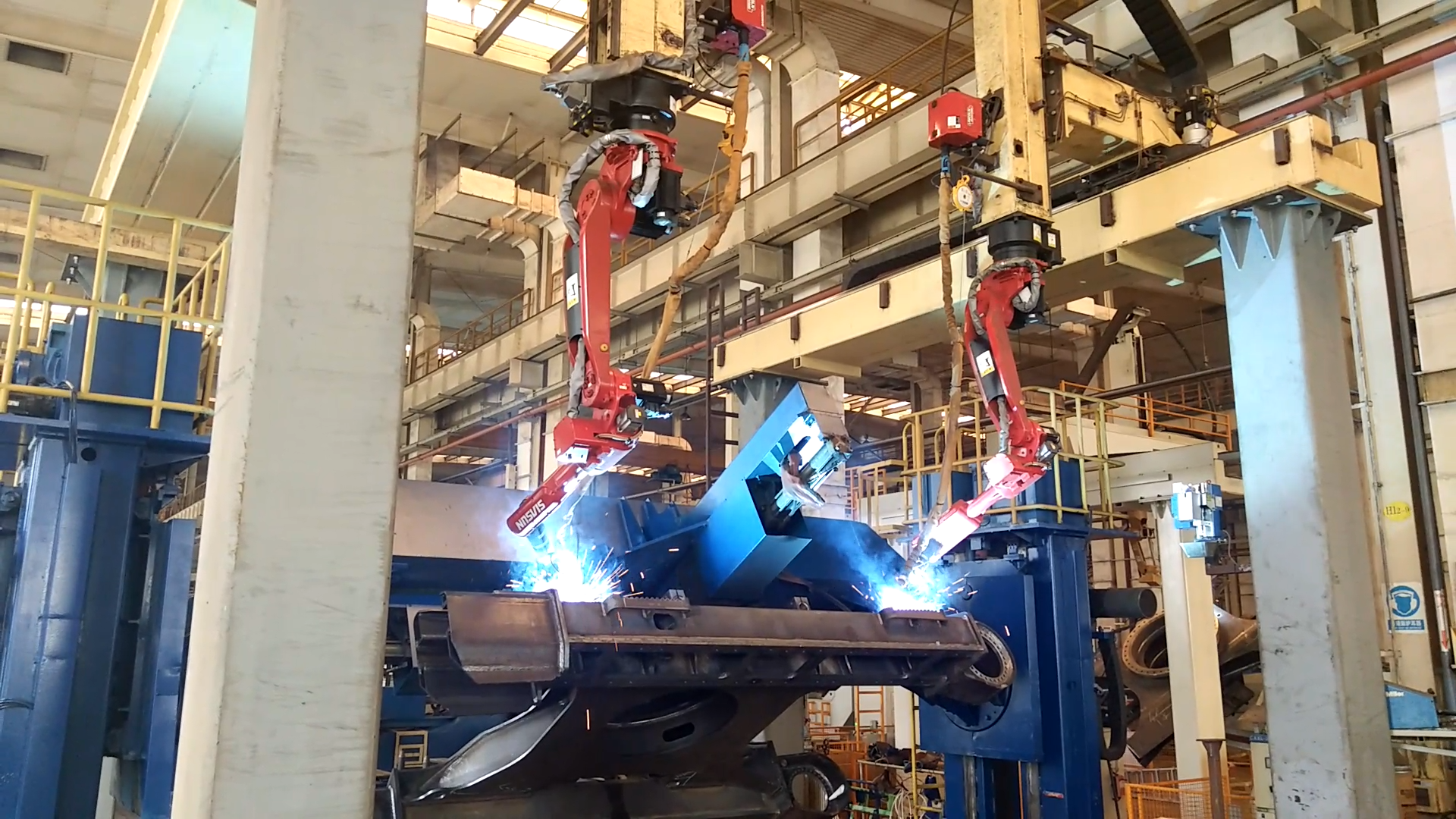
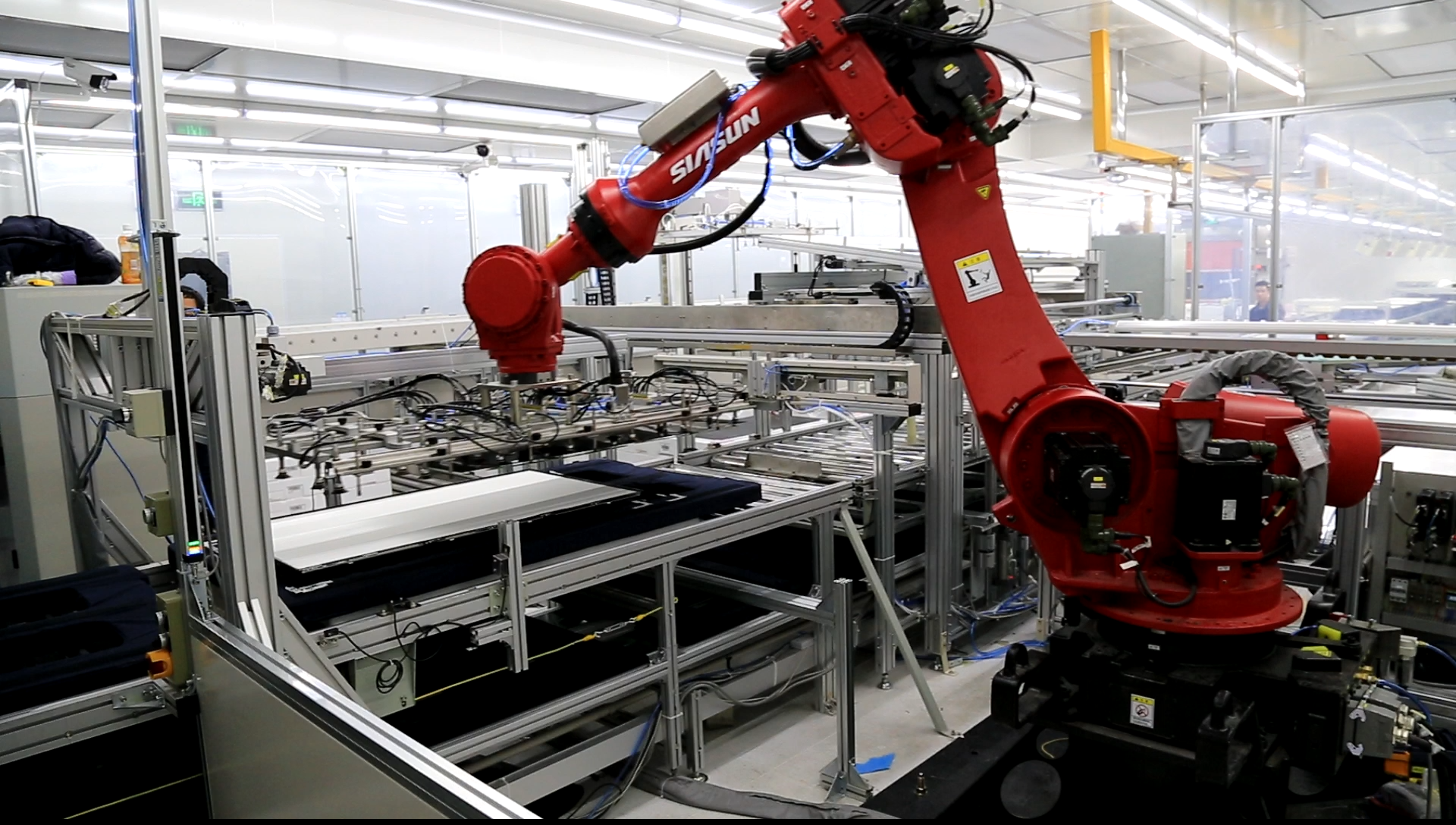
Application of packaging stations
Robotising repetitive production is the key to increasing the efficiency, precision and reliability of your company's processes. Automated workstations eliminate errors, speed up tasks and ensure repeatable product quality. Our end-to-end solutions - from design to implementation and service - are fully tailored to the specifics of your production. By robotising repetitive processes, your company gains a competitive edge, saves time and optimises costs.
- Food industry
- Paper industry
- Manufacturing industry palletised packaging
- Picking up packaged products from the production line
- Stacking of products in cartons
- And wherever there is repetitive production
- Pass-through 6 axles
- Stationary 6 axes
- Suspended 6 axes
- Designed for packaging - bags, cartons, etc.
- Operating panel
- Robot base
- Protection fences
- Carton and bag grippers
- Vacuum suction cups for handling various products
- Training
- Service
Use of grinding stands
Robotising repetitive production is the key to increasing the efficiency, precision and reliability of your company's processes. Automated workstations eliminate errors, speed up tasks and ensure repeatable product quality. Our end-to-end solutions - from design to implementation and service - are fully tailored to the specifics of your production. By robotising repetitive processes, your company gains a competitive edge, saves time and optimises costs.
- Furniture industry
- Steel industry
- Metal casting
- Glass industry
- And wherever components are ground
- Pass-through 6 axles
- Stationary 6 axes
- Suspended 6 axes
- Suitable for machining steel, aluminium, etc.
- Oscillation of steel plates, stainless steel, aluminium etc.
- Polishing of furniture tops
- Surface sanding
- Edge-breaking
- Grinding of castings
- Grinding of welds
- Grinding cell
- Dust extraction
- Turntable
- Swivels and positioners
- 3 types of grinding heads
- Abrasive magazine for automatic abrasive collection
- Operating panel
- Protection fences
- Training
- Service
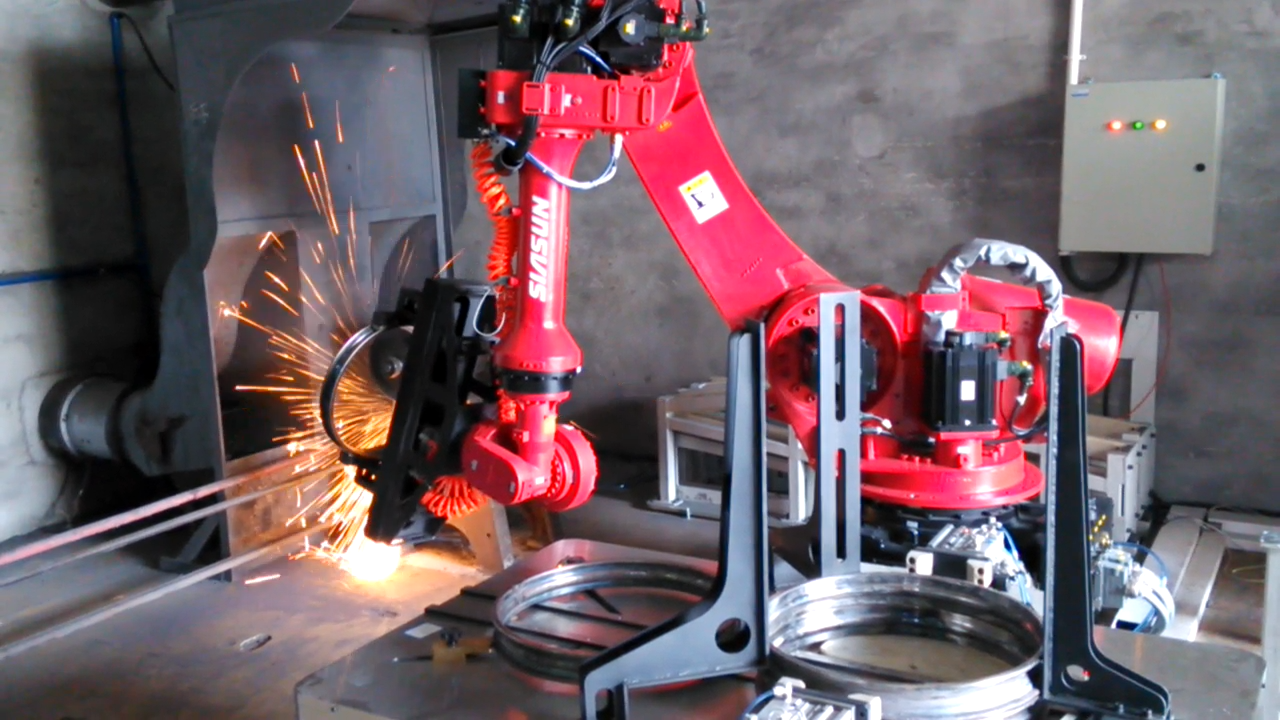
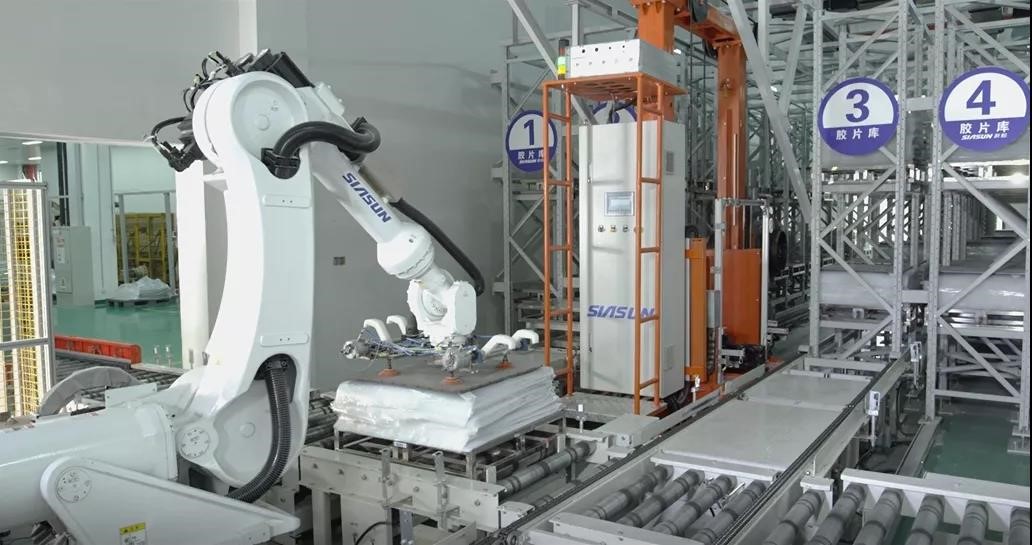
Application of stacking positions
Robotising repetitive production is the key to increasing the efficiency, precision and reliability of your company's processes. Automated workstations eliminate errors, speed up tasks and ensure repeatable product quality. Our end-to-end solutions - from design to implementation and service - are fully tailored to the specifics of your production. By robotising repetitive processes, your company gains a competitive edge, saves time and optimises costs.
- Powder coating plants
- Wet paint shops
- Pass-through 6 axles
- Stationary 6 axes
- Suspended 6 axes
- Powder coating of profiles, steel pipes
- Powder coating of all parts where there is repeat production
- Painting of furniture fronts
- Wet painting
- Protection fences
- Automatic pistols
- Operating panel
- Training
- Service
Application of paint stands
Robotising repetitive production is the key to increasing the efficiency, precision and reliability of your company's processes. Automated workstations eliminate errors, speed up tasks and ensure repeatable product quality. Our end-to-end solutions - from design to implementation and service - are fully tailored to the specifics of your production. By robotising repetitive processes, your company gains a competitive edge, saves time and optimises costs.
- Automotive industry
- Steel industry
- Shipbuilding industry
- And wherever there are welded components
- Pass-through 6 axles
- Stationary 6 axes
- Suspended 6 axes
- Designed for welding carbon steel
- Designed for welding aluminium
- Designed for welding stainless steel
- Welding cell
- Automatic feeder
- Answering machine
- Cleaning station (burner preparation)
- Swivels and positioners
- Operating panel
- Robot base
- Protection fences
- Training
- Service
- Maintenance
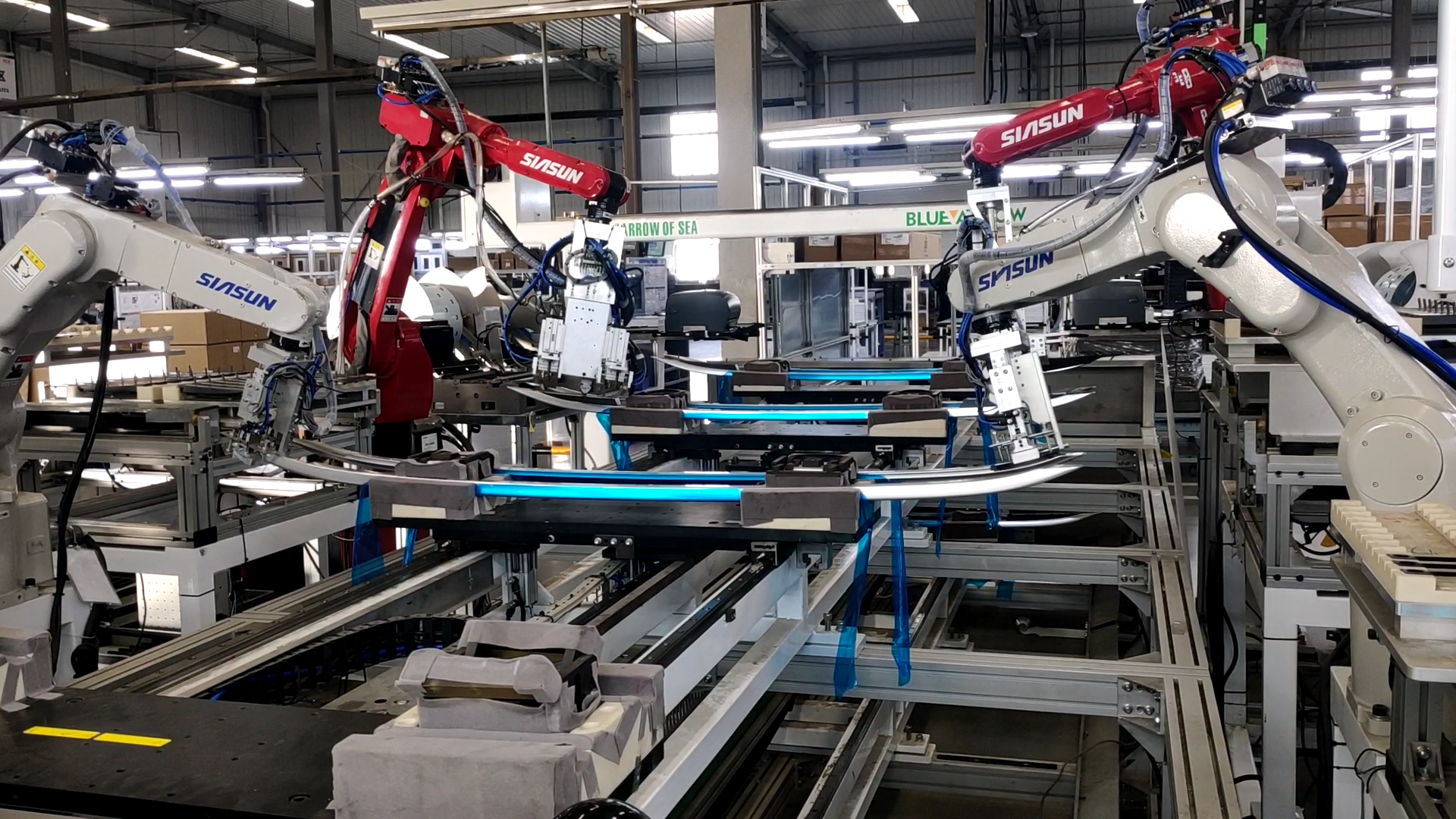
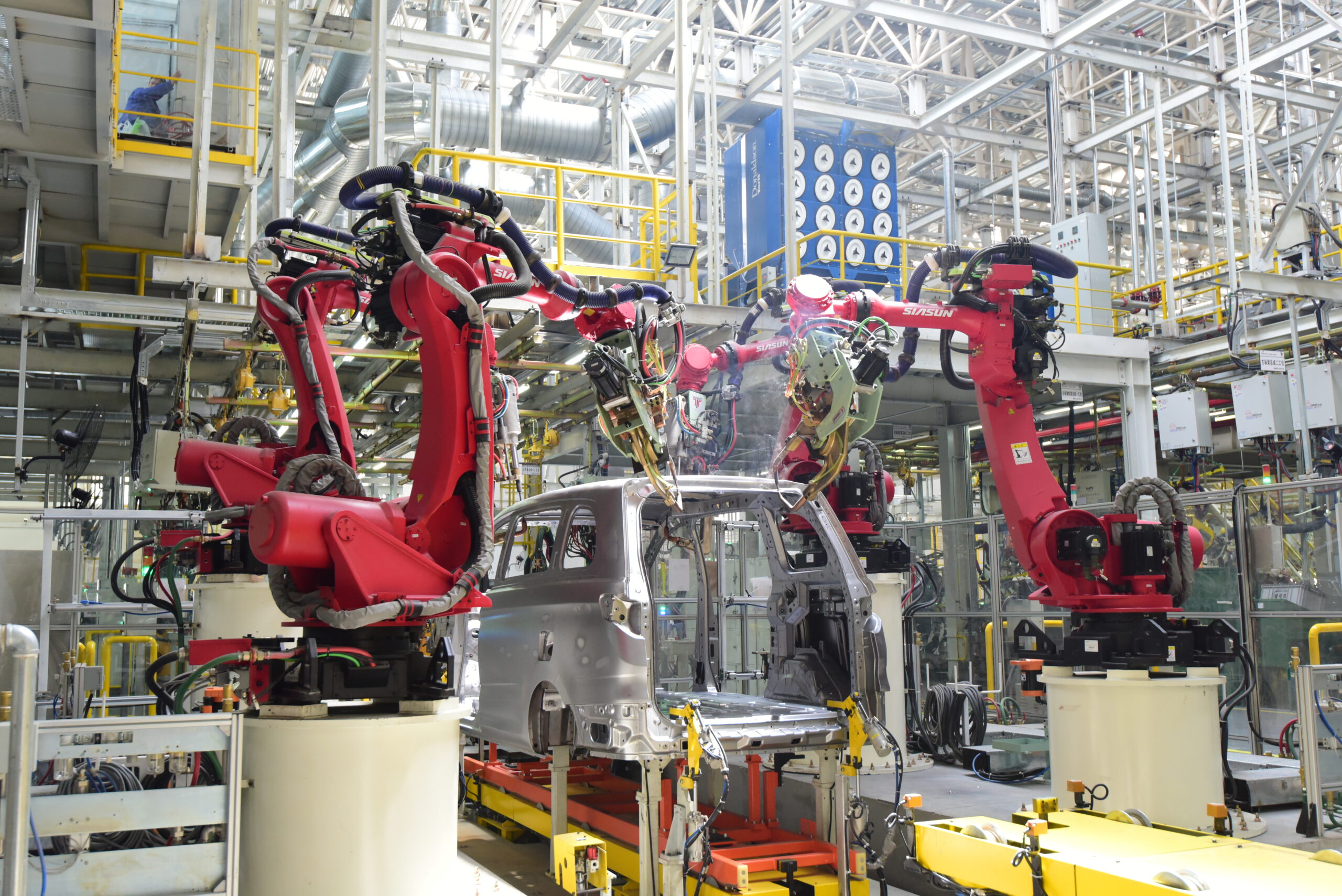
Application of universal robot workstations
Robotising repetitive production is the key to increasing the efficiency, precision and reliability of your company's processes. Automated workstations eliminate errors, speed up tasks and ensure repeatable product quality. Our end-to-end solutions - from design to implementation and service - are fully tailored to the specifics of your production. By robotising repetitive processes, your company gains a competitive edge, saves time and optimises costs.
- Used wherever there is continuous production
- They can be used for feeding, positioning, moving materials, stacking and much more
- Pass-through 6 axles
- Stationary 6 axes
- Suspended 6 axes
- Welding cell
- Automatic feeder
- Answering machine
- Cleaning station (burner preparation)
- Swivels and positioners
- Operating panel
- Robot base
- Protection fences
- Training
- Service
- Maintenance
Advantages
Intelligent control and easy maintenance - maximum performance with minimum effort!
Increased operational flexibility
The hollow arc-shaped arm design is an innovative solution that effectively minimises interference with workpieces. This gives the robot greater flexibility in operation, especially in complex production environments. This design allows for more precise and smoother operations, resulting in higher quality tasks and better use of the workspace. It is the ideal solution for companies that focus on maximum efficiency and reliability in difficult environments.
High-performance power supply system
The system offers exceptional dynamic capabilities, meeting stringent requirements for high precision, speed and stability. This is particularly important for fast production schedules, where every second counts. Not only does the robot guarantee reliable operation, but it also optimises processes to increase productivity and reduce downtime. This enables companies to achieve higher levels of productivity and meet the demands of modern industry.
Lightweight and integrated design
A specialised aluminium alloy casting process, also used in the manufacture of automotive engines, is used in the production of the robots, allowing a significant reduction in the weight of the device. In addition, the integration of the wire feeder into the robot body not only reduces its overall weight, but also improves wire feeding stability and welding quality. The result is more precise and durable welding that meets the highest quality standards. This solution is ideal for companies looking for technology that combines lightweight construction with unparalleled performance.
Versatile use and flexible mounting options for tight spaces
The robot can be mounted both on a table and in a suspended position, making it an extremely versatile solution. This feature makes it ideal for operations in confined spaces and areas with a tight turning radius. The flexibility of mounting allows the robot to be easily adapted to the specific requirements of the working environment, increasing its functionality and efficiency in a variety of industrial applications.
Next-generation intelligent welding control system
The robot is equipped with an advanced intelligent control system that significantly simplifies the maintenance and management of the machine. Intuitive technological solutions allow problems to be diagnosed quickly and downtime to be minimised. As a result, companies can enjoy operational continuity and reduced running costs, resulting in a greater return on investment.
Comprehensive solutions for the welding sector
Our solutions are based on the implementation of a next-generation welding control system that combines advanced technology with digital welding equipment. With a unified design approach, we ensure full integration of all system components, resulting in reliable, precise and efficient welding processes.
Realised projects - our business card
We are proud to present examples of our implementations that have helped our clients achieve tangible business benefits
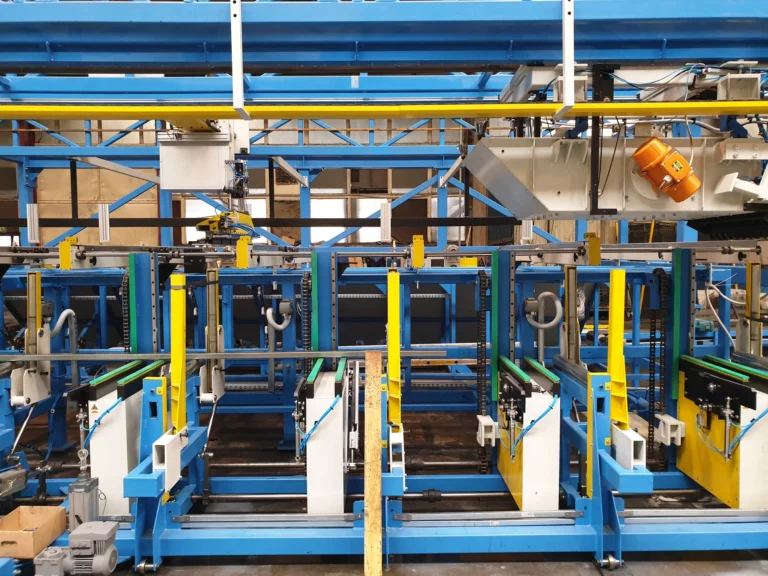
Packaging system
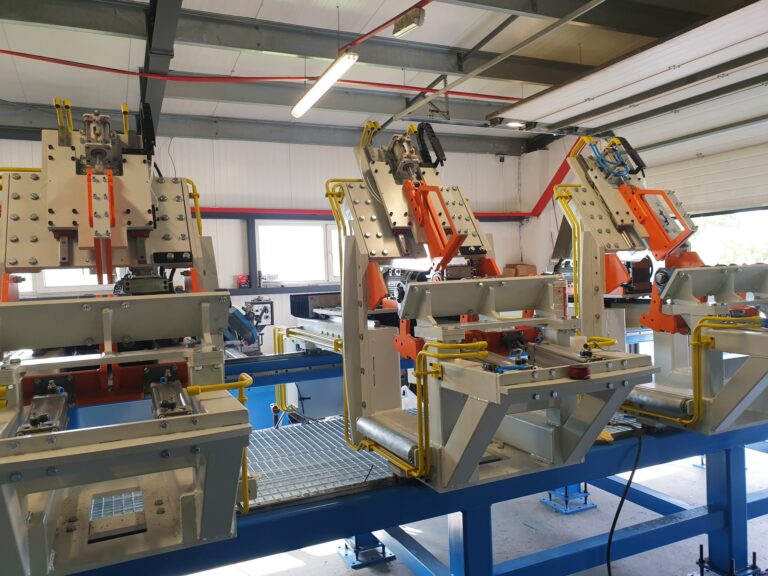
6-head saw
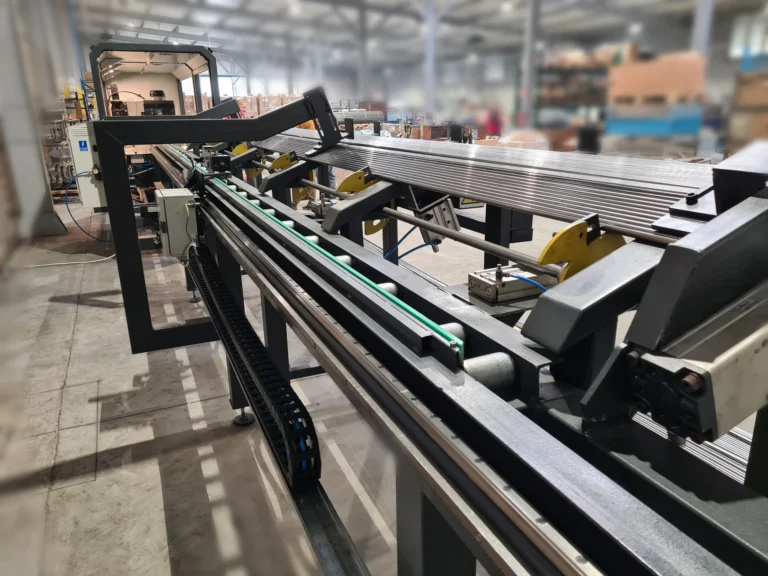
Saw with feeder
Tailor-Made Complex Stations
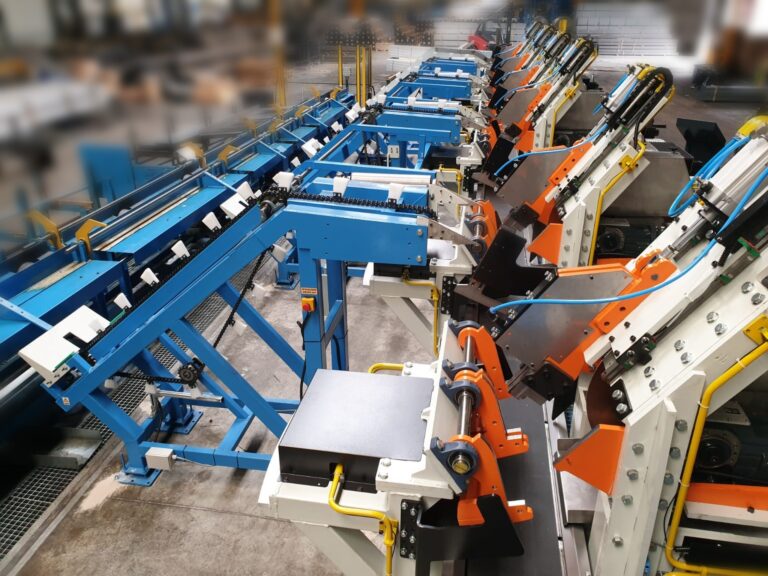
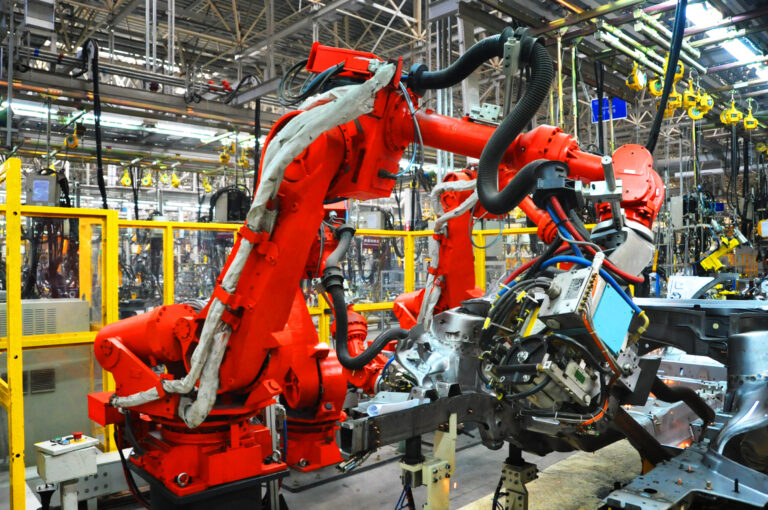
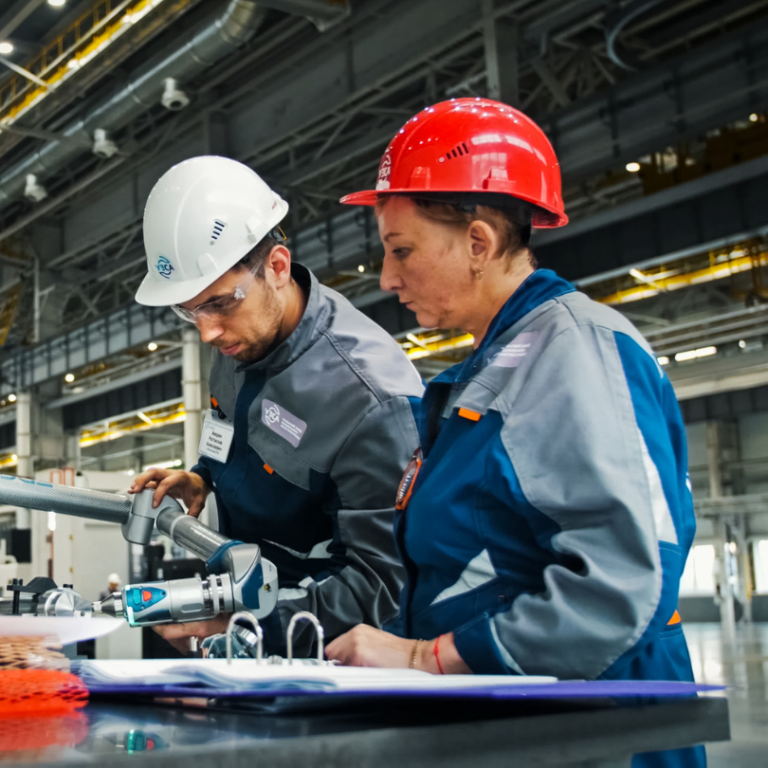
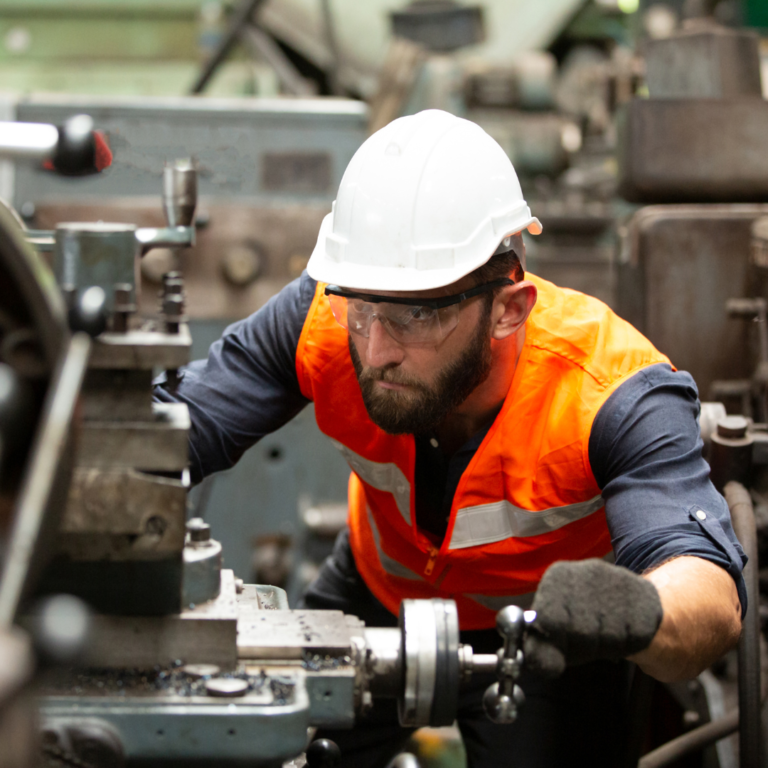
Customer feedback



Our blog

5 myths about the robotisation of manufacturing broken down into facts and figures
5 myths about manufacturing robotisation dispel stereotypes. Find out how automation increases efficiency and flexibility in every industry
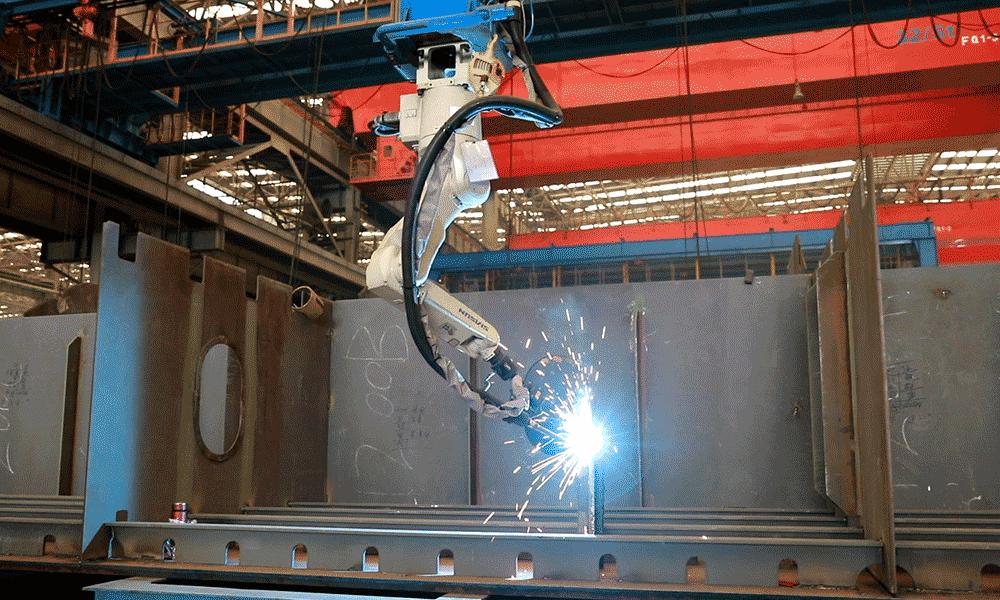
Robotic welding: the future of industry
Robotic welding is the key to efficient production, increasing precision and production efficiency while reducing costs.